 |
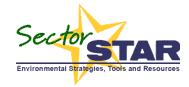
|

|
 |
|
 |
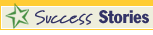 |
 |
|
Company 'Excel's at Achieving Waste
Reduction Goal SectorStar 10/23/01
Printed with
permission from BioCycle. http://www.biocycle.net/
Excel Corporation Beardstown, Illinois
The Story: On-Site Composting of Meat Processing
Residuals Helps to Reach Goals
IN 1997, Cargill,
Inc. set a corporate wide goal of a 30 percent reduction in
solid waste by 2000, using 1997 as a baseline. When the
company achieved that goal, it instituted a subsequent goal of
another 30 percent waste reduction by 2005, using 2000 as a
baseline.
Excel Corporation, a Cargill subsidiary that
processes pork, beef and related meat products at several
locations around North America, took on that challenge. At its
Beardstown, Illinois plant, getting the first 30 percent had
been relatively easy, essentially going after the low-hanging
fruit like certain recyclable materials and improved
wastewater treatment operations to reduce eventual waste
stream volumes. The second goal would be much tougher to
achieve, going beyond the "reduce and contain" initiatives of
Stage 1 (the 30 percent goal) to the more proactive efforts of
Stage 2 that involve the conversion and elimination of wastes.
Stage 2 serves the dual goals of saving containment space
(e.g. landfills) for critical materials and also creates
opportunities to actually improve environmental conditions.
About 95 percent of the waste streams at the
Beardstown plant are organic materials that are easily
composted. This includes 2,500 to 3,000 tons/year of cardboard
and processing plant waste (wastewater stream screenings,
paunch material, some livestock bedding and a small amount of
manure) that were being landfilled in a 40-mile radius of the
plant. Additionally, about 20,000 tons/year of biosolids (wet
basis) are being spread on farmland. Targeting these waste
streams would move the facility well beyond the mandate from
Cargill. After evaluating a number of alternatives, composting
was chosen as the best strategy for Stage 2 waste management.
Partners Help to Test the Concept
Adequate acreage and the availability of additional
carbon sources at the processing plant led to the decision to
compost on-site. Because of a lack of experience in the
composting arena, the first step was to find the right
partners.
The first partner selected was Midwest
BioSystems, a composting consultant, biological soils
fertility group and equipment supplier in Tampico, Illinois.
The company's founder, Edwin Blosser, originated his business
in soil fertility. He needed a high-grade biological material
and very high-grade compost was the only thing that met that
need. Blosser developed a very intense controlled composting
process to get the high-grade product desired. Excel staff
weren't nearly as interested in the final product as in the
process. People within Cargill supported the Beardstown effort
on composting, but were very concerned about the possibility
of taking one pile of waste and turning it into another pile
of waste and making a big stink in the middle. Therefore the
primary focus was on "in-process" control rather than the
product.
It soon became apparent that a very high
level of in-process control also would yield a very good
product. Excel then partnered with a neighbor of the
Beardstown plant, Illinois Forest Products (IFP). IFP is an
upscale nursery company that agreed to cooperate with Excel on
product marketing.
The final partnership was with the
Illinois Environmental Protection Agency (IEPA). Excel began
discussions and negotiations with them early on and continues
to stay in contact. The Illinois EPA provides an opportunity
to do testing before jumping into full-scale production, which
proved to be extremely helpful.
The Beardstown test
operation involved setting up a 200 cubic yard windrow built
out of all the waste streams that were potentially compost
feedstocks. The trial was initiated in May 1999. Following
construction of the windrow, an Aeromaster turner was leased
and the row was taken to full completion in about ten weeks.
There were no vector attractions or odors and the process
yielded a very good product. This provided the confidence at
both the local and corporate levels to allow movement to a
full-scale project.
Facility Design and
Operation
The permitting and siting approval
process began in the summer of 1999 with actual site
preparation beginning that fall. The facility began operating
on a full-scale basis in July 2000.
The composting
site is on 17 acres adjacent to the wastewater treatment
operations. The site includes a five-acre pad with the
capacity to handle up to 15,000 tons/year of material as well
as three abandoned anaerobic lagoon basins that create the
future ability to expand to a 12-acre pad. The site has a one
percent slope in the direction of the windrows and a base made
of over 12- inches of compacted clay that exceed the 10-5
cm/sec infiltration requirements. A compacted crushed
limestone topping of about four-inches creates an all weather
surface. Rain event runoff is managed by a collection system
that discharges into a part of the plant's wastewater
treatment system. The site also includes a loading, storage
and maintenance area. Separate storage and cleaning/sanitation
buildings are under construction.
The three abandoned
anaerobic lagoon basins each contained about three to four
feet of residual biosolids. These have been the primary
nitrogen source in the initial stages. As noted above, as
these lagoons are emptied, the pad can be expanded. A belt
press is being installed to thicken the waste activated sludge
(WAS) currently being generated so it can be included in the
composting mix. This will replace the residual anaerobic
sludge as the primary nitrogen material within the next few
months.
Cardboard is the primary carbon source in the
initial mix. About 1,000 tons/year of waste cardboard are
generated. This material is shredded in the plant into ten to
20 inch-size pieces, then loaded on a truck and brought to the
composting area where it is ground in a Haybuster 1100E tub
grinder through a three-inch screen. Because the plant
generates feedstocks that are stronger in nitrogen than
carbon, corn stalks and wheat straw also are added. Excel has
400 acres of farmland at its facility, and the stalks and
straw are baled at harvest and put through the tub grinder as
needed.
The biosolids make up about 80 percent of the
nitrogen source in the mix. Biosolids in the anaerobic lagoons
are removed from the basins via end loader and truck and
transported to bunkers in the loading/mixing area. In the near
future, the belt-thickened biosolids also will be trucked to
bunkers in the loading/mixing area. Noncardboard materials
(wastewater stream screenings, paunch material, some livestock
bedding and a small amount of manure) generated in the
processing plant are collected daily and also trucked to the
loading/mixing area and put in bunkers so that mixing can be
accomplished in a more expeditious fashion.
Feedstocks
are weighed and combined in a Knight mixer. A certain amount
of clay is added as a buffer. About 800 cubic yards/ week of
materials are processed and put in windrows built about ten to
11-feet wide, about five-feet high and 200-feet long. The
average life of a windrow is eight to ten weeks. During that
period, the windrows are turned about 20 times. Determining
when to turn is based on measured CO2 and temperatures.
Water can be added to the windrows via a tank pulled
behind the turner. This unit also is used to add inoculants
that accelerate the composting process and get the desired
microbial profile. Windrows are sometimes covered between
turnings to help in moisture management.
Marketing
the Product
After eight to ten weeks of composting
and curing, a pathogen check is run on the compost as well as
a maturity test using the Solvita kit. If the desired quality
has been achieved, the finished material is moved across the
road to Illinois Forest Products for further preparation for
market. The compost is screened to about three-eighth inch
using CEC equipment. Once Illinois Forest Products begins
bagging the material, the screen size likely will be reduced
to one-quarter inch.
Several thousand tons of compost
have been produced since the system started up. Several
hundred tons were utilized around the Excel facility as part
of a green belt appearance enhancement project. Illinois
Forest Products has used some in-house for its own nursery,
tree farm and landscaping operations. The remainder has been
marketed for landscape and nursery uses in the 150 mile radius
around the Beardstown area.
A number of marketing
seminars have been held with the participation of Excel,
Illinois Forest Products and Midwest BioSystems personnel. The
purpose of these seminars is to help customers understand the
value of compost and how to differentiate compost quality and
value for their own uses. These seminars have been well
received and feedback on their value to the customer (and
ultimate purchase of material) has been positive.
Revising Strategies to Achieve Success
Since the Beardstown composting facility began
operations about a year ago, certain challenges have arisen
along with the successes. The first challenge was related to
nitrogen impact. Biosolids would be naturally dewatered to
about 25 percent solids and then removed from the anaerobic
lagoons to the loading/mixing area. The removal process
occurred weekly and in the first stages the same general areas
of the basins would be revisited each week. However, after
several months of removal (and a greater area devoid of
sludge), several weeks could pass before a specific area was
revisited for further removal. It was learned that when
several weeks passed, some of the remaining biosolids at the
sludge removal face actually had started to compost in situ.
The net effect was an expiration of nitrogen "punch" in the
mix sooner than expected.
As a result, the nitrogen
management plan has been revised. The first step is to
minimize the surface face when stored biosolids are removed.
While some of this can be managed in the removal process, as
each basin nears completion a certain time exposure is
unavoidable. Expectations are that it will take up to two
years to complete removal of the residual materials so this
problem must continue to be managed. A more certain solution
involves the replacement of the residual material as the
primary source with the WAS and anaerobic blow-down sludge
from the belt filter press. This material is "fresh" every day
and eliminates the in situ composting problem. This change
should be reflected in the mix by late summer or early fall of
this year.
A second major challenge was related to
winter-time composting. Initial testing had spanned winter
conditions, but those conditions were not as cold as what was
experienced this past winter. In fact, several hundred tons of
product this spring did not meet final specifications in
either pathogen limits, Solvita requirements, or the general
compost marketing specifications. Some of this material was
reprocessed and some has been used on-site around the
wastewater treatment area to enhance the green belt there.
Operational changes will be implemented for future
winter conditions. This will include the reduction of any
frozen feedstocks, grinding carbon sources more finely,
reducing moisture levels and building the windrows as large as
possible. Turning also will be more restricted under winter
conditions.
Implementation of the composting operation
at the Excel facility in Beardstown, Illinois has been a
sustainable win-win situation. The plant is saving money and
is reducing its environmental liability. Disposal costs of up
to $60/ton have been reduced. Total solid waste in the fiscal
2000-2001 year at Beardstown was reduced by about 50 percent,
which already meets the Cargill goal. With increased operating
time in the coming years as well as the ability to compost
additional wastes, this reduction is certain to improve. It is
also a win for neighbors of the Beardstown facility, including
their marketing associate, Illinois Forest Products. Finally,
it's a win for the regulators in the state of Illinois as well
as the citizens of that state and region.
Lessons
Learned:
- Taking the first step is often the easiest. What
seemed to be a difficult initial goal to reach for Excel, a
30 percent reduction in solid waste between 1997 and 2000,
was actually relatively easy to achieve. The company was
able to reduce waste stream volumes by finding recyclable
materials and improving wastewater treatment operations.
- Find where you can make the biggest difference at
your facility. Excel began looking at its waste
reduction goal by looking at where it could produce the
biggest changes. This led the company to examine its waste
streams, which turned out to be 95 percent organic materials
that are easily recycled.
- Partners bring experience and encouragement. When
it began to tackle its second goal of reducing waste by 60
percent, Excel chose to compost its organic residuals. It
had no experience in composting, so it sought the help of
Midwest BioSystems, Illinois Forest Products and the
Illinois Environmental Protection Agency. These partners
helped Excel test its concept for waste reduction and refine
the composting process to achieve high levels of success.
- Understand your facility. Excel took a great
amount of time to study and understand the design and
operation of its facility. This knowledge is crucial when
trying to make improvements to processes, or finding ways to
cut wastes. It is also critical to understand your facility
should any problems arise -- you will then be able to
respond quickly.
- Turn waste into useful products. Through its
composting efforts, Excel has actually created a product
that is valuable to one of its partners, Illinois Forest
Products (IFP). The compost is used in IFP's in-house
nursery, tree farm and landscaping operations, and was used
by Excel as part of a green belt appearance enhancement
program. What wasn't used by these companies is then put out
into the larger market and used by landscapers and nurseries
in a 150 mile radius from Beardstown.
- Be flexible with your plans. Excel faced many
challenges that arose after it had begun working toward its
waste reduction goals. It remained flexible in its approach
and was able to address these problems as they arose, and
still reach its goals.
Contact
Information Excel Corporation 2901 N
Mead St. Wichita, KS. 67219
Phone: (316)
832-7500
Printed with permission from BioCycle.
http://www.biocycle.net/
|
|
 |
|
 |