by
Mr. William D.Faulkner
Calgon Carbon Corporation
Marketing Director
Pittsburgh, Pennsylvania
Mr.John E.Urbanic
Calgon Carbon Corporation
Senior Research Fellow
Pittsburgh, Pennsylvania
Mr.Robert W.Ruckel
Calgon Carbon Corporation
Manager of Metallurgical Process Market
Pittsburgh, Pennsylvania
Presented at the 110th Annual Meeting of the
Society of Mining
Engineers and the Metallurgical Society, Denver, CO. Feb. 23-27, 1987
Abstract
Guidelines are presented for the selection,
handling and regeneration of activated carbon used in gold recovery
operations. The guidelines are based on Calgon Carbon Corporation's own
investigations and experience gained in working with gold mine operators all
over the world. Gold adsorption rate and adsorption capacity are shown to be
independent variables thereby requiring testing of both properties when
selecting activated carbon. Means of measuring these these properties are
provided. Historical activity tests on activated carbon are shown to be
minimally useful in selecting carbon for gold recovery. Proper thermal
regeneration techniques to maximize recovery of adsorption rate without
weakening the carbon structure are suggested. Simple positive means of
measuring efficiency of regeneration are presented. The subject of
regeneration are presented. The subject of hardness measurement as a
predictor of "in process" abrasion is discussed. The cost/benefit
issue of carbon activity level is addressed.
INTRODUCTION
Mill designers and operators desire maximum
recovery of precious metal values at the minimum achievable cost while
maintaining steady state plant performance. Economics favor lowest possible
soluble gold losses from the adsorption section of the plant, since at this
point in the process the gold is available at no additional liberation cost.
To achieve this objective requires carbon with high adsorptive power which
is a reflection on the inherent ability of the carbon, the efficiency of
regeneration of the carbon and the residual values on the carbon when it is
returned to the circuit. Additionally, the carbon must load well in the
presence of co-absorbing materials, both organic and inorganic, to keep
stripping and recovery costs to a minimum. The physical strength of the
carbon impacts operating costs. Make-up carbon purchases to offset abrasion
and regeneration losses should be minimized. Steady state operation is
favored by using consistent quality carbon.
Activity, particle size and attrition
resistance of activated carbon are selection criteria relating to plant
performance that are addressed in this paper. Operating guidelines on the
use and regeneration of activated carbon are provided. The test methods
discussed here are those which the authors believe, and experience in
specifying carbon to a variety of mining operations all over the world has
shown, best describe the properties essential for extraction of gold from
pulp and leaching solutions. Calgon Carbon Corporation has been
manufacturing carbons for this market using these tests for specifications
and/or quality control. The information is presented primarily with the pulp
applications in mind. Where considerations relative to column use are
prominent particular mention is given. Applications other than precious
metals recovery are not addressed.
GENERAL DESCRIPTION OF ACTIVATED CARBON
Activated carbon can be manufactured from
many carbonaceous raw materials. High carbon content, low ash and low cost
are raw material requirements. Many wastes have been utilized such as
sulfite liquors, waste lignin, and wastes from processing petroleum and
lubricating oils. Materials of vegetable origin and younger fossil fuels
were some of the first materials used - wood, peat, sawdust, nut shells,
fruit pits. More recently bituminous coals have come into use. Hassler
(1974) mentions 33 raw materials which have been studied for the production
of activated carbon.
The raw material affects final product
characteristics, as does the type of manufacturing method - chemical or
steam - and the particulars of the manufacturing process. Most of the raw
materials and processes will allow the production of fine powdered carbons
although product characteristics and costs will vary. The list of realistic
raw materials and applicable manufacturing processes shrinks when large
particle/granular carbon is needed and physical strength in the virgin and
regenerated states are considerations.
For precious metals recovery, granular carbon
is the most widely used form. Over 95% of the coarse carbon in service for
gold and silver recovery is steam activated coconut base carbon.
Products available for consideration include:
Table 1
COMMERCIALLY AVAILABLE CARBONS
FORM |
MEAN
PARTICLE
SIZE (mm) |
SIZE
FRACTION
U.S.SIEVE NO. |
RAW
MATERIAL |
Granular |
2.5
2.1
1.7 |
6x12
6x16
8x16 |
Coconut,
Bituminous Coal |
Pellet |
2.6 |
2 mm diam. |
Coal, Peat |
Powder |
0.04 |
65%-325 |
Coal Peat,
Wood |
SELECTION CRITERIA FOR ACTIVATED CARBON
Criteria used to select activated carbon
include the following tests and/or considerations.
1. Adsorption Rate
2. Adsorption Capacity
3. Iodine Number and Carbon
Tetrachloride Number
4. Particle Size
5. Attrition Characteristics
6. Desorption Characteristics
Adsorption Rate
Adsorption rate is generally accepted as the
fundamentally important adsorption criteria by factors of 3:1 to 5:1 over
equilibrium adsorption capacity for gold. With process and carbon particles
size parameters held constant, higher rate of adsorption raises stage
efficiency and reduces loss of soluble gold.
The quality control test initially used by
Calgon Carbon (available from Calgon Carbon Corporation) was adapted from
earlier work by Anglo American Research Laboratories (Davidson, et al.,
1982). In this test, the rate of gold adsorption is determined by using
carbon dosage of one gram of carbon of 2.19 mm mean particle diameter, (8x10
U.S. Sieve No.) in 1.7 L (dosage of 0.6g C/L solution) of 5 ppm borate
buffered potassium aural cyanide solution.
Figure 1 - Plexiglas adsorption rate vessel
showing inside and outside dimensions and baffle arrangement
A baffled Plexiglas cylinder (Figure 1) is
used to hold the carbon and solution. The solution is stirred at 400 rpm by
a propeller type stirrer. The propeller pitch is adjusted to keep all of the
particles in suspension while minimizing particle to particle collision. The
narrow particle size range insures that the adsorption rate will not be
influenced by particle size distribution, since it is the relative
adsorption rate of the various carbons that is the desired characteristic to
be measured.
The gold concentration of the solution is
determined periodically over an eight hour exposure. The data are fitted to
an equation of a straight line illustrated in Equation I below.
t/(x/m) = (1/M)t +
l/R
(1)
where:
t = Time - Minutes
x/m = Carbon Loading (mg/g)
M = Reciprocal of the Slope
R = Reciprocal of the Intercept
at the Time Zero
The value R for each carbon tested is
relative. Higher R-values indicate faster adsorption rates under the conditions of the test.
More recently, the test has been shortened to
two hours with more frequent sampling at earlier time intervals. The dosage
has been increased from 0.6 grams carbon per liter of solution to l gram
carbon per liter of solution. The data are then treated by plotting the log
of gold concentration versus time and fitting at first order rate equation
shown below.
Log C = mt +
b
(2)
The gold concentration in ppm (C) at any
given time in minutes (t) can be computed if the slope (m) of the equation
has been determined experimentally. Value b, the intercept, is the log of
the initial concentration.
Calgon Carbon's laboratory studies have shown
that over the dosage range of 0.5 to 2g C/L solution, the slope
"m" of equation (2) varies directly with carbon dosage. This means
data obtained or quoted at other carbon dosages on equivalent mesh size
carbons and agitation conditions can be recalculated to a standard dosage
for comparison.
Changing from the R-value to the first order
rate constant m does not alter the relative rankings of carbons with respect
to adsorption rate. This is demonstrated in the table below.
Table 2
ADSORPTION RATE RANK
CARBON |
R-VALUE |
m |
MINUTES TO
50% Au REMOVAL
1g C/L DOSAGE |
A |
0.08 +/- 0.005 |
0.007 +/-
0.00035 |
45 +/- 2.65 |
B |
0.046 +/-
0.0046 |
0.0035 +/-
0.00018 |
90 +/- 4.5 |
Both methods can be used with synthetic
solutions or actual plant solutions to compare the adsorption rate of
different carbons. The test can be used with virgin, in-use, or regenerated
carbons to monitor the operation of the gold adsorption system.
Adsorption Capacity
The K-value (Calgon Carbon Test Method #53)
is a measure of equilibrium gold capacity. It is determined from an isotherm
for the activated carbon in question. The carbon is ground to less than 30
microns or 95% passing a U.S. Sieve #325. A series of dosages of carbon are
exposed to 100 ppm of potassium aural cyanide in a pH 10 borate buffered
solution. The K-value is the carbon's gold capacity in milligrams of gold
per gram of carbon at the interpolated 1 ppm gold concentration value.
Equilibrium capacity is not directly related to adsorption rate, as will be
shown later. For this reason, it is of secondary importance when evaluating
carbons for gold recovery use.
It has been suggested that it is necessary to
add excess cyanide ions to the solution intended for use in isotherm tests;
otherwise the system will not come to equilibrium. To check this premise the
standard test with and without excess cyanide present was conducted at
various contact times. The data in Table 3 below demonstrate no difference
in equilibrium gold capacity between 2 and 54 hours contact time. The effect
of excess cyanide ion does not change the time to reach equilibrium but does
suppress capacity.
Table 3
INFLUENCE CYANIDE AND TIME
ON "K" VALUE
CONTACT
TIME-HOURS |
K-VALUE
WITHOUT
EXCESS CN |
WITH CN |
2.0
7.5
54.0 |
30.8
30.8
30.3 |
24.4
24.5
24.4 |
Iodine Number and Carbon Tetrachloride Number
These are the traditional activity parameters
for coconut-based activated carbon. Iodine number (AWWA B604-74-4.7), which
measures the take-up of iodine in milligrams of iodine adsorbed per gram of
carbon when carbon is in equilibrium with .02 normal iodine solution,
represents an approximation of the surface area available to most adsorbates.
CCl4 number (ASTM D3467-76) is
expressed as a weight percent loading on the carbon when the carbon is
exposed to air saturated with CCl4 at 0oC. This is a
rough measure of micropore volume of the activated carbon. This test was
developed during World War II as a means of classifying gas mask carbons.
Carbon tetrachloride is a good gauge of vapor
phase adsorption capacity. The use of activated carbon in gold recovery
combines physical adsorption, surface reactions and solution equilibrium.
Therefore, these two standard measures of activated carbon quality are not
necessarily good gauges for the use of carbon in gold recovery applications.
An absence of correlation between adsorption
capacity for gold and surface area was shown in work by Davidson, et al.
(1982). An investigation was undertaken in the laboratories of Calgon Carbon
to explore the relationships between both the adsorption capacity and
adsorption rate of gold cyanide and the traditional activity parameters.
Activations were carried out in a laboratory rotary furnace. Time,
temperature and atmosphere were varied to produce a range of activity levels
from the same coconut raw material. In total, 26 carbons were produced. The
results of comparing the "K" and "R" values with Iodine
Number and CCl4 Number are shown in Figures 2-5. Correlation
coefficients are given for the complete sample populations. For reference,
"R" values for commercial carbons generally fall in the range of
0.03-0.12. "K" values will occur over the full range of values
shown. As can be seen, there are correlations between adsorption rate and
the traditional activity parameters; however, fixing Iodine Number and/or
CCL4 value can still result in wide variations in "R"
value.
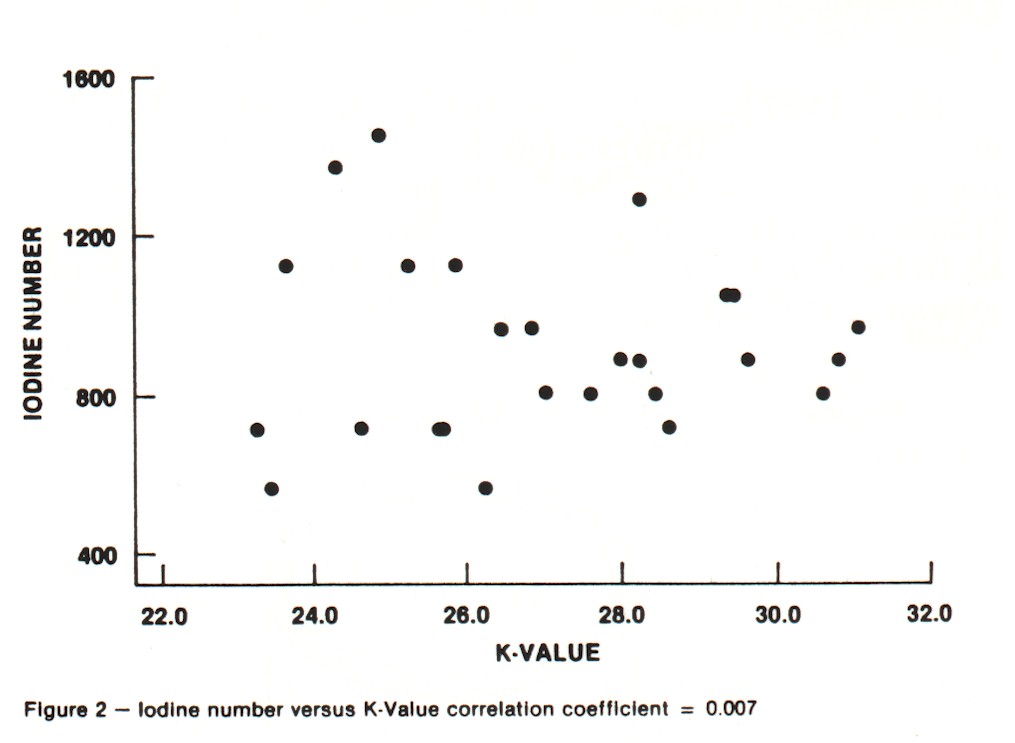
|
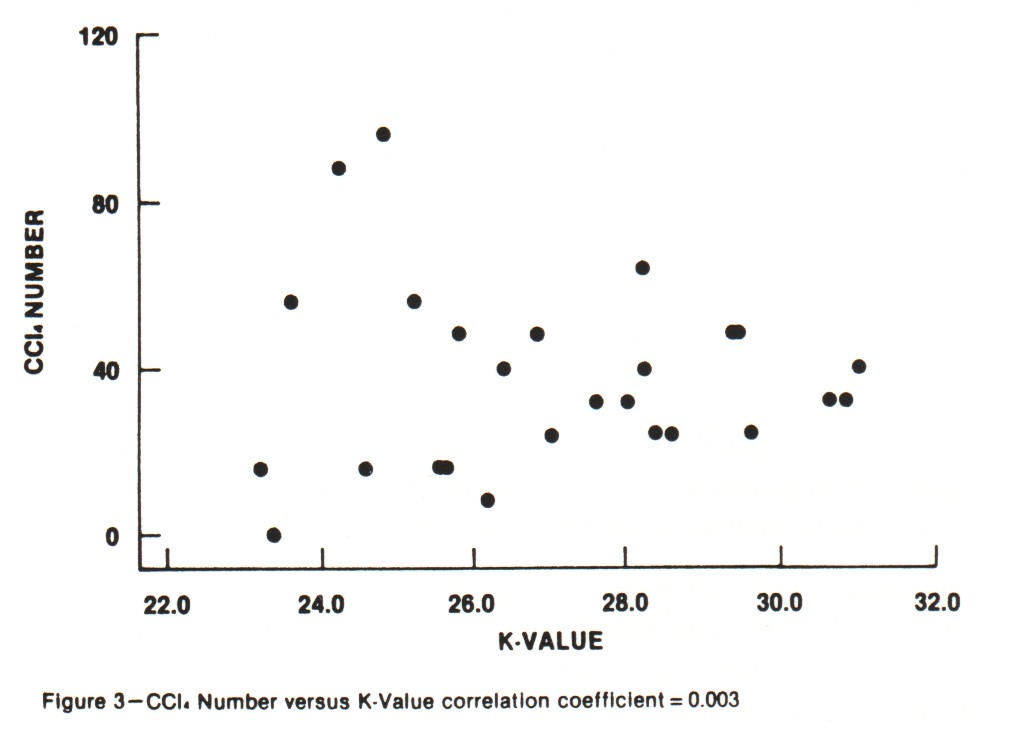
|
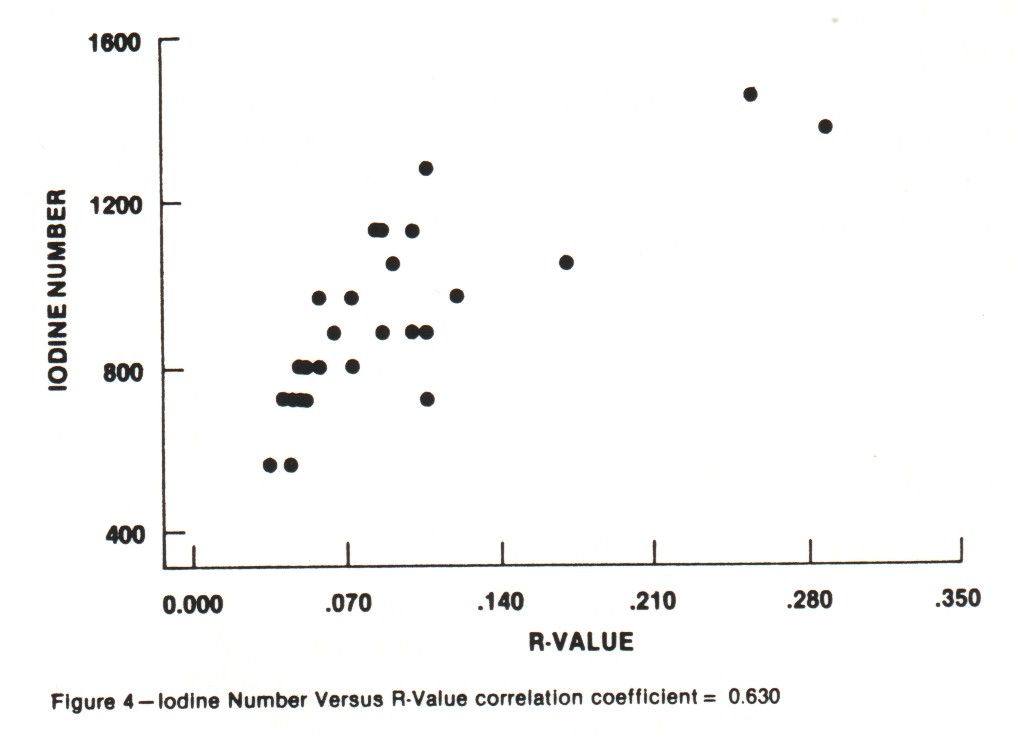
|
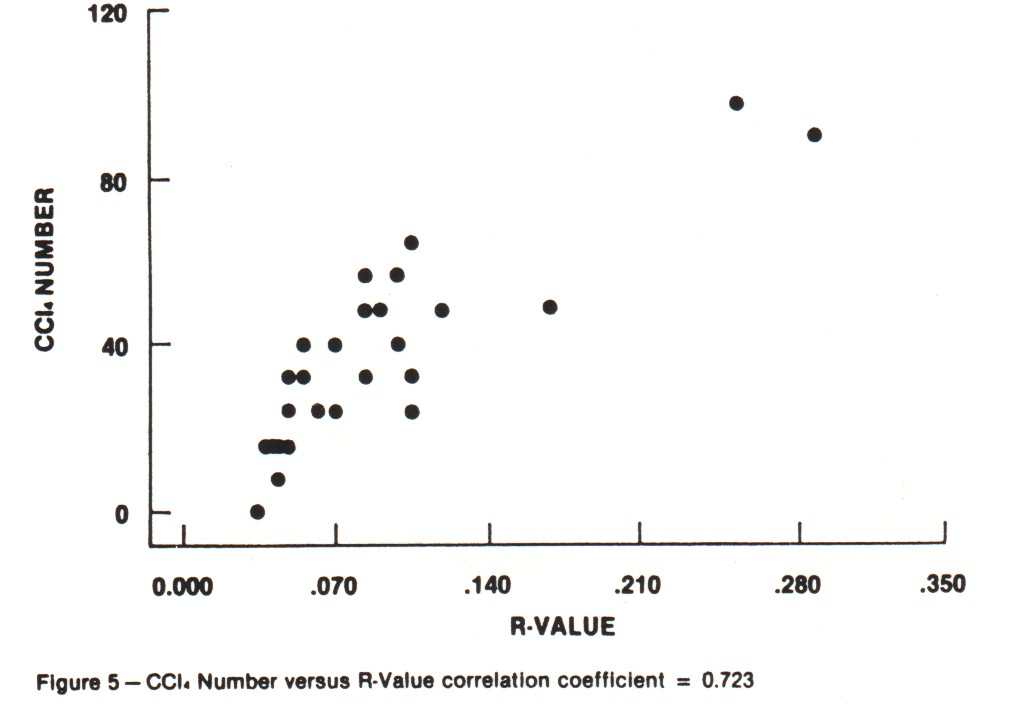
|
Additionally, the "K" and
"R" values were compared as shown in Figure 6. These data clearly
indicate that adsorption equilibrium capacity for gold (as reflected in the
"K" value determination) does not provide information on
adsorption rates.
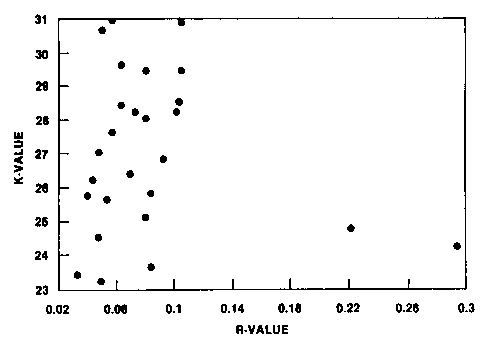
Figure 6 - K-Value versus R-Value correlation
coefficient = 0.021
One could theorize that carbons from the same
producer would be produced under standard conditions and therefore would be
consistent in gold adsorption properties. To assess this premise, virgin
carbon samples were obtained from several mines in the United States. The
results were organized by carbon suppliers and are shown in Table 4. All
carbons were supplied to the mines against Iodine number and CCl4
specifications.
Table 4
VARIATION OF CARBON CHARACTERISTICS
BY MINE AND SUPPLIER
|
SUPPLIER
X |
SUPPLIER
Y |
Mine No.
Characteristics |
1 |
2 |
3 |
4 |
1 |
5 |
Apparent Density
g/ml) |
0.600
|
0.525
|
0.586
|
0.459
|
0.599
|
0.569
|
Hardness No. |
87.8 |
82.8 |
93.0 |
82.4 |
96.4 |
98.0 |
Ash (%-wt.) |
1.67 |
3.13 |
1.36 |
2.44 |
3.81 |
4.19 |
Iodine No. (mg/g) |
897 |
808 |
859 |
1180 |
779 |
831 |
CCl4 No. |
22.3 |
28.4 |
27.5 |
59.3 |
22.5 |
20.0 |
"K"Value Kg Au/MT |
27.1 |
19.1 |
27.1 |
25.1 |
26.7 |
15.1 |
Subsequently, samples of carbon were obtained
from different packages of a single 18.12 mt (40,000 lb) incoming shipment
to a mine. Those test results are shown in Table 5. These data indicate that
significant variations can occur in gold adsorption properties from
individual sources, and that significant variations can even occur within an
individual shipment.
Table 5
VARIATION OF CHARACTERISTICS
FROM SAME LOT
|
No. 1 |
No. 2 |
No. 3 |
Apparent Density (g/ml) |
0.484 |
0.491 |
0.495 |
Hardness No. |
99.4 |
99.8 |
99.4 |
Ash (%-wt) |
3.1 |
3.3 |
3.7 |
Iodine No. (mg/g) |
1260 |
1232 |
1199 |
CCl4 No. |
66.7 |
64.6 |
59.9 |
K Value (Kg/MT) |
30.5 |
33.4 |
29.3 |
R Value |
.046 |
.070 |
.066 |
Both sets of data suggest that one should not
rely on Iodine Number and CCL4 values as purchase specifications
for carbon to be used in gold recovery operations.
Carbon Particle Size
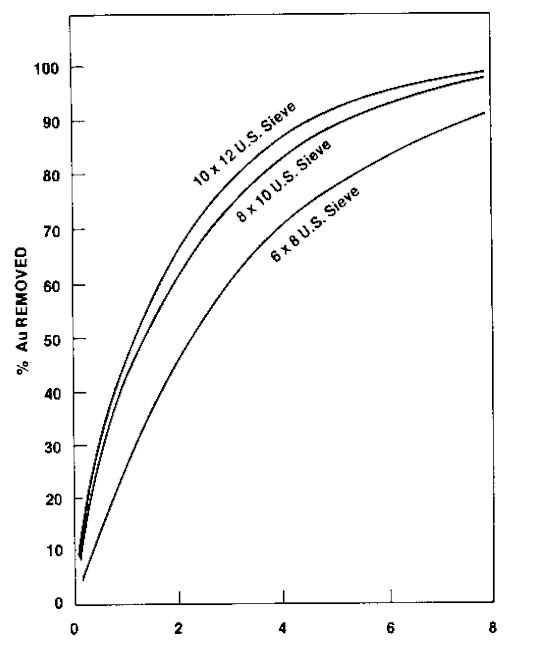
TIME-HOURS
Figure 7 - Adsorption rate
curves showing effect of particle size
Carbon particle size has a major impact on
rates of adsorption and desorption. The magnitude of the impact on
adsorption rate can be seen in Figure 7 where the removal of gold from
solution is plotted against time for three fractions of the same carbon
sample.
Table 6
GRC CARBON PARTICLE SIZE
VERSUS K-VALUE
Carbon mesh fraction |
6 x 8 |
8 x 10 |
10 x 12 |
K-Value |
28.4 |
28.7 |
28.4 |
The K-value was determined for each fraction
and was found to be similar for each fraction (Table 6). It can therefore be
concluded that the effect seen in Figure 6 is purely a particle size
phenomenon. This raises the possibility that one could use less of a finer
mesh carbon to achieve the same stage efficiency in a CIP circuit. While the
rate of adsorption improves with finer carbon, concern about carbon losses
arise.
Experience has shown that plants using the
finer carbons do not generally have higher losses. Coarser carbon is
required in most cases because of problems encountered with flow of pulp
through small screen openings necessary to retain finer carbons.
Particle size is also a significant
consideration when carbon columns are used to remove gold from leachate
solutions. When expanded beds are used in this process, the fluidization
characteristics of the different size carbons vary significantly. Solution
temperature also affects fluidization characteristics. One needs to design a
system for the maximum flow and the minimum temperature that are expected to
be encountered.
Attrition Characteristics
The ASTM Ball Pan Hardness (D3802) test has
historically been used to measure the resistance to crushing and breakage of
granular carbons. It was a method originally accepted by the Chemical
Warfare Service for respirator carbons that had to withstand the rigors of
the canister assembly process and then be transported to and used on the
field of battle. The test is reliable when comparing carbons of the same
form. It is not viewed as a reliable test relative to CIP service for
pelleted carbons. The test suffers somewhat in sensitivity for carbons that
give results in the 97 plus area and when comparing results on different
Ro-Tap machines. At the present time it is still the most widely used test
for specifying carbons. Modification of the test method is under study.
Attrition test methods remain an area of some
concern for mineral processors. Due to the plant-to-plant variations in gold
recovery operations, it is extremely difficult to verify the predictive
value of any type of laboratory attrition test on absolute plant carbon
losses or even relative losses in plant operations. With this situation
present, it appears that uneasiness with ball pan test methods developed out
of difficulty in perceiving that resistance of carbon to breakdown from
being shaken, dry, with steel balls would correlate with gentle wet
agitation in a 40-50% fine solids slurry in a CIP system. Metallurgists have
devoted efforts toward developing agitated wet tests.
Interest in ball pan tests has not been
dropped. Carbon attrition can potentially occur whenever significant carbon
movement occurs such as in transferring carbon slurries through pumps and
pipelines and in tubling carbon through regeneration kilns. Overall, ball
pan type tests may hold advantages in selecting granular carbons and in
maintaining consistent carbon quality.
Efforts will likely continue to refine and/or
standardize on a test method. Regardless of the type test method pursued,
the test should be relatively insensitive to common variances in test
operator skills, laboratory equipment and carbon sampling techniques. For
the carbon manufacturer to best respond to customer needs, the practicality
of using the test method for on-line quality control is an important
consideration.
Desorption Characteristics
Of equal importance to the loading of gold on
carbon is the ease with which the adsorbed gold and silver can be removed
from the carbon by stripping solutions. This is an area where relatively
little comparative test work has been reported. Limited laboratory work
conducted at Calgon Carbon showed lack of consistent results when working
with the same carbons. Fortunately, there is substantial field experience to
show that coconut carbons can be adequately stripped. Of particular interest
is the performance of carbons with high capacity for gold. A perception
about carbons with high capacity for gold was that they would be difficult
to strip. A number of plants strip high performance coconut carbon to 34 gm/mt
(one ounce per ton). Conclusions from field experience with coconut carbon
cannot be extended to include carbons made from all base materials. They
will not necessarily behave the same way (Van Deventer, 1984).
Cost Considerations
Conducting a rigid cost/benefit analysis on
high versus low adsorption rate carbon is clouded by the number of variables
in plant operations that impact on plant performance. Additionally, it is
rare for a plant to change carbons instantaneously whereby the working
inventory is replaced without additional changes being made. The closest
published reference is the experience at the President Brand plant reported
by Young (1984). Test work in the plant using baskets of carbon suspended in
the adsorption tanks indicated that 150-300% loading improvement could be
achieved with high activity carbon. The entire plant inventory was replaced
with high activity carbon. Carbon concentration was increased in the last
two adsorption tanks from 24 g/L (0.2 lb/gal) to between 30 and 40 g/L (0.25
and 0.33 lb/gal). Soluble losses decreased from 0.17 mg/L (0.00002 oz/gal)
to 0.01-0.04 mg/L. Gold values on loaded carbon increased from 4.28 kg/mt
(125 oz/T) to 6.16 kg/mt (180 oz/T).
President Brand, in effect, recovered an
extra 0.15 gm gold per mt of ore (0.0044 oz/T), assuming 50% slolids slurry,
by switching to high gold adsorption rate carbon.
To put carbon costs in perspective, it is
useful to consider the amount of additional gold it is necessary to recover
to offset the cost of using high activity carbon. Table 7 presents a simple
sensitivity analysis on additional gold recovery needed as a function of
carbon losses. The assumptions are: $11.25/gm (350 $/oz) gold, 50% solids
slurry, 1.10 $/kg (0.50 $/lb) cost differential between low and high gold
adsorption rate carbons.
Table 7
CARBON COSTS
IN TERMS OF RECOVERED GOLD
|
CASE 1 |
CASE 2 |
CASE 3 |
Carbon Losses
gm/mt ore
(lb/st) |
30
(0.06) |
60
(0.12) |
90
(0.18) |
Differential Carbon Cost
$/mt ore
($/st) |
0.03
(.03) |
0.07
(.06) |
0.10
(.09) |
Equivalent Gold
gm/mt ore
(oz/st x 104 ) |
.003
(.86) |
.005
(1.71) |
.008
(2.57) |
In the worst case of 90 gm/mt carbon loss
(Case 3), the recovery of an additional 0.007 gm gold per mt of ore (0.00026
oz/T) pays for the higher price carbon. The carbon losses reported at
President Brand were 35 g/mt. The value of higher activity carbon to
President Brand, by this simplified cost/benefit analysis, would be a net
1.65 $/mt improvement in gold recovery.
Using Carbon In Operating Plants
Once the carbon has been selected, interest
shifts to preparing it for use and maintaining it. Two basic considerations
to preparing carbon for use are wetting and pre-attrition. To completely wet
activated carbon with room temperature water requires considerable time, as
the data in Figure 8 show.
Figure 8 - Effect of water temperature on air
displacement rate upon wetting 12 x 40
U.S. Sieve high activity Carbon. Estimated total air volume present in 454 kg Carbon
is 0.42 m³.
The carbon should be soaked at least 24 hours
to insure that none of it floats out of up-flow columns or concentrates in
the upper region of CIP tanks. Particularly in heap leach operations where
solution temperatures vary through the seasons, the influence of solution
temperature should be kept in mind. Cooler solutions, because of higher
viscosity, retard the wetting process and cause greater expansion of up-flow
beds.
Preconditioning of granular carbons is
generally recommended to accelerate the rounding off of sharp corners. North
American plants are typically equipped with pre-attrition agitated tanks for
this purpose. Another approach to pre-attrition is to use the reactivation
unit. Fresh carbon is added to the kiln feed hopper. This approach can be
used for new plants when the kiln is not being fired, whereby the kiln acts
as a tumble drum. With a kiln operating at temperature the same approach is
still applicable. Some carbon fines may be burned in the hot zone of the
kiln. Hot carbon falling into the quench tank is instantaneously wetted. The
pre-attrition step should not result in the loss of more than 5% of on-size
virgin carbon.
Regenerating Service Carbon
Renewal of carbon (regeneration and/or acid
treatment) is required due to fouling by organics and inorganics. The rate
of adsorption appears to be must affected (Young, et al. 1984; Fleming and
Nicol, 1984). LaBrooy and Bax (1985) showed variations in poisoning effects
on various carbons from organics. The work further showed that some carbons
can adsorb more organics than others and be less fouled. Smith, et al.
(1984) found variations in the effect of inorganics on different carbons and
variations in response to acid treatment. LaBrooy and Bax (1985) showed that
frothers can have more effect than zanthate on hindering adsorption. Organic
measurements on leach solutions may be misleading relative to the amount of
organics available to the carbon in a CIP or CIL circuit. Potential exists
for organics attached to ore particles to transfer to activated carbon when
the carbon and ore are in intimate contact (Iwaski, 1969).
Conditions for regenerating service carbons
from gold plants were investigated by Urbanic, et al. (1985). Two sets of
conditions were found to be successful.
Table 8
CONDITIONS FOR REGENERATION
OF GOLD RECOVERY CARBON
|
CONDITION
1 |
CONDITION
2 |
Temperature, oC |
700 |
600 |
Time, min |
40 |
20 |
Steam, lb/lb carbon |
0.5 |
1.0 |
In Table 8 above, Condition 1 represents the
water content of plant-dewatered carbon. Condition 2 represents the
addition of 0.5 lb of steam to dewatering carbon.
Success was measured by restoration of near
virgin adsorption rate. Acid washing was found to be useful in reducing the
ash content of all service carbon tested and was beneficial in the
restoration of rate of adsorption in four of the five cases investigated.
Water quenching was found to be preferred over air cooling, but quench water
of high mineral and organic content was viewed as a potential problem.
The objective of regeneration is to return
the carbon as close to the virgin state of activity as possible. A relative
efficiency adsorption rate test is usually considered most meaningful using
the conditions of the rate test procedures described above to compare virgin
carbon with service carbon. A one point isotherm at one hour contact time
can be used to get relative results. It is recommended that a narrow mesh
fraction, such as the 2.19 mm mean particle size (8x10 U.S. Sieve) fraction
be used in the test to eliminate rate differences caused by particle size
differences between regenerated and virgin carbons. Service carbon will
usually have a smaller mean particle size.
Apparent density (ASTM D2854-83) is a simple
reproducible test that can be run in the plant and will give a clear
indication of carbon conditions. The objective is to keep the apparent
density as close to virgin apparent density as possible, after subtracting
the inorganic ash (ASTM D2866-70) from the weight of the carbon. If the
apparent density starts moving up, conditions are too mild and the
regeneration residence time and/or temperature should be increased. If the
ash-free apparent density is below virgin, then temperature and/or time
should be reduced to prevent increased carbon losses.
In the work of Urbanic, et.al. (1985), ash
content (ASTM D2866-83) and apparent density were combined to derive an
ash-free apparent density as an indicator of the amount of organic or
residual char in the pores of the carbon. For continuing operation, relative
efficiency and/or apparent density are the suggested routine tests, with
periodic determination or ash content, if apparent density increases
markedly. Particle size distribution and attrition resistance can be
determined periodically as well.
Drying of the carbon before regeneration is
counter-productive to the reactivation process. In fact, co-current addition
of steam is sometimes beneficial and has no negative impact.
Quenching of the freshly regenerated carbon
in water of low solids content is an effective means of pre-wetting the
carbon prior to re-introduction into the circuit.
SUMMARY
- Adsorption rate for gold cyanide and
adsorption capacity are independent variables. Measurement of both is
needed in determining relative practical effectiveness in gold recovery.
- Iodine and Carbon Tetrachloride
determinations are not adequate criteria to predict carbon performance
in gold recovery service.
- Given that adsorption rate is a major
determinant of relative extraction efficiency in gold recovery, accurate
comparison of virgin carbons and comparison of virgin carbon with plant
carbon requires testing of the same narrow particle size range.
- ASTM hardness number is the major
manufacturing specification test for attrition resistance. More
practical tests have not been universally accepted. Additional work is
needed to establish a standard test method that provides gold recovery
plant operators with confidence about the tests used while providing
carbon producers with a practical quality control test.
- Thorough wetting of new carbon is needed
for use in up-flow expanded beds. Pre-attrition can be achieved by making
new carbon addition to the kiln feed.
- Temperature of regeneration and time at
temperature are important positive factors in regeneration of carbon.
Drying prior to regeneration is counter-productive. Water quenching in
clean quench water of freshly regenerated carbon is preferred over air
cooling prior to re-entry into the gold recovery circuit. Determination
of apparent density and ash content of regenerated carbon will allow
good control of regeneration conditions. Ideally, the ash-free apparent
density should approach but not fall below that of virgin carbon.
BIBLIOGRAPHY
Davidson, R.J., Douglas, W.D., Tumilty, J.A.,
1982, "The Selection of Granular Activated Carbon for Use in a
Carbon-in-Pulp Operation," Carbon-in-Pulp Technology for the
Extraction of Gold, The Australian Institute of Mining and Metallurgy,
December, pp. 199-218.
Fleming, C.A., Nicol, M.J., 1984, "The
Absorption of gold Cyanide onto Activated Carbon. III. Factors Influencing
the Rate of Loading and the Equilibrium Capacity, "Journal of the South
African Institute of Mining and Metallurgy, April, pp. 85-92.
Hassler, J.W., 1974, Activated Carbon,
Chemical Publishing, New York, pp. 169.
Iwasaki, I., 1969, "Method of Removing
Fatty Acid Coating from Iron Ores," U.S. Patent 3,430,763, March 4.
LaBrooy, S.R., Bax, A.R., 1985, "Carbon
Fouling Basis of Study," Mining Monthly, Australia, August, pp.
54-63, (Presented to Chemeca, Perth, August, 1985).
Smith, I., Hinchliffe, W., Hosking, J.W.,
Muir, D.M., 1984, "Fouling Studies on CIP Carbons, Part A, Project No.
35, Report No. 5," Western Australian Mining & Petroleum
Research Institute, June, pp. 41-52.
Urbanic, J.E., Jula, R.J., Faulkner, W.D.,
1985, "Regeneration of Activated Carbon Used for Recovery of Gold,
" Minerals and Metallurgical Processing, Vol. 2, No. 4,
November, pp. 193-202.
Van Deventer, J.S.J., 1984, " Criteria
for Selection of Activated Carbon Used in Carbon-in-Pulp Plants, " Reagents
Miner. Ind. Pap., Jones, M.J., Oblatt, R., ed., Inst. Min. Metall.,
London, U.K., pp. 155-60.
Young, G.J.C., Douglas, W.D., Hampshire, M.J.,
1984, "Carbon in Pulp Process for Recovering Gold from Acid Plant
Calcines at President Brand," Mining Engineering, March, pp.
257-264.
|