 |
 |
Common
Manure Handling Systems
Back
to Poultry Menu
Litter
Poultry manure is handled as a solid litter, either deposited directly
by animals on pastureland, or collected in bedding placed on solid shelter
floors to absorb the urine. Some turkeys, broilers, and ducks are raised
on concrete or earthen floors. After every flock, the litter is either:
- Removed and fresh litter applied,
- Tilled and fresh litter placed on top, or
- Cake manure removed, remaining
litter tilled or mixed, and fresh litter placed on top.
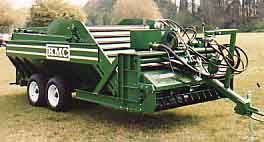 |
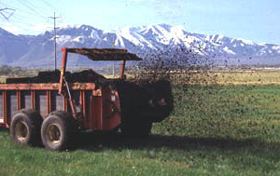 |
Tractor-drawn Decaker/Cruster |
Solid Manure Spreader |
(Source: Kelly Manufacturing Co.)
|
(Source: Purdue University)
|
Cake manure is sometimes removed with a tractor-drawn decaker/cruster
which removes the top layer of manure, breaks it apart, and separates
the larger manure particles from the finer litter particles (which are
placed back into the house). Poultry litter is normally surface
applied, but in some cases may be incorporated into the soil with a farm
tillage operation shortly after spreading.
For further information
on proper sampling of poultry litter.
Back to Top
Layer Manure - Dry
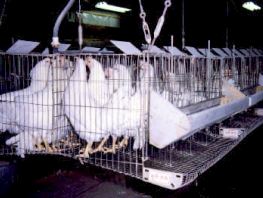 |
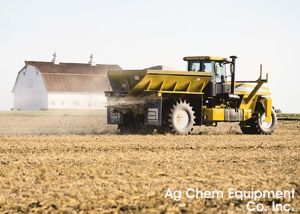 |
Laying Hens on Wire Floors |
Surface Applied Solid Manure |
(Source: Purdue University) |
(Source: Purdue University)
|
Manure from pullets and laying hens is relatively dry as it falls through
layer cages into a concrete storage area. Manure composition in these
facilities can range in dry matter between 20 and 60 percent. The storage
pit provides for long-term storage of the manure. Manure is then
typically surface applied. Composting is another option for solid manure
management.
Back to Top
Layer Manure - Semi-Solid/Liquid
Some laying hen facilities contain shallow pits with scrapers or belts,
or shallow flush pits. This manure typically can not be stacked and requires
some type of containment storage. Liquid manure that is mostly water (<
12% solids) must be kept in a watertight storage. Liquid manure can be
handled with tank trucks/wagons, injection-type spreaders, or irrigation
equipment. Semi-solid manure (12 to 20 percent solids), on the other hand,
does not flow readily but still requires containment with walls. This
type of manure can be handled easily with bucket loaders and open broadcast
spreaders. Most Midwestern states require manure storages for larger operations
to be large enough to hold six month’s accumulation. This avoids
the need to apply manure during the crop growing season and when weather
conditions are unsuitable – such as on frozen or snow-covered ground
or when the soil is wet enough that heavy application vehicles could compact
and damage the soil.
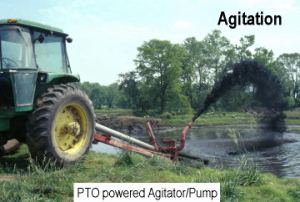 |
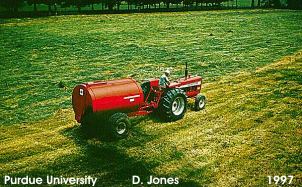 |
Liquid Manure Pit Agitation |
Surface Applied Liquid Manure |
(Source: Purdue University)
|
(Source: Purdue University)
|
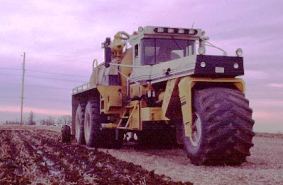 |
Injecting Liquid Manure |
(Source: Purdue University)
|
Liquid manure from storages is normally agitated thoroughly before removal
and hauled to the field for application using large tanker wagons or trucks.
Liquid manure is either applied on the soil surface or incorporated shortly
after application to control loss of volatile ammonia and release of odors.
Incorporation is very effective at controlling runoff of manure nutrients
and odor from land application if done within a few hours after application.
An alternative application method is the use of a soil injector, where liquid
manure is "injected" directly into the soil to a depth of 6 to
9" as the tanker passes over the field. This immediate contact between
the manure and soil is highly effective against the release of odors.
In larger operations, liquid manure may be pumped to nearby application
sites and irrigated onto cropland. Spray irrigating liquid manure is a
very efficient method of land application, in terms of speed and labor,
but odor emissions can be significant; therefore, it is seldom possible
to use this method in heavily populated areas.
Back to Top
Lagoons - Duck
|
Two-stage Lagoon System |
(Source: Purdue University) |
Lagoons are typically used only for laying hen production with flush-type
pit systems, and in some duck production systems. Lagoons are different
from liquid manure storages because they are operated to encourage anaerobic
digestion of organic material while it is being stored. This reduces odor
when the treated manure is land applied. A properly designed and operated
lagoon is much larger and more expensive than a liquid manure storage with
the same storage time, and should be much less concentrated, in terms of
organic solids present.
|
|
Gravity Drain, Flat Bottom Gutter |
Reverse Hairpin Flat-bottom Gutter |
(Source: Purdue University) |
(Source: Purdue University)
|
|
Recirculating Lagoon Water to Flush
Manure from a Gutter under a Slotted Floor |
(Source: Purdue University) |
In the Midwest, an equal part of relatively clean dilution water must be
added for each part manure. Furthermore, manure must be added slowly and
uniformly to the lagoon, to avoid an upset (and subsequent release of odors)
to the biological treatment system. One common method of doing this is to
utilize shallow pits or gutters under slotted floors and drain or flush
manure to the lagoon on a frequent basis, usually from three days to three
weeks. This is done by pulling a drain plug in the bottom of the pit, called
gravity drain, use of a scraper system running in the underfloor gutter,
through a process called a "hairpen" gutter or by recirculating
a volume of relatively clean effluent from the lagoon to flush manure out
of the building and into the lagoon. Recirculation involves either a flushing
action that takes place one or more times a day or a "pit recharge"
system that works basically like a toilet that is flushed every few days.
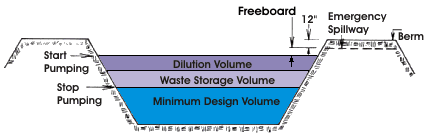 |
Single Stage Lagoon |
(Source: Purdue University) |
A portion of the lagoon contents must be left in the lagoon after contents
are pumped to the land (a minimum treatment volume) to retain a large number
of microbial organisms to treat the fresh manure entering the system. In
spite of proper operation, there is an "over turning" of the lagoon
contents that occurs in the fall of the year for a couple of weeks, as ambient
temperature drops and cools the top layer of liquid in the lagoon. As its
density increases, it drops to the bottom of the lagoon, forcing the bottom
layer, containing partially digested manure solids, to the top. This phenomenon
can result in higher odor levels for a week or two around the lagoon.
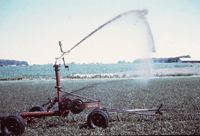 |
Irrigation of Lagoon
Effluent |
(Source: Purdue University) |
Lagoon contents are normally applied to cropland by spray irrigation systems.
If the lagoon is properly designed and operated, spray irrigation should
not release much odor, because most of the organic solids should have been
biologically stabilized. In a well-operated lagoon, effluent should have
only about 20% as much nitrogen and about 30% to 40% as much phosphorous
and potassium as raw manure, because of treatment and sedimentation of solids
to the bottom of the lagoon. These solids, or sludge, must be removed every
few years and the operation should plan to handle them as a part of their
nutrient management plan. Because this material is very concentrated, it
may be possible to haul the sludge off site or to more distant cropland
that can better utilize the nutrients contained in the sludge. Because of
the nuisance potential of this partially stabilized material, it should
normally be injected or otherwise incorporated as with liquid manure.
Back to Top
Lagoons - Egg Wash Water
Since eggs from laying hen houses contain traces of manure on the shell,
most states require that the water used to wash the eggs be collected
and processed accordingly. Many laying hen operations collect this dilute
wash-water in lagoon systems and apply the nutrients to croplands via
irrigation systems (typically spray irrigation). Some producers treat
this low-nutrient, wastewater using constructed wetlands or other systems
prior to land application.
Back to Top
Back
to Poultry Menu
|