 |
 |
Common
Manure Handling Systems
Table 1. Manure Production per 200 Cows* |
|
Per Day (lb.) |
Per Year (LB) |
Feces and Urine |
24,100 |
8,800,000 |
Total Solids |
3,360 |
1,230,000 |
Volatile Solids |
2,800 |
1,020,000 |
Total N |
126 |
46,000 |
Total P |
26 |
9,610 |
Total K |
812 |
23,600 |
*does not include wastewater and bedding
*estimates may increase with milk production |
Cows differ considerably in the amount of manure they produce. Jerseys,
for example, produce only 60% as much manure as Holsteins. With respect
to many environmental rules, especially state regulations, however, no consideration
is made for breed or body size. Composition of typical dairy manure is known
(Table 1). Consideration must be given to the kind(s) of
bedding used (Table 2) and the milking system (Table
3), both of which contribute to the amount of manure produced on
a dairy farm.
Table 2. Bedding |
|
ft3/cow/day |
Housing Type |
Chopped Straw |
Sawdust |
Tiestall |
0.8 |
0.1 |
Freestall |
0.3 |
0.2 |
Loose Housing |
1.1 |
--- |
0.6 ft3 per cow is a good guide |
|
Table 3. Wastewater |
# Milking Cows |
gal/cow/d |
ft3 |
0 - 50 |
5 - 8 |
0.6 - 1.0 |
50 - 100 |
4 - 6 |
0.5 - 0.8 |
150 + |
2 - 4 |
0.2 - 0.5 |
1 Gal = 7.5 ft3 |
|
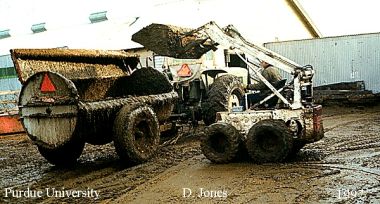 |
Skidsteer Loading a Manure Spreader |
A number of manure handling systems are utilized in dairy
production. For tiestall barns, manure is collected in gutters
behind the cows and removed from the barn as a solid material by a barn
cleaner. Outside of the barn, the barn cleaner
places the manure on a storage stack or directly into a manure
spreader.
There are three types of manure handling systems
used for freestall barns:
- Manual scraping,
- Flush systems, and
- Automatic alley scrapers.
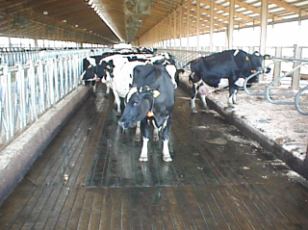 |
Flush Systems Work Very Well |
Some freestall barns use slotted concrete floors
above a pit, but these are quite rare in
the U.S. With manual scrape systems, manure is scraped to the end of the
barns by a skidsteer or mechanical loader with a scraping attachment.
The manure is either stored
temporarily in a solid stack, or loaded directly onto a manure spreader.
Some barns are equipped with a freestall alleyway that is flushed
with recycled wastewater to convey the manure to a storage pit or lagoon.
Mechanical alley
scrapers consist of a hinged v-shaped plough driven by a cable or
chain. The plough is continuously or periodically dragged forward to draw
manure to the end of an alley. When being pulled, the plough's blade splays
across the entire alley between two curbs. After completing a pass, the
chain or cable reverses direction and pulls the plough backward as the
plough's blades fold together so as not to pull manure the opposite direction.
Flush
systems are comprised of a tank that delivers copious amounts of water
to flush all manure off the alleys. Provided there is adequate slope along
the channel and adequate water pressure from the tank, flush systems work
very well. However, some concerns have been raised that a number of bacterial
pathogens may be circulated through the
barn by flush systems.
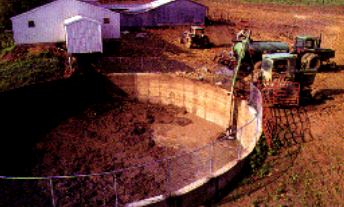
(Source: Al Sutton, Purdue University) |
Storage Containers |
Frequently manure from the freestall barn is stored
temporarily in a storage pit and combined with more dilute waste from the
milking parlor. Milking parlor waste often contains very little manure,
but does have much residual milk from cleaning and may have various cleaning
products as well. Manure from pits is agitated and then loaded onto a slurry
wagon for application onto cropland, often with direct incorporation into
the soil.
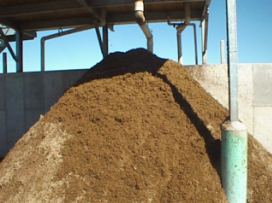 |
Effluent Drips Down for Collection |
Collection pits may also be used when solids are to be separated
from the liquid portion of the manure. Solid
separation can be mechanical, in which the liquid portion of the manure
is squeezed though a screen. This provides a relatively dry solid that may
be composted and perhaps even reused as a bedding
material after drying. Sloped screen separators
work by trickling the manure over a sloped
screen so that the effluent drips through the screen with the solids
sliding down for collection. Other mechanical
separators draw an apron across the manure to force it across a screen.
Concrete
pit separators work by using a porous "weeping wall" in which the effluent
is allowed to weep through the slots between boards or screens while the
solids are retained. The solids then can then be removed as a semi-solid
from the concrete
pits. Composting is another option for
solid manure management.
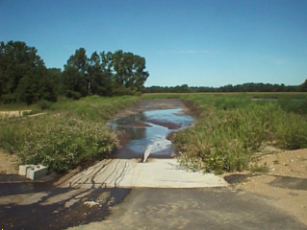 |
Settling Pond |
With sloping screen separators or other mechanical
methods, the effluent may go into a settling pond
to settle out even more solids before the effluent enters the lagoon.
Many lagoons have been constructed with clay or compactible soil. In sandy
or lighter soils, dairies must line the lagoons with compacted clay or synthetic
liners.
Recently, there has been much interest expressed in developing technology
to utilize methane produced by anaerobic digestion of manure . As cost of
the technology declines and pressure to manage manure and control odors
on larger farm units increases, this technology will become more common.
On some very large farms, these systems are used to generate electricity
and hot water for the farm. Some are able to to sell electricity back into
the grid through their local cooperatives. Cost of this technology remains
too expensive for all but the largest producers at this time. Furthermore,
anaerobic digestion should be viewed as a value-added process, but not as
a solution to nutrient management difficulties, since nitrogen, phosphorus,
and potassium remain in the effluent following digestion. Advantages appear
to be in reduced energy costs, potentially reduced odors, and a more stable
manure slurry.
Back
to Dairy Main Menu
|