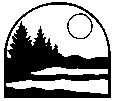 |
Office of Technical Assistance
Executive Office of Environmental Affairs
Commonwealth of Massachusetts |
Toxics Use Reduction Case Study
Quench Oil Recycling at Hyde Manufacturing Corporation
Summary
Hyde Tools, a division of Hyde Manufacturing Corp., installed a filtration system to recycle the quench
oils used in its heat treating process. This system reduced the firm's water consumption, cut back on
testing and permitting costs, and eliminated the need for out-of-house reclamation of quench oils. The
project cost $25,805 to implement, and it yielded a favorable net present value in excess of $15,000 over
its ten-year economic lifetime.
Background
Hyde Tools of Southbridge, Massachusetts is a 300-employee firm with two lines of products: an
industrial tool line featuring machine blades, saw blanks and hand knives; and a trade line of knives,
scrapers and other surface preparation tools designed for do-it-yourself home improvement projects.
Hyde's knife and scraper blades are stamped out of high-carbon steel, sent through a vibratory degreaser,
loaded into racks, then propelled via robotics through a heat treatment process. In the heat treatment
process, the blades are submerged in a molten salt tank at temperatures ranging from 1600 to 1800
degrees, then plunged into a 500-gallon tank of quench oil. The quench oil is removed from the parts in
a wash tank and two rinse tanks. The blades are then ground and polished, and the tools are assembled,
packaged and shipped.
Prior to the implementation of in-house quench oil recycling, the heat treatment process generated
approximately 12 drums of oily water every six weeks. These were sent out for reclamation and water
removal.
Toxic Use Reduction
In 1988, the firm instituted a systematic plan to attain zero discharge of water pollution within three to
five years. At that time, company management realized that eliminating the use of toxic chemicals in
Hyde's processes would not only be cost-effective, but would also help ensure the health and safety of
workers and the public, while guaranteeing that the firm would exceed compliance requirements.
With the help of plant engineers, Hyde Environmental Manager Douglas DeVries drafted a plan for
attainment of the zero discharge goal. DeVries decided to deal first with discharge from the heat
treatment process. After considerable analysis, he determined that in-process recycling was the answer.
Toxics Use Reduction Modification
After collecting and reviewing proposals from various vendors of filtration and wastewater recycling
systems, DeVries chose a filtration model capable of recycling the wash and rinse water as well as the
quench oil. The new system is composed of a transfer pump, a bag filter for capturing excess dirt, and
two heated cone-bottom reclamation tanks in which suspended solids and water can be separated from
the quench oil. This new system eliminates the need to pump oil into drums and send them out for
reclamation, reduces the total cost of reclaiming quench oils, and conserves wash and rinse waters by
filtering and recirculating them.
The purchase cost of Hyde's oil recycling system was $20,055. The vendor trained Hyde employees to
use and monitor the system at no additional cost. In-house installation costs amounted to approximately
$5,000.
Results
Reductions Achieved: Hyde was able to reduce the amount of oil sent off site for reclamation
by 1,730 gallons per year. The project also reduced water usage in the wash process by 19,200
gallons per year.
Economics: Purchase and installation costs for Hyde's new filtration and recycling system
totaled $25,055. Hyde also installed an alarm system that automatically shuts off the unit's pump
when the oil/water combination in the sump nears capacity. The purchase and installation cost of
this safety system was $750, bringing the total up-front cost to $25,805.
The new system has reduced Hyde's purchases of quench oil by $4,844 every year. In addition,
Hyde saves $8,760 in water bills, $4,200 in NPDES permits and $300 in laboratory testing costs
each year. The only new expenditures associated with the system are the filtercake purchase and
disposal costs, which total $2,800 per year. Thus, the payback period for the investment is about
2.5 years. This does not take into account the potential $2,500 per day fines or the potential
liability associated with discharging into the sewer.
OTA has conducted a more fine-toothed economic analysis which shows that the project yields a
favorable net present value of $15,229 over its 10-year economic lifetime. (See Figure 1.) In net
present value analysis, any project which shows a positive value is considered favorable.
Figure 1: Financial Analysis of Hyde Tools' Filtration and Recycling System:
Item | Year(s) | BTCF* | ATCF** | PV Factor*** | Present Value |
Purchase and Installation | 0 | ($25,055) | ($25,055) | 1 | ($25,055) |
Depreciation (straight line) | 1-10 | $2,505 | $1,002 | 6.1446 | $6,157 |
Water | 1-10 | $8,760 | $5,256 | 6.1446 | $32,296 |
NPDES Permit | 1-10 | $4,200 | $2,520 | 6.1446 | $15,484 |
Testing | 1-10 | $300 | $180 | 6.1446 | $1,106 |
Alarm System | 0 | ($750) | ($750) | 1 | ($750) |
Filtercake Purchases | 1-10s | ($1,300) | ($780) | 6.1446 | ($4,793) |
Filtercake Disposal | 1-10 | ($2,500) | ($1,500) | 6.1446 | ($9,217) |
Net Present Value | $15,229 |
*BTCF = Before Tax Cash Flow
**ATCF = After Tax Cash Flow (assuming 40% corporate tax rate)
***PV Factor = Present Value Factor (assuming 10% cost of capital)
This case study is one in a series prepared by the Office of Technical Assistance (OTA), a branch of the
Massachusetts Executive Office of Environmental Affairs. OTA's mission is to assist industry in reducing
the use of toxic chemicals and/or the generation of toxic manufacturing byproducts. Mention of any
particular equipment or proprietary technology does not represent an endorsement of these products by
the Commonwealth of Massachusetts. This information is available in alternate formats upon request.
OTA's confidential, non-regulatory services are available at no charge to Massachusetts businesses and
institutions that use toxics. For further information about this or other case studies, or about OTA's
technical assistance services, contact: Office of Technical Assistance, 251 Causeway St., Boston, Massachusetts 02114. Phone #(617) 626-1060. Fax #(617) 626-1095.
Website: http://www.state.ma.us/ota.
|