Mercury Work Group
Phase II Reports >> Hg Management Guidebook
2.0 MANAGEMENT OF MERCURY DISCHARGES
Successfully managing mercury
discharges involves the same elements used in any effective environmental management
system: commitment, goals, standards, accountability, operational controls, communication,
training, and performance metrics. Most facilities have found that many individual actions
are needed to achieve success. They have also found that these actions are most
efficiently and effectively undertaken if they are specifically developed and coordinated
under a written Mercury Management Plan.
2.1 Management Commitment
Senior management commitment and
participation are essential to successful mercury management under a Mercury Management
Plan. This commitment provides a framework for integration of the mercury management
process into facility strategic plans and for the appropriate and necessary allocation of
both human and fiscal resources.
The commitment of senior management
is often demonstrated by the creation of a Mercury Management Committee. The initial task
of this committee is to develop, publish, and internally distribute a written statement of
the management commitment and a facility policy regarding mercury control. Appendix A
gives an example of a brief mercury reduction policy statement used by a hospital as part
of a Standard Operating Procedure. A separate, stand-alone and comprehensive facility
policy statement is recommended.
2.2 Standard Operating Procedures
The Mercury Management Committee
should direct the development, communication, and implementation of policies and
procedures as necessary and appropriate to establish the facility Mercury Management Plan.
These policies and procedures should include a statement of what is expected from each
employee concerning mercury discharge control. In addition, the documents could include
specific procedures for material procurement, wastewater disposal, and mercury spill
response. Appendix A gives an example of a Standard Operating Procedure used by a
hospital to implement a mercury reduction policy.
2.3
Planning and Goals
An important part of any Mercury
Management Plan is the setting of goals and objectives and the development of a plan and
schedule to meet them. While all facilities will have an ultimate goal of achieving and
maintaining compliance with the MWRA mercury discharge limit, each facility will have its
own set of priorities and directions. As explained below, the planning process to achieve
compliance for mercury discharges should be a cross-functional effort.
2.4 Roles, Responsibilities, and Resources
To maximize its mercury
discharge reduction effort, the Mercury Management Committee should assign specific roles
and responsibilities to various individuals in developing and carrying out the overall
Mercury Management Plan. It is important to include representatives from each discipline
or department that could be involved. Organizational structures vary over a wide range;
however, for most organizations, the process should include representatives from
laboratory, manufacturing, purchasing, environmental health and safety, and maintenance
departments. It can be expected that the tasks of plan development and implementation will
require cooperation between the responsible departments. These tasks must be coordinated
with oversight and follow-up to ensure an orderly and cost-effective mercury discharge
reduction effort.
Senior management representatives
must also be active participants to ensure such coordination, oversight, and follow-up.
These representatives may need to enforce written policies to ensure that they are
continuously put into practice. Since a comprehensive effort can involve large commitments
of capital and personnel, an important part of the senior management effort will be the
allocation and scheduling of those resources to address efficiently the needs of the
organization and of regulatory agencies. For example, Standard Operating Procedures of the
facility should include descriptions of the authority and responsibilities of each level
of staff members.
The selection of, and investment in,
a proper Mercury Management Committee will help to ensure a most cost-effective and
resource-effective implementation of the steps listed below.
2.5 Controls and Procedures
Successful mercury management
has often been organized around four major components:
Many dischargers have found that
actions in each of these areas are needed as part of an ongoing Mercury Management Plan.
Control measures span the spectrum of administrative, procedural, and engineered controls.
Source reduction, source segregation, infrastructure improvements and, in some cases,
pretreatment will be needed. Frequently, more than one measure may be needed to achieve
continuously the MWRA mercury discharge enforcement limit of 1.0 µg/L (ppb). While the
sequence of actions carried out by different institutions may vary, it has proven helpful
to go through the steps listed below when developing a plan for controlling mercury
discharges:
Conduct a targeted monitoring
program to track the location of mercury sources in the facility and any changes in
mercury discharges at permitted monitoring locations that result from source reduction,
infrastructure improvements, or pretreatment.
Evaluate and test possible
substitute chemicals, operating procedures, and production processes for effectiveness,
and implement those that are feasible.
Conduct wastewater
characterization studies to obtain specific data regarding problem sources or chemicals,
monitor progress in reducing mercury concentrations, and learn of possible interferences
with candidate mercury pretreatment systems from, for example, suspended solids, other
heavy metals, or complexing agents. Reduce or segregate such interfering waste streams.
If necessary, clean or replace
waste piping infrastructure (traps, drains, and lines) in the facility to remove mercury
accumulations from past use and mercury-contaminated bacteriological growth (biomass).
Reconsider and implement
additional source reduction actions, infrastructure improvements, waste segregations, or
pretreatment processes to reduce mercury levels further as needed to remain in compliance,
using routine monitoring of operations and of wastewater discharges as guides for action.
For a flow diagram depicting much of
this process, refer to Section 3.0, "Step-by-Step Approach to Discharge
Compliance" of the MWRA/MASCO Mercury Work Group, Phase II, End-of-Pipe Subcommittee,
Pretreatment Guidance Manual, December 1997.
2.5.1 Identifying Sources of Mercury
The first step to manage mercury
discharges is to identify how mercury enters the facilities wastewater. Several approaches
to accomplish this task are summarized below:
Process characterization
Facilities should use process
flow diagrams to develop a conceptual model of the facility as a series of individual
processes or unit operations that produce a product or service. All steps in the processes
where mercury or mercury-containing materials are either added or discharged should be
emphasized in the diagrams to show where opportunities exist for source reduction and
control or prevention of mercury in the wastewater before it is discharged from the
process. Large, complex facilities with many separate operations can use a combination of
different, connecting process flow diagrams. Examples of process flow diagrams for an
overall facility and for a specific process (photodeveloping) can be seen in Figure 1A
and Figure 1B, respectively.
A second useful way of tracking
pollutant sources is to list the production steps and locations and the specific mercury
sources and quantities in each step. This approach can be used as a tracking method to
ensure that all mercury sources are considered for control and to measure progress of the
program at any given time.
Hidden Sources
Comprehensive process flow
diagrams and lists will help identify the large, obvious mercury contributors but may not
help to identify all existing sources of mercury. All paths and opportunities for the
introduction of mercury from "hidden" sources must be identified.
For hidden sources of mercury,
consider the following possible sources:
process feed materials,
pharmaceuticals, reagents, and chemicals (such as ophthalmic and contact lens products,
nasal sprays, vaccines, histological fixatives (e.g., B5 and Zenker's Solution) and
stains, hematoxylin, and chemicals (e.g., Toxi-Dip B3) used for acidic drug
analysis by thin layer chromatography)
Figure 1A
Example Process Flow Diagram
Overall Facility
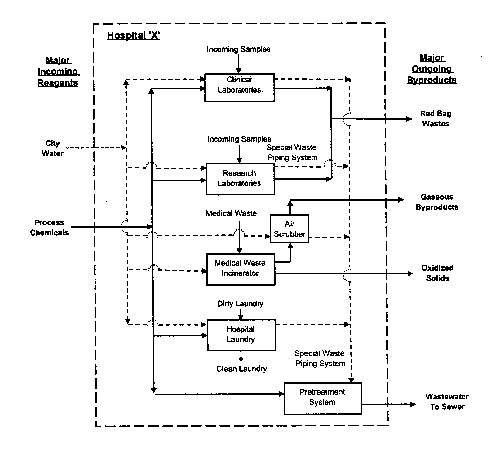
Figure 1B
Example Process Flow Diagram
Specific Process - Photodeveloping
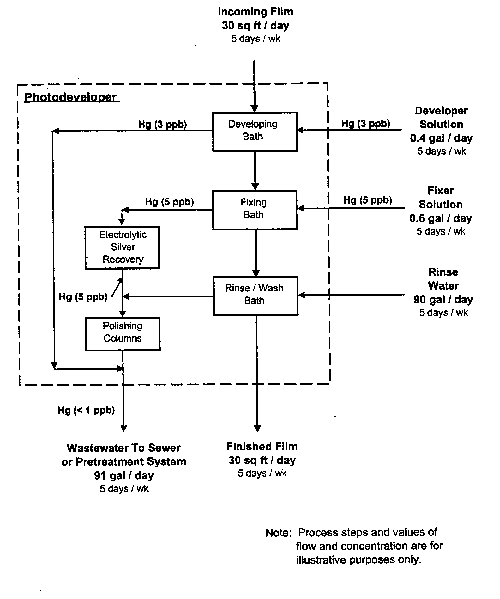
medical and biological wastes
(blood and blood products, specimen cultures, dental amalgam, and pathological wastes
including organs, tissues, and body fluids)4
tissue grinders 5
cleaning materials, soaps and
other chemicals used by janitorial services
contaminated manufacturing or
processing equipment
inputs from an incinerator
emission control process such as the fume scrubber.
facility infrastructure (the
Special Waste 6 piping system itself)7
Mercury sources may be distributed
throughout a facility. Institutional processes and activities that occur in decentralized
locations present challenges to investigations of sources of mercury-contaminated
wastewater. Hospitals and other medical institutions are good examples of this problem
because many different types of clinical and research laboratories may occupy adjacent
areas or may be spread throughout the facility. For example, a common sink used by
individuals from several different departments can be a significant source of mercury
contamination.
Mercury Source Identification:
Materials
The following actions can be
taken to identify sources of mercury contamination in commercial, industrial, and
laboratory products used at your facility:
Research available information
from chemical supply vendors including Material Safety Data Sheets (MSDS) assays and
safety information on reagent containers, and if available, certificates of analysis that
could suggest the presence of mercury in their products. Vendor information may be limited
in usefulness because mercury-bearing substances present in concentrations less than 1
percent or considered proprietary may not be reported in MSDSs or assays.
Refer to the MWRA/MASCO database
of mercury-bearing substances, chemical reagents, and other commercial products that may
be in use within a facility. Refer to Section 1.2 and Section 3.0 for
information on the database. The database was developed with information obtained from
many industries and institutions that have conducted testing of substances commonly
discharged to the MWRA sewerage system.
Request Certificates of Analysis
from all suppliers. The request should specify that Certificates of Analysis list mercury
contents in micrograms per liter (µg/L) or parts per billion (ppb), not as percentages.
For nondetectable concentrations, the Certificates of Analysis should report the
respective analytical detection limit.
Perform mercury analyses on
reagents disposed to drains in significant quantities if mercury content information is
unavailable. Initial analyses could be done on products found in and around sinks in the
facility. Continuous and intermittent discharges from automatic instruments or machines
should also be tested. Note that many domestic cleaning agents available at retail stores,
such as soaps, detergents, and bleaches, are known often to contain mercury.
Mercury Source Identification:
Facility Infrastructure:
In facilities where mercury was
or is being used, the infrastructure itself may be a significant source of discharge
pollution. The waste plumbing system should be examined for residual mercury by conducting
a sampling and testing program from the point of discharge, including any existing
pretreatment systems, all the way back to points of process discharges into system.
Consider the following:
Passive pH neutralization systems,
i.e., limestone chip tanks, can accumulate mercury-containing deposits often in
association with organic substances. Even when a chip tank is acceptable, the tank must be
inspected and serviced monthly.8 Such
tanks are not allowed for recombinant DNA biomedical research or production laboratories.9
Inspect sink traps for
accumulations of elemental mercury from past disposal practices. A sink trap cleaning and
replacement program could be conducted when suspected source areas have been isolated by
other means. Contents from sink traps, both liquid and sediment, can be analyzed for
mercury as a record of past and (after the initial cleaning) recent mercury-bearing
material disposal to the drain. The traps should be thoroughly cleaned or replaced before
reinstallation. Refer to Section 2.5.4 and Appendix B for further
information on infrastructure control measures.
Inspect waste piping systems,
particularly laterally running pipes, for accumulations of sediment or bacteriological
growth (biomass). Refer to Section 2.5.4 and Appendix B for further
information on infrastructure control measures in Special Waste piping systems.
2.5.2 Source Reduction Methods
This section addresses the
planning process from the point where the processes using mercury have been characterized
and mercury sources have been identified and quantified. Once a better understanding of
mercury sources and uses has been developed for the facility, the process of identifying
and evaluating source reduction options can be started.
The information in this section is
summarized in part from "A Practical Guide to Toxics Use Reduction"
prepared by the Massachusetts Office of Technical Assistance (OTA). OTA provides free
assistance to Massachusetts industries that wish to set up a source reduction program at
their manufacturing facilities. Additional sources for information on source reduction are
listed in Section 3.0 of this document.
Mercury source reduction can be
achieved by many methods, ranging from complete redesign of processes to simple changes in
work habits and chemical handling practices. These methods can be categorized into six
generic types of source reduction options as follows:
1. Input Substitution
2. Product Reformulation
3. Process Redesign/Modification
4. Process Modernization
5. Improved Operation and Maintenance
6. Recycling and Reuse
1. Input Substitution
This source reduction method or technique involves substituting materials or equipment
that contain mercury with non-mercury replacements. Examples of this technique include
replacement of elemental mercury with GalinstanTM,10
changing chemicals to higher grades (e.g., changing sodium hydroxide and sulfuric acid
that may be used in wastewater neutralization and treatment), and replacing thimerosal
containing reagents with non-thimerosal containing products. Additional examples of
successful input substitution can be found in Case Studies 1, 3, and 7 in Appendix
F.
2. Product Reformulation
This technique focuses on reducing or eliminating mercury in the final manufactured
products. Beyond reducing mercury discharges, this method may permit companies to increase
sales by appealing to growing consumer demand for "green" products. If your
product formulation is specified by your customers, consider negotiating with them to
change their specifications. Customers may need to be educated to realize the potential
benefits of sound environmental practices. Case Study 4 is a good example of this
source reduction technique.
3. Process Redesign/Modification
When source reduction is achieved by developing and using new and different equipment
or processes than those currently in use, it falls under the category of process redesign.
This technique focuses on alternative ways of conducting a process (e.g., manufacturing a
product, analyzing a sample) that will reduce or eliminate the use of mercury in the
process and the generation of a mercury- containing discharge. One example of this
technique is replacing mercury thermometers with digital units. Case Study 6
presents another use of this option.
4. Process Modernization
This technique is similar to process redesign, but does not involve a total redesign of
the equipment or processes being used. Instead, existing equipment/processes are modified
or replaced with newer, more efficient approaches based upon the same technology as the
old. Because fundamental changes in process technology are not made, process modernization
options will often pay for themselves more quickly than process redesign options. Examples
of this technique are more precise metering of chemicals and reagents into a process, and
new sample analyzers that use smaller quantities of reagents. Additional examples are
shown in Case Studies 1, 3, and 7.
5. Improved Operation and
Maintenance
This source reduction technique applies to all industries and should be pursued by all
facilities using mercury or mercury-containing materials. Improved operation and
maintenance often results in significant reductions in mercury discharge, and bottom-line
savings, without major up-front costs. Improved operation and maintenance has three
primary categories: Inventory Controls, Materials Handling Improvements/Housekeeping and
Personnel Training. Examples of the first two categories are discussed below. More
detailed information on personnel training programs can be found in Section 2.8 and
Appendix E of this Guidebook.
Inventory Controls
Train personnel on how to identify
and order/purchase mercury-free materials
Purchase chemicals and supplies as
they are needed to reduce storage time.
Computerize purchasing to improve
inventory control.
Install inventory management
software to track supplies.
Offer incentives to reduce rates
at which stocks of chemicals and supplies expire.
Control cleaning chemicals used by
contractors.
Housekeeping/Materials Handling
Improvements
Improving housekeeping procedures
(e.g., prohibiting water used in floor washing in non-process areas from being poured down
drains connected to the Special Waste system).
Develop a spill control plan for
mercury-containing materials, including the use of mercury cleanup kits. Make sure spills
and leaks are not discharged to the sewer.
Loading docks - repair or replace
any leaking valves, pipes, pumps, containers, and fill hose or fill line connections.
Storage areas - ensure that tank
overfill alarms are working, storage containers are properly sealed and curbed, and
workers are trained in proper chemical transfer procedures.
Laboratory stockrooms - protect
containers to eliminate breakage.
Production areas/laboratories -
repair or replace leaking tanks and equipment.
Work with employees to reduce
leaks and spills during material transfers or equipment operation (e.g., mixing batches of
reagents.)
Institute a program to have
employees separate mercury- containing materials from the waste stream (e.g., fixatives
with thimerosal, mercury thermometers, and batteries).
Production areas/laboratories -
place portable thermoplastic screens in sinks to keep medical or biological solids out of
drains.
Personnel Training
Improve employee awareness of
mercury discharge issues, sources of mercury in the facility, and proper handling and
disposal procedures. Post signs near all sinks and drains in work areas stating that
disposal of any mercury-containing compounds to the sewers is prohibited. Refer to Figure
2 for an example "Waste Water Alert!" sticker used at some facilities.
Replace the signs regularly with different background colors or revised text to maintain a
high level of awareness and compliance. Develop and periodically update specific lists of
mercury-containing compounds for each work area.
Figure 2
Example AWaste Water Alert! Sticker
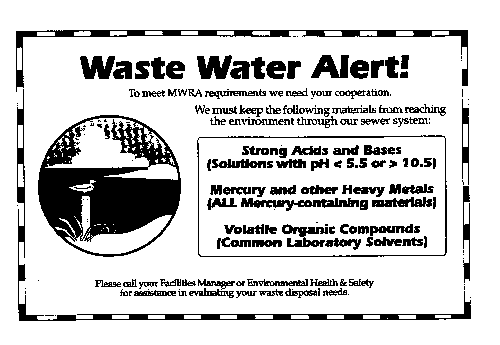
Develop standard and improved
operating and maintenance procedures. Set up personnel training and retraining programs. Case
Studies 1, 2, 3, 4, 6, and 7 provide examples of improved operating and maintenance
procedures. Refer also to the Example Standard Operating Procedure in Appendix A.
6. Recycling and Reuse
This type of source reduction technique has the potential to provide significant
reductions in chemical purchase and disposal costs, and includes recycling both treated
water and recovered mercury. An example of this technique is given in Case Study 3.
Source reduction programs usually
include the development of formal procedures for identification of source reduction
options, evaluation of the identified options, and implementation of favorably evaluated
options. The following are summaries of these three steps:
Source Reduction Options:
Identification
One commonly used technique for developing a list of source reduction options is a
series of brainstorming sessions involving several individuals at the facility. The group
should consist of facility management, engineering, maintenance, equipment operators,
manufacturing and laboratory personnel as appropriate. All options generated should be
initially listed, without judging feasibility. Developing an extensive list of options is
beneficial since it will then be more likely that the best options for the facility will
be identified. After the list is generated, the screening process can begin.
Source Reduction Options: Evaluation
The initial consideration of options need not be very detailed, but it should be
documented and structured to show why a given option is considered infeasible, worthy of
further study, or ready for implementation. Using an "option screening table" is
often helpful in structuring the evaluation. The screening table lists the options for
each part of the process, ranks them for technical and economic feasibility11 and pollution prevention potential, and shows
what action will be taken.
When identifying options, the
important thing is not to get the category of option correct, but to know what makes up
good versus bad source reduction methods. For example, if a proposed option will increase
worker exposure to safety and health hazards, it is not a viable source reduction option.
Source Reduction Options:
Implementation
As in any planning process, careful scheduling and anticipation of results are needed
for effective implementation. Once the mercury reduction options are identified and
chosen, an implementation schedule and task list should be developed and responsibilities
should be assigned.
Such a schedule is particularly
important if your facility is currently in noncompliance with the MWRA mercury discharge
limit. Compliance with MWRA limits is a task and schedule driven process. The MWRA
enforcement staff defines and negotiates specific compliance dates based on discussions
and documents from the facility and their knowledge of what is needed. If a facility does
not define the actions and schedule that it wishes to follow to achieve compliance, the
MWRA may define them for the facility. The MWRA approach may not be as convenient or as
cost-effective as a proactive plan developed by the facility itself.
Be practical in scheduling: allow a
reasonable amount of time for foreseeable and unexpected delays such as receiving results
from analytical testing laboratories, receiving price quotes, or completing construction
activities.
Source Reduction Summary
In cases where source reduction alone will not be sufficient to bring the facility
into compliance with the current MWRA enforcement action threshold of 1.0 µg/L (ppb) for
mercury, additional infrastructure, source segregation, and/or pretreatment actions may be
warranted. However, when source reduction is incorporated into a Mercury Management Plan,
the need for pretreatment will often be significantly reduced. This often results in a
lower overall cost than if pretreatment alone is pursued. Case Study 7 shows how a
clinical testing laboratory could significantly reduce the size of a pretreatment system
by including source reduction and segregation measures into its successful efforts to
achieve compliance.
2.5.3 Peak Discharge Control Methods
As part of its Phase II effort,
the MWRA/MASCO Mercury Work Group studied mercury loadings from five groups of facilities
that had MWRA discharge permits: clinical laboratories, medical waste incinerators,
hospital laundries, medical and biotech research laboratories, and other related
facilities (including college laboratories, steam suppliers, pharmaceutical manufacturers,
and testing laboratories). The study used discharge flow estimates and available mercury
concentration data to calculate estimates of average mercury loadings (in pounds per day)
for 242 of these facilities having 355 permitted discharges or sampling locations.12
One finding of the study was that
many of these facilities had sporadic peak mercury discharges during the study period.
Frequently, the peak discharges seriously affected the average mercury concentrations from
the facility. For example, a hospital laundry was found to have discharged mercury at an
average of about 400 µg/L (ppb) for six daily composite samples collected during a six
month period. Two of the six samples were measured at about 1,000 µg/L (ppb) and 1,400
µg/L (ppb), but three samples were at or below 1.0 µg/L. The 1,400 µg/L (ppb) sample
suggested that the hospital laundry discharged more than 0.1 pounds of mercury in that one
day.13 Since the overall loading to the
MWRA sewerage system is estimated to be between 0.75 and 1.0 pounds per day,14 the discharge from this one facility
represented a very significant one-day loading of mercury.
To limit such sporadic peak
discharges, facilities should develop and carry out a source reduction program as outlined
in the previous section. For many facilities, peak discharges are likely to be associated
with individual daily activities of material handling, operations, and maintenance.
Therefore, continuous training and monitoring of personnel are essential activities to
assure that proper material handling, processing, and disposal procedures are practiced at
all times.
For facilities that continue to
experience sporadic peak discharges after implementation of an intensive source reduction
program, segregation of problem waste streams from the sewer discharge should be
considered. Since the source reduction program should help to identify the problem waste
streams, control of peak discharges could become a matter of selection of alternate
disposal methods (offsite disposal) for the identified waste streams. Refer to Section
1.3 in Appendix C for a discussion of procedures and permits required for
offsite disposal of various waste streams. Refer also to the following section for the
possible contributions of biomass accumulations to sporadic peak mercury discharges.
If a pretreatment system is to be
installed, limiting the mercury concentration peaks remains an important consideration.
Problem waste streams can be segregated from the influent to the pretreatment system.
Also, a mixed equalization tank can be used to reduce variations in both the wastewater
flow and concentration. To limit concentration peaks, the equalization tank would be
operated in a partially full mode so that a volume of liquid would exist within the tank
at all times. The liquid volume would serve to dilute short-term peaks in incoming mercury
concentrations. A mixer would ensure that concentrations remain uniform throughout the
liquid volume in the tank.15 Refer to Section
2.5.5 for a discussion of pretreatment systems.
2.5.4 Infrastructure Control Measures
In some cases, the following
have been recognized as significant contributors to chronic mercury contamination in
wastewater discharges from wastewater piping systems that carry Special Waste:
1. Quantities of elemental mercury
that have collected in Special Waste piping traps that serve sinks and other fixtures.
2. Organic mercury accumulations in
the bacterial biomass growth on the interior walls of the Special Waste piping
infrastructure.
The presence of elemental mercury in
traps and other collection points of the Special Waste piping infrastructure of a facility
can result from past inappropriate disposal practices. The deposits of elemental mercury
can contaminate the wastewater passing through the Special Waste system for indefinite
periods.
Large quantities of bacterial
biomass growth within the Special Waste piping infrastructure of a facility may be very
important because mercury and mercury compounds can be converted by bacteria into very
toxic methyl mercury that becomes accumulated and highly concentrated in the biomass. This
phenomenon is called bacterial "bioaccumulation" and
"bioconcentration" of mercury. Then, dislodged pieces of the mercury-laden
biomass may be carried into the wastewater stream. In this way, large accumulations of
biomass within a Special Waste piping system can lead to instances of high mercury
concentrations in the discharged wastewater.
Therefore, infrastructure control
measures may have to be addressed in the Mercury Management Plan developed by a facility.
Specific infrastructure control measures are outlined in Appendix B and its
subsections: Special Waste Piping Design (Appendix B-1), Special Waste
Trap Cleaning/ Replacement (Appendix B-2), and Special Waste Piping Power
Washing (Appendix B-3). The guidelines and procedures outlined in these
appendices relate to mercury and biomass and their removal from Special Waste traps and
piping systems. However, these guidelines can be followed by any facility where the
discharge of mercury-containing materials to waste piping systems is suspected or has been
confirmed.
It must be noted, however, that the
biomass removal procedures have been found totally ineffective in reducing mercury
concentrations in wastewater from metal waste piping systems such as copper,16 high silicon cast iron and stainless steel.
The reason may be that mercury cannot easily be removed from most metal surfaces because
of the strong tendency of mercury to react with metals and form an amalgam (or alloy).
From the amalgam, the mercury can still be released and metabolized by bacteria in the
Special Waste piping system.
For all waste piping systems,
depending upon the approach specified in the facility's Mercury Management Plan,
infrastructure control measures may include some or all of the following steps:
source reduction
source segregation, waste piping
modifications
waste trap sampling, cleaning, or
replacement
waste piping replacement or
cleaning (power washing)
wastewater collection for offsite
disposal17
wastewater pretreatment (possibly
consisting of solids sedimentation, multistage filtration, or other process steps).
While these measures are listed in a
possible chronological order, some of them could be eliminated depending upon a facilities
specific Mercury Management Plan.
Before any infrastructure control
measures (as detailed in Appendices B and B-1, B-2, and B-3) are
started, however, a facility should take all steps needed to prevent any elemental
mercury or mercury-containing compounds from being disposed to the Special Waste drains of
the facility. Continued disposal of any amount of mercury to the drains may mean that the
waste trap and piping cleaning procedures would be totally ineffective or effective only
for a short period. Then, the waste trap and piping cleaning procedures would have to be
done again to reduce effluent mercury concentrations.
The MWRA is currently formulating
requirements for data collection during power washing. As part of this process, a facility
must notify the MWRA of its intention to do power washing and participate in a study of
power washing effects according to specific conditions and protocols. The results of the
study will be used to finalize a MWRA guidance on acceptable power washing procedures.
Currently, the MWRA is concerned that:
Power washing may be improperly
considered by some facilities as a substitute for comprehensive mercury management that
would include source reduction (including purchasing and inventory controls), source
segregation (including training and supervision of waste disposal practices), and/or
pretreatment.
Power washing may lead to greater
mercury violations for an indefinite period as small particles of loosened mercury-laden
biomass are discharged with normal wastewater flows for several days or weeks after the
power washing procedure.
Refer to Appendix B-3 for
details on the interim MWRA power washing requirements.
2.5.5 Pretreatment Systems
Facilities that experience
difficulties in complying with sewer discharge limits after implementing aggressive source
reduction, source segregation, and infrastructure control measures may find that
"end-of-pipe" pretreatment systems may be needed to achieve compliance. Since
mercury discharges to the environment have recently received considerable attention from
national (EPA), regional (Great Lakes), and local (Boston, San Diego) regulatory agencies,
several vendors of wastewater pretreatment technologies have conducted research,
development, and marketing activities related to mercury removal systems.
The MWRA/MASCO Mercury Work Group,
End-of-Pipe Subcommittee, Technology Identification Subgroup, conducted a Bench-scale
Feasibility Testing Project in 1997 for which six vendors of mercury pretreatment
technologies volunteered to participate. The participating vendors offered mercury removal
systems in the following main process technology areas:
Activated / Modified Carbons
- Barnebey & Sutcliffe Corporation and ICET,
Inc.
Other Specialized Adsorbents
- Aero-Terra-Aqua (ATA) Technologies Corporation,
ICET, Inc. (a second offering), KDF Fluid Treatment, Inc., and SolmeteX, Inc.
Electrolytic Precipitation Systems
- Soils N.V. (Zwijndrecht, Belgium).
Besides these vendors and process
technologies, the Subgroup found other vendors that offered enhanced filtration systems
for mercury removal applications. Facilities that are considering the installation of
mercury pretreatment systems are encouraged to refer to the Technology Identification
Subgroup Report18 that details the
methods and results of the Bench-Scale Feasibility Testing Project and to its companion
document, the Pretreatment Guidance Manual.19
As a follow-up to the MWRA/MASCO effort, the Massachusetts Strategic Envirotechnology
Partnership (STEP), operating under the Massachusetts Executive Office of Environmental
Affairs (EOEA), has been conducting a pilot-scale project of four mercury removal
technologies at three wastewater generating facilities. The STEP project report is
expected to be published in late 1999.
One of the most important steps in
the selection of a pretreatment system is to learn the physical and chemical
characteristics of the process wastewater stream in question. The study of wastewater
characteristics may help identify the presence of contaminants from each contributing
industrial or laboratory process. Based upon analytical testing of representative waste
stream samples, the levels of contaminants can be compared with the limits of applicable
sewer discharge regulations. The scope of the characterization effort will vary from
simple to complex depending upon the nature and size of the facility and upon the type and
extent of the discharge problem.
For wastewater containing mercury, a
wastewater characterization study could include determination of the chemical species and
physical forms of mercury that may be present. Mercury in wastewater may exist in three
chemical species: metallic, ionic, and organic. In addition, the various species of
mercury may bind to particulate matter in the wastewater to form physical agglomerates
containing mercury.
In analytical testing of wastewater
samples, total mercury concentrations are usually determined by analytical laboratories
using EPA Method 245.1 with a method detection limit of 0.2 µg/L (ppb).20 Besides meeting current regulatory
requirements, this EPA method is usually the analytical method of choice because most
applicable federal, state, and local regulations typically address total mercury
concentrations.
Of the various mercury species that
may be present in a wastewater stream, concentrations of particulate mercury are the
easiest to quantify. Particulate mercury concentrations in wastewater samples are not
directly measured, however, but are determined as mathematical differences in analytical
test results of total mercury and dissolved mercury. Dissolved mercury concentrations are
determined using EPA Method 245.1 on wastewater samples that have been initially filtered
through a 0.45 micron (mm) filter. Additional tests on samples filtered through larger and
smaller (such as 0.2 mm) filters are sometimes recommended because particulate mercury is
such an important species of mercury in wastewater.
Contaminants in the wastewater (such
as suspended solids; metals like copper, lead, and zinc; solvents and other organic
compounds; or metal-complexing agents like ammonia and detergents) can interfere with the
proper operations of certain wastewater pretreatment systems. If individual process waste
streams contain these interfering contaminants, the waste streams could be either reduced,
segregated from the other streams, or eliminated. If this is not possible, the
pretreatment system must be designed to work effectively with the identified interfering
contaminants.
A wastewater characterization study
that examines these issues can help to set an overall approach to achieving compliance
with regulations. Such an overall approach may involve a combination of source reduction,
source segregation, and pretreatment. If the facility does not have qualified technical
staff, an experienced consulting engineering firm should be employed to perform the
wastewater characterization study and to help in the development and execution of the
overall approach.
2.6 Managing Mercury Wastes
Guidance for managing mercury
wastes according to federal and Massachusetts regulations is presented in Appendix C.
This Appendix also deals with regulatory issues of collection and offsite disposal of
industrial wastewater from a facility in an area served by a sewer system (see Section
1.3.2).
The information in Appendix C
may be helpful in mercury source identification and waste reduction efforts. Wastes that
exceed the current MWRA enforcement limit for mercury may be generated when activities
such as waste stream segregation and infrastructure control measures are carried out.
2.7
Communication
Communication is key to the
pursuit of a cost-effective reduction effort. Because many tasks will cross departmental
lines, regular planning and review meetings are necessary to ensure the proper exchange of
information and progression of effort. Intra-departmental communication must also take
place as direction and training for the generators and managers of the waste streams.
Finally, an organization must maintain good communication with the regulatory agency
including a compliance schedule and routine progress reports. This reporting relationship
can also become a pathway for exchange of information as new products or reduction methods
are identified.
To keep personnel up-to-date on all
waste management issues, the facility may want to develop newsletters and informational
posters, distribute published articles, or implement other appropriate means of
communication.
2.8 Training and Education
Once a facility has identified
its sources of mercury and has determined what methods it will use to control those
sources, it is imperative that all staff be trained in the new waste management techniques
the facility has adopted. Each staff person should be made aware that the actions of each
individual throughout the workday can directly affect the compliance status of the
facility wastewater discharge.
The mercury management committee
should play an integral role in developing the training program. While the training
program should be tailored to each facility's needs, each program should include an
overview of the following topics:
regulatory requirements and
responsible agencies
sewer discharge
regulations/prohibitions
air emission regulations
solid and hazardous waste
regulations
plumbing infrastructure
information
treatment systems information
mercury source list
policies and procedures for
purchasing mercury-containing and mercury-free materials
product substitution/source
reduction
proper handling techniques
wastewater sampling protocols
pH monitoring
distinguishing and segregating
sanitary waste from Special Waste
waste management
recycling opportunities
waste minimization techniques
waste disposal protocols and
required permits
The training program should be
presented to all affected facility personnel as soon as all new waste management
techniques are in place. Newly hired personnel should be trained within thirty days of
hire. All staff should be provided with refresher training annually, at a minimum. Refer
to Appendix E for an example of a mercury awareness "Training Packet."
2.9 Periodic Reviews
To monitor the effectiveness of
a Mercury Management Plan and maintain a continuous improvement effort, regular periodic
reviews are needed. These reviews would have a dual intent:
ensure control of mercury
discharges and compliance with regulatory standards, and
ensure continuing adherence to
internal mercury management policies and procedures.
The periodic reviews should target
the key areas of the Mercury Management Plan and should be scheduled accordingly for
review and repetition. Annual reviews could be done for facilities that have successfully
set up their Mercury Management Plan. More frequent reviews should be done during the
first year, when changes are made to the system, or when deficiencies are found.
Priorities should be based on the facility's assessment of its particular risks and
vulnerabilities.
The periodic reviews should include
assessments of source reduction and waste management practices, employee training and
communication, and wastewater monitoring and pretreatment programs. Additional factors
that may affect topics, complexity, and frequency of the reviews could include regulatory
changes, new processes or operations, and personnel changes.
Review observations should identify
deficiencies and omissions in the Mercury Management Plan and should also identify and
emphasize its strengths. The reviews could include unannounced site visits to observe work
practices. Reviewers may recommend actions that address ways to ensure or improve staff
compliance with written mercury management procedures.
Plan review findings and
recommendations should be documented and shown to senior and operations managers for their
examination and action. Copies should also be distributed to operations, environmental,
engineering, maintenance, and other staff as appropriate. Additionally, managers of the
reviewed operations should develop and execute any needed corrective action plans that set
timetables and assign responsibilities for implementation. Periodic follow-up is
recommended to ensure completion of any remedial actions.
For a regulatory agency, an ongoing
Plan review program at a facility may show the facility's awareness and intent to address
mercury compliance issues. Thus, review results could be made available to the MWRA or
other regulators as appropriate. It is recommended that a facility discuss their Plan
review process with the regulating authority so that a mutual and written understanding
can be reached regarding the release and use of review reports.
2.10 Continuous Improvement
Because the results of periodic
reviews of a Mercury Management Plan can greatly help a facility to identify Plan
accomplishments and deficiencies, periodic reviews serve as mechanisms for providing
feedback into the Plan. With the support of management, the Plan can then be modified and
improved to meet the goal of total success. Therefore, a successful Mercury Management
Plan is usually one that includes a regular iterative process of investigation, action,
measurement, review, and revision.
The Mercury Management Subcommittee
of the MWRA/MASCO Mercury Work Group hopes that this Guidebook can help many facilities to
properly address, successfully and efficiently achieve, and continuously improve the
management of mercury.
RETURN TO HG MANAGEMENT GUIDEBOOK
TABLE OF CONTENTS
|