RECYCLED PLASTIC LUMBER
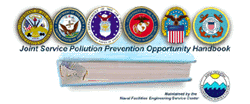 |
Revision Date: |
5/00 |
Process Code: |
Navy/Marines: MS-01-00; Air Force: MI01; Army: OTG |
Usage: |
Navy: High; Marines: High;Army: High; Air Force: High |
Compliance Impact: |
Low |
Alternative for: |
Replaces wood lumber and sheeting products. |
Applicable EPCRA Targeted Constituents: N/A |
|
|
Overview: |
As some states consider banning treated wood from landfill disposal, plastic lumber is replacing traditional wood in many applications. Treated lumber often is considered hazardous and must be disposed as a hazardous waste, making plastic lumber a desirable alternative.
Plastic lumber can be made from numerous types of plastic resins. Plastic lumber also can be made with recovered plastics, such as HDPE, PET, or several commingled, recovered plastics. The HDPE raw material comes from post-consumer waste (primarily milk jugs) and PET comes primarily from post-consumer soda bottles. The materials are either molded or continuously extruded into standard lumber forms.
Composite recycled plastic lumbers also exist, which are a combination of plastic resins and wood, such as sawdust; or plastic resins and fiberglass.
Since plastic lumber is impervious to the elements (e.g., wind, water, sun, insects, and salt air) that are destructive to wood, it may be used for many residential, commercial, or governmental applications. These applications include decks, floors, marine docks, piers, fences, playgrounds, landscape timbers, lawn and garden products, parking stops, and railroad ties. Most recycled plastic lumber is ultraviolet light (UV) stabilized to resist sunlight damage.
Plastic lumber can be installed using conventional wood working tools and will cut, drill, and rout very cleanly because there is no grain to split or chip.
Plastic lumber is commonly available in three grades - hollow, solid, and structural solid. The hollow grade plastic lumber can be used for light-load applications, such as low-load deck surfaces, fences, signage, and shutters. Regular solid-grade plastic lumber can be used for medium-to-light-load applications, such as deck surfaces and planters. The structural grade plastic lumber has a 20 percent fill of fiberglass to provide superior strength and reduce the expansion and contraction properties common to plastic wood. A fourth grade, recycled sheeting, is being tested and evaluated to be used as an alternative to plywood.
|
Compliance Benefit: |
Using recycled plastic lumber will help facilities meet the requirements under Executive Order 13101 requiring executive agencies (e.g., DOD) to incorporate waste prevention and recycling in their daily operations.
The compliance benefits listed here are only meant to be used as a general guideline and are not meant to be strictly interpreted. Actual compliance benefits will vary depending on the factors involved, e.g. the amount of workload involved.
|
Materials Compatibility: |
No materials compatibility issues were identified.
|
Safety and Health: |
Plastic lumber can be ignited and will maintain a flame very similar to a piece of soft wood. The fumes generated by burning plastic lumber are very similar to the fumes of a burning candle. Water via a fogging nozzle should be used to extinguish plastic lumber that is on fire, since a high velocity waterspray will spread the burning surface layer. Consult your local industrial health specialist, your local health and safety personnel, and the appropriate material safety data sheet (MSDS) for specific precautions and proper procedures prior to implementing this technology.
|
Benefits: |
- Uses recycled materials;
- Often can be recycled after use;
- Decreases the amount of plastic landfilled;
- Reduces replacement costs;
- Does not contain toxins (e.g., copper, chromium, and arsenic) found in treated wood;
- Does not require painting, sealing, waterproofing, staining, treatment, or maintenance;
- Does not absorb moisture;
- Does not splinter, crack, rot, or warp; and
- Allows most graffiti to be washed off easily.
|
Disadvantages: |
- Loses its strength characteristics at temperatures of 160 F and above;
- Expands and contracts more than wood;
- Should not be used as a structural component (e.g., support post, joist, stringer) unless it has been engineered for a specific applications;
- Could cause skin irritation to people who are sensitive to fiberglass if a fiberglass composite plastic lumber is used;
- More flexible than wood; and
- Heavier than dry wood of the same size.
|
Economic Analysis: |
The economic analysis compares the cost of building, maintaining, and replacing a southern yellow pine picnic bench over 20 years to the cost of building a plastic lumber picnic bench that lasts 20 years.
Assumptions:
Plastic Picnic Bench
- Total cost of high quality recycled plastic lumber picnic bench (9 pieces of 2 in. x 6 in. x 8 ft. and 5 pieces of 2 in. x 8 in. x 8 ft.) is $266.40.
- Since the manufacturer guarantees most plastic lumber for 20 years, there is no cost for treatment and maintenance. Purchase of one large collection bin: $500
Yellow Picnic Bench
- Total cost of one number 1 grade southern yellow pine picnic bench (9 pieces of 2 in. x 6 in. x 8 ft. and 5 pieces of 2 in. x 8 in. x 8 ft.) is $75.00.
- The yellow pine picnic bench will need to be replaced every 5 years (3 times in 20 years) for an additional capital cost of $225 (3 x $75.00).
- Each picnic bench will require treatment and maintenance once during its 5-year life (4 times in 20 years).
- Treatment and maintenance of the wood picnic bench includes waterproofing, sealing, staining, and painting and costs 20 percent of the capital cost.
- The treated wood picnic bench will be disposed of as hazardous waste at a cost of 10 percent of the capital cost.
Cost Comparison for Plastic Lumber vs. Southern Yellow Pine
|
Plastic Lumber
|
Southern Yellow Pine
|
Capital and Installation Costs: |
$266.40
|
$300.00
|
Operational Costs: |
|
|
Treatment and Maintenance: |
$0
|
$60.00
|
Disposal Cost: |
$0
|
$30.00
|
Total Costs (not including capital and installation costs): |
$0
|
$90.00
|
Total Recovered Income: |
$0
|
$0
|
Net Annual Cost/Benefit: |
$0
|
-$90.00
|
Economic Analysis Summary
Annual Savings for Plastic Wood: $90.00
Capital Cost for Diversion Equipment/Process: $266.40
Payback Period for Investment in Equipment/Process: 3 Years
Click Here to view an Active Spreadsheet for this Economic Analysis and Enter Your Own Values.
|
Approving Authority: |
Approval is controlled locally and should be implemented only after engineering approval has been granted. Major claimant approval is not required.
|
NSN/MSDS: |
Product |
NSN |
Unit Size |
Cost |
MSDS* |
Aeolian Hollow |
5675-01-421-XXXX |
Various |
$Various |
|
Earth Care Solid |
5675-01-422-XXXX |
Various |
$Various |
|
Trimax Structural |
5675-01-421-XXXX |
Various |
$Various |
|
Recycled Plastic Sheets |
5675-01-449-XXXX |
Various |
$Various |
|
*There are multiple MSDSs for most NSNs.
The MSDS (if shown above) is only meant to serve as an example. |
Points of Contact: |
DLA:
Mr. John Martino
Defense Industrial Supply Center
Columbus, OH
Phone: (215) 697-3894
DSN: 850-1685
|
Vendors: |
Black Rhino Recycling, Inc.
4503 Lebanon Church Road #1
West Mifflin, PA 15122
Phone: (412) 460-0160
FAX: (412) 460-0166
|
|
Aeolian Enterprises, Inc.
P.O. Box 888
Latrobe, PA 15650
Phone: (724) 539-9460
FAX: (724) 539-0572
|
|
Earth Cares Products of Long Island, Inc.
NY Phone: (800) 445-4445
FAX: (516) 427-7965
|
|
TriMax Lumber
Phone: (205) 235-8855
|
Sources: |
Mr. John Martino, Defense Industrial Supply Center, March 1999.
Save a Tree-Starve a termite- Build it once, Part Two, Loglines. Vol 2, No.4
|
[Back]