A Generalized Framework and
Methodology for Product Planning in Eco-Industrial Parks
Shi Lei 1, Zheng Donghui 2,
Shen Jingzhu 2, Li Yourun 2, Qian Yi
1, (1 State Key Joint Laboratory
of Environment Simulation and Pollution Control, Tsinghua
University, Beijing, 100084, China 2 Department
of Chemical Engineering, Tsinghua University, Beijing, 100084,
China)
Abstract: A product planning framework and methodology for
Eco-industrial Parks (EIPs) was studied. Following the discussion of
guiding principles, a generalized framework was firstly proposed on
how to obtain a sustainable product system. Then, an integrated
product planning methodology was set up for a given EIP. Finally,
the methodology was applied illustratively to a real EIP
project.
Keywords: product planning, industrial ecology,
Eco-industrial Park
Introduction
As one of the ideal patterns for the development of industry,
Eco-Industrial Park (EIP) has gained more and more attention in both
developed and developing countries. Two categories of EIP projects
are identified: the redevelopment of existing industrial parks and
the design of new EIPs. By learning from the Nature, both types of
EIPs try to form an engineered or self-organized industrial
symbiosis system like Kalundborg (Denmark), the most famous park
where a few disparate large units have worked out an effective
system to optimize their materials and energy (Grann, 1997). Some
common features of EIPs have been identified, for example, industry
match in terms of inputs and outputs, high efficiency of material
flows, energy flows and information flows, and so on. However, the
conception of EIP is still evolving, and the standardized one has
not yet gained. According to the United States President’s Council
on Sustainable Development (1996), an EIP can be considered to be an
industrial system of planned materials and energy exchanges that
seeks to minimize energy and raw materials use, minimize waste, and
build sustainable economic, ecological and social relations.
Up to date, most definitions on EIP are from the perspective of
process system, which easily misleads one to think that the main
task of designing an EIP is just to optimize its process system. In
fact, EIP is an evolutionary system governed by natural, social and
economical rules instead of a static one. Therefore, updating its
product system, in a sense, is a more important task for the
planning of an EIP than optimizing its process system. Looking at
the product system rather than process system, shifts the focus of
planning from the end of the process to the center stage of product
development which is essential for the overall performance of an
EIP. For a single product or products in a kind, recently, the
concept of product planning or development has been extended such
that it includes consideration of the entire life cycle of a
product. As a result, a new research area called life cycle
engineering, concurrent engineering, or integrated product and
process development comes up and receives more and more attention
(Yan et al., 1999). More recently, several studies began to cast the
planning of sustainable product system (Ehrenfeld, 1997; Hanssen,
1999). However, they still put their stress on the life cycles of
products instead of the context of a given EIP. Much research is
needed to obtain a systematic methodology for product planning for
EIPs.
A generalized framework was proposed firstly on how to obtain a
sustainable product system under the guiding principles of
industrial ecology. Based on this framework, then, an integrated
product planning methodology was set up for a given EIP. Finally,
the methodology was applied illustratively to the planning of
Shenjia EIP located in Quzhou City, the East China’s Zhejiang
Province.
Guiding principles of product planning
The product planning process is a step-by-step procedure that
firms follow from product ideas to product introduction into the
marketplace (Spitz, 1977). It is so complicated that the systems
approach to product planning is always required. By considering the
industrial system as a whole, industrial ecology provides a
conceptual framework and a comprehensive and systems-based approach
for the process of planning product development. According to
Stanley (1999), industrial ecology is an approach based upon systems
engineering and ecological principles that integrate the production
and consumption aspects of the design, production, use and
termination (decommissioning) of products and services in a manner
that minimizes environmental impact while optimizing utilization of
resource, energy, and capital.
Following the ideas behind industrial ecology, Hanssen (1999) has
developed a systematic structure for Environmentally Sound Product
Development by integrating environmental performance, customer
quality and life cycle economy in decision-making. Four main
strategies for product system improvements were mentioned:
- Reformulating user requirements, to find new innovative
solutions beyond the scope of today’s product systems;
- Improvement in the performance of the product system, in
relation to user requirements;
- Substitution of the whole product system, or
substitution/elimination of parts of the system;
- Optimization of the processes and operation of each system
unit or in the interaction between system units.
Hardin Tibbs (1992) provided a more detailed framework with seven
elements for industrial ecology:
- Improving the metabolic pathways of industrial processes and
materials use;
- Creating loop-closing industrial ecosystems;
- Dematerializing industrial output;
- Systematizing patterns of energy use;
- Balancing industrial input and output to natural ecosystem
capacity;
- Aligning policy to conform with long-term industrial system
evolution;
- Creating new action-coordinating structures, communicative
linkages, and information.
The first four of these items can be used as the technical
skeleton of a product design system (Ehrenfeld, 1997). However, this
skeleton is still too abstract to be practical. Many researchers
have realized this point, and presented some frameworks to integrate
technology and environment under the banner of industrial ecology
(Allenby, 1994). Among these technologies, Design for Environment
(DFE) and Green Chemistry are frequently mentioned and thought to be
central to the development of the industrial ecology because both
focus on the design phase which affords the greatest flexibility in
reducing environmental impacts (Anastas and Breen, 1997).
DFE (similar to Eco-design and life cycle design) is a systematic
approach to reducing and balancing the adverse impact of
manufactured products on the environment by considering the
product’s whole life cycle—from raw materials acquisition, through
manufacture, distribution and use, to reuse, recycling and final
disposal. It involves a combination of strategies to minimize total
environmental impacts over the whole life cycle of a product (Roy,
2000).
Green Chemistry is the use of chemistry techniques and
methodologies that reduce or eliminate the use or generation of
feedstocks, products, by-products, solvents, reagents, etc., that
are hazardous to human health or the environment (Anastas and Breen,
1997). The general areas of investigation in Green Chemistry
include: selection of feedstocks, selection of reagents, choosing
synthetic transformations, selection of solvents and reaction
conditions, and selection of products and the design of safer
chemicals. In short, Green Chemistry concerns the greening of the
feedstocks, the process and the products.
Both DFE and Green Chemistry tend to evolve a sustainable system
of production and consumption that offers a decent quality of life
to the world’s population within the long-term carrying capacity of
the Earth. However, their viewpoints are different: DFE provides the
understanding of what changes need to be made in products and
processes with its methods and tools such as Life Cycle Analysis,
while Green Chemistry provides the methods and tools by which
products and processes can be made. So, to some extent, DFE and
Green Chemistry are usually thought to be complementary. Thus, a
product planning framework can be constructed by combining DFE and
Green Chemistry.
Product planning framework
Analysis of the flow of materials used in an economic system, the
way they are used and the impact of their use on the environment
could form the corner stone for product planning, and then generate
criteria on the basis of which one could plan products development
work in an EIP. Fig. 1a shows the material flow model made up of
three subsystems: processes (production system), products, and
society (consumption system). Here, the product system is
highlighted because of its roles in bridging the production and
consumption systems. The production system takes in new materials
from the natural donor, and generates both products and wastes. Some
wastes are reused by the production system itself, and the remaining
are discarded into the natural acceptor. The products enter the
consumption system, and are then discharged with three different
terminals: some are reused without any modifications; some are
recycled into the production system; and the remaining has to be
thrown into the natural acceptor.
From the Fig. 1a, the economic, environmental and social
performances of the product system depend on the feedstocks from the
Nature, the way of production, the way of consumption, the ratio of
waste reuse/recycling, and the product in itself. In Fig. 1b, we
present a possible framework within which the five influencing
factors above are discussed. A sustainable product system can be
achieved by taking the following 5 paths:
- the dematerialization of products (replacing resources by
services and techniques, such as information techniques,
nano-techniques, molecular manufacturing, and so on);
- the greening of products (alternatives of forbidden products,
bio-degradatable products, recyclable products, and other
environmental benign products);
- the greening of processes (energy integration, mass
integration, the green catalysis system, the non-solvent reaction
system, the mild reaction system, and so on);
- the greening of feedstocks (alternating or reducing toxics
use, replacing minerals by biomass); and,
- the resourcelization of wastes (waste reclamation techniques).
By applying the product life cycle ideas in DFE and considering
all aspects of product improvements in Green Chemistry, therefore,
the framework with 5 product improvement paths provides a holistic
and systematic way of product planning.
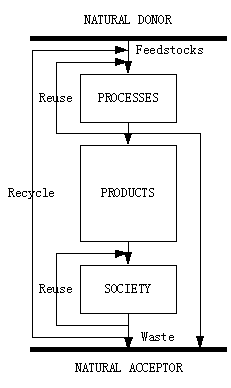 |
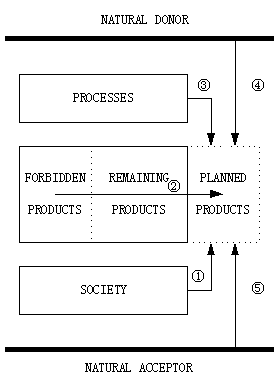 |
Fig.1a The material flow in
economic system |
Fig.1b Product planning
framework |
Product planning methodology for EIPs: an application
procedure
In the above Section, a conceptual framework for product planning
is outlined. Now we give an application procedure to illustrate how
to apply the framework systematically to real product planning in an
EIP.
Take the Shenjia EIP project being carried out as an example. An
application procedure of the product planning methodology includes
the following steps:
Step 1: construct the remaining products set by excluding
the forbidden products (mainly due to international, governmental,
and regional regulations) from the existing products set;
Step 2: construct extended products set by adding the
region-planned products to the remaining products set;
Step 3: based on the extended products set, construct the
product superstructure following the 5 paths included in the
framework above;
Step 4: decrease the products superstructure through the
convergency analysis of resources and technology;
Step 5: decrease further the products superstructure
through the marketing prediction analysis;
Step 6: decrease finally the products superstructure
through the compatibility analysis with the existing process system
in the EIP.
The main idea behind this procedure lies in: a products
superstructure is firstly constructed following the guiding
principles of product planning (Step 1- Step 3), then a dominant
product system is identified under constraints in consideration,
such as resource scarcity, technical feasibility, market prediction,
compatibility with existing system, and so on (Step 4- Step 6).
Therefore, the dominant product system provides a strong base for
guiding how to attract enterprises, as well as the site planning and
mass integration in the EIP. It needs to pay attention that we
should construct the product superstructure on a larger level (at
least on the same level) than the EIP in consideration. In this
case, the product superstructure is based on the Quzhou region level
because the Shenjia EIP is still in the cradle and its existing
product system is interlinked so strongly with other parks.
In Step 3, how to apply the 5 improvement paths to constructing
the product superstructure is the most critical. Generally speaking,
the existing steady-going product system is basically balanced with
its surrounding resources, markets, and social environment except
for some man-made disastrous interruption, which makes us to focus
on its backbone product series. In the case, 7 product series have
been identified in Quzhou region: agricultural fertilizers,
inorganic salts, nitrogenous organic compounds, halogenide products
(mainly chlorochemicals and fluorochemicals), benzene derivatives,
silicochemicals, and biomass derivatives (mainly heteronuclear
compounds and amino-acids). Taking the 5 paths, therefore, the
following product series are highlighted:
- Plastic manufacturing series (Path 1);
- Fine fluorochemicals (Path 1);
- Alternatives to chloro-agricultural pesticides (Path 2);
- Hydrogeneration product series (Path 3);
- Dimethyl carbonate derivatives (Path 4);
- Biomass derivatives distilled from plants (for example,
oranges) (Path 4).
- HCl-consumed product series (Path 5).
Apply the step 4-6 to Shenjia EIP where chlorochemicals dominate,
only HCl-consumed product series and orange-distilled product series
are preferred (the details is omitted).
Conclusions
Due to the importance of EIP to industrial development, many
industrial parks are being designed or redesigned under the guiding
of industrial ecology principles. Thus, the planning of product
system deserves more and more attention in the context of the EIP. A
generalized framework was proposed firstly on how to obtain a
sustainable product system by product design. Then, an integrated
product planning methodology was set up for a given EIP. Finally,
the methodology was applied illustratively to a real EIP project.
Further work will be followed in the near future.
References
1. Allenby, Brad. Industrial ecology gets down to earth. IEEE
Circuits and Devices Magazine. 1994, 10: 24-28
2. Anastas, P.T.; Breen, J.J. Design for the environment and
Green Chemistry: the heart and soul of industrial ecology.
Journal of Cleaner Production. 1997, 5(1-2): 97-102
3. Cote, Raymond P.; Cohen-Rosenthal, E. Designing eco-industrial
parks: A synthesis of some experiences. Journal of Cleaner
Production, 1998, 6 (3-4): 181-188
4. Ehrenfeld, J.R. Industrial ecology: a framework for product
and process design. Journal of Cleaner Production. 1997,
5(1-2): 87-95
5. Grann H. The industrial symbiosis at Kalundborg, Denmark.
The Industrial Green Game. Washington, DC: National Academy
Press. 1997:117-123.
6. Hanssen, O.J. Sustainable product systems - experiences based
on case projects in sustainable product development. Journal of
Cleaner Production. 1999, 7: 27-41
7. Hardin Tibbs. Pollution Prevention Review. 1992, 2(2):
167
8. Manahan S.E. Industrial ecology: environmental chemistry and
hazardous waste.
9. President’s Council on Sustainable Development. In:
Eco-Industrial Park Workshop Proceedings, Washington (DC), 17-18
October 1996.
10. Roy R. Sustainable product-services system. Future,
2000, 32:289-299
11. Spitz A.E. Product planning (2nd Edition). New York:
Mason/Charter Publishers, 1977
12. Yan P., Zhou M., Sebastian D. An integrated product and
process development methodology: concept formulation. Robotics
and Computer Integrated Manufacturing, 1999, 15:
201-210 |