Non-Electrolytic
Aluminum Oxide Conversion
Coating A
non-electrolytic method can be used to produce a thin aluminum oxide
coating of the same or better quality as an electrolytic conversion
coating while using environmentally friendly and non-toxic
materials...
John W. Wibber,
Ph.D. Sanchem, Inc.
The term
"conversion coating," as used in the finishing industry, refers to
the conversion of a metal's surface into a surface that will more
easily accept applied coatings and/or provide for a more corrosion
resistant surface. These coatings are rather thin (not more than 600
nm thick on aluminum), quickly and easily formed, easily scratched
and, if used to enhance paint adhesion, coated shortly after
application to prevent degradation of the conversion coating.
Conversion coatings for aluminum have been in use since the
early 1920s, and there are a number of different products on the
market. The four main types of conversion coatings are based upon:
the production of a film of chromium hydroxides and/or oxides; the
production of a film of precipitated heavy metal phosphates or
oxides; the use of various synthetic polymers, with or without heavy
metal phosphates or oxides; and the formation of a manganese
oxide-aluminum oxide film by use of permanganates. Manganese
oxide-aluminum oxide based conversion coatings are particularly
useful since they have excellent barrier properties and greatly
enhance the adhesion of applied coatings in general.
Electrolytically generated, or anodized aluminum, oxide
surfaces have long been used to give the highest quality and range
of aluminum oxide based conversion coatings. This quality comes at a
cost in terms of time, money and effort. This article presents a
less expensive non-electrolytic method to produce thin aluminum
oxide coatings of the same or better quality using environmentally
friendly and non-toxic materials.
Cleaning and Deoxidizing In any metal
processing procedure (painting, conversion coating, anodizing,
etc.), the most important part of the processing is the proper
cleaning of the metal surfaces prior to processing. Cleaning is the
removal of surface oils and loose dirt. In general, alkaline
cleaners do the best job. When used on aluminum they should be
non-etching, since etching will leave difficult-to-remove alloyed
elements, such as heavy metals or elemental silicon, and may pit the
metal surface. To prevent excessive etching, silicates are usually
added to alkaline cleaners. If added, they should be present in
small amounts (generally less then 500 ppm), as excessive amounts
will hinder cleaning and leave difficult-to-remove silicate
deposits.1
Deoxidation is the removal of oxides and other
inorganics that would otherwise interfere with further processing of
the aluminum without significant attack upon the aluminum surface.2
To prevent excessive attack, deoxidizers generally contain an
oxidizing agent designed to maintain a thin film of oxide on the
metal's surface. This allows for the oxide to be removed rather than
having a direct attack on the metal by the deoxidizer.
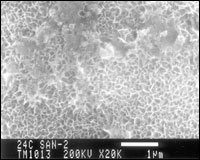 |
Fig 1-SEM of an aluminum surface after
treatment in boiling DI water at 20,000x magnification. The
hydrated aluminum hydroxide has a poorly defined,
non-crystalline structure.
|
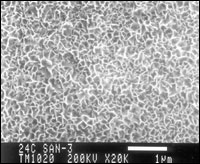 |
Fig. 2-SEM of the surface after treatment
in deoxidizing solution at 20,000x magnification. Note the
better definition of the surface.
|
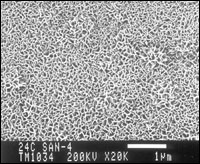 |
Fig. 3-SEM of the surface after treatment
in a proprietary potassium permanganate based solution at
20,000x magnification. Note the well-defined crystalline
structure of the manganese/aluminum oxide
surface. |
Many of the
deoxidizers now in use will use an iron (III) salt, such as ferric
sulfate coupled with hydrogen peroxide,3 or any one of a number of
different oxidizers (chlorates, nitrates, persulfates, etc.). Iron
based deoxidizers leave deposits of iron on the surface of the
aluminum that encourage galvanic corrosion, since you have two
dissimilar metals in direct contact with each other. The other
oxidizers mentioned are, in general, not strong enough oxidizing
agents to maintain a good oxide film on the metal or have toxicity
problems associated with them. The best deoxidizers for aluminum are
those based on nitric acid coupled with another oxidizer, such as
hydrogen peroxide or sodium bromate.4 Unlike other acids, nitric
acid will dissolve aluminum oxide but has very little effect upon
aluminum itself.
With high silicon content alloys, it is
difficult to avoid the use of fluorides in spite of their toxicity.
If you must use fluorides, keep the fluoride level low (generally
not more than 200 ppm) as excessive amounts of fluorides will leave
a white deposit of insoluble aluminum fluoride on the metal's
surface and will pit the metal. The use of acids other than nitric
and the use of heavy metals, such as iron, will have the same
effect.
For years chromic acid and/or chromates were used in
deoxidizers in conjunction with nitric acid and were generally
considered the best deoxidizers on the market. In addition to the
toxicity issue associated with the use of hexavalent chromium, these
deoxidizers always leave a thin deposit of chromium oxides on the
metal's surface that will not allow for the subsequent use of a
non-hexavalent chromium conversion coating system.
Non-Electrolytic Conversion Coating
Process The first stage of the process is the
formation of a hydrated aluminum oxide film by the use of boiling
deionized water. The aluminum begins to react within 10-15 sec and
completes the formation of a 30-40 nm thick, soft, blue-gray coating
in about 5 min (see Figure 1).
The second stage of the
process involves treatment of the aluminum in a proprietary aluminum
salt solution at about 200F for at least 1 min to decrease the
hydration of the aluminum oxide film and remove unwanted inorganics
(smut). At this point, the aluminum is metallic in color and has a
well-defined structure (see Figure 2).
The third step
involves treatment in a proprietary potassium permanganate solution
at 130-140F for at least 3 min to create a manganese oxide-aluminum
oxide coating of about 30-40 nm thick with a very well defined
structure (see Figure 3). The metal itself will have a clear to
light gold, iridescent finish. The coating is quite hard and scratch
resistant, will withstand temperatures up to the melting point of
the aluminum and will not degrade over time.
The already
excellent corrosion resistance and paint adhesion may be still
improved further by use of one of several secondary seals available
for that purpose. The secondary seals are non-toxic, environmentally
friendly and water-based products applied at ambient temperature and
allowed to air dry. Potassium permanganate is on the list of
materials allowed in potable drinking water5 and has been used for
more than 80 years in the treatment of potable drinking water
systems. Potassium permanganate will leave no heavy metal residues
in your rinse water.
Paint Adhesion
and Corrosion Resistance Numerous paint adhesion and
corrosion studies have been performed on bare and painted aluminum
alloys conversion coated by this process.6,7 Bare salt spray
corrosion resistance according to ASTM B-117, filiform corrosion
resistance studies and paint adhesion studies are presented in
Tables I, II and III. In all cases the coating is shown to meet or
exceed the required standards of the tests. Independent tests on
high-solids, heat-resistant paints have shown performance values
that exceed those of chromic acid anodizing in paint adhesion and
corrosion resistance characteristics.
Hexavalent chromium based conversion coating systems have
been used for more than 60 years because they have provided such
excellent corrosion resistance and paint adhesion characteristics
when used with aluminum and its alloys. Any replacement must be
designed to duplicate its characteristics as closely as possible.
The manganese oxides produced by the heptavalent manganese based
system are by far the most closely related to the chromium oxides
and hydroxides in terms of their respective chemistries. Thus, the
manganese oxide-aluminum oxide film, as produced by the heptavalent
manganese conversion coating system, is the most closely matched in
terms of performance and actual chemistry.
References 1. Spring, S., "Industrial Cleaning," Prism Press,
Melbourne, 1974, p. 20. 2. Spring, S., "Industrial
Cleaning," Prism Press, Melbourne, 1974, p. 145. 3. Anchem
Products, Inc., British Pat. # 1,368,230 (1974). 4. United
States Patent # 4,883,541. 5. "Drinking Water System
Components, Component Materials and Treatment Additives in
Accordance with ANSI/NSF 60 and 61," Underwriters
Laboratories, Inc., 1997. 6. Stephen J. Spadafora, "Naval
Air Warfare Center Aircraft Division Warminster," Warminster,
PA, Report #NADC-92077-60. 7. Jang, Elwin and Meininger,
John, "Enviromental Compliant Chemical Conversion Coating," AF
Contract: FO 4699-98-D-0004,1 AR. | |