Mercury Work Group
Phase II Reports >> Hg Management Guidebook
APPENDIX B
INFRASTRUCTURE CONTROL MEASURES
As outlined in Section 2.5
of this Guidebook, infrastructure control measures may include the following steps:
source reduction
source segregation, waste piping modifications
waste trap sampling, cleaning, or replacement
waste piping replacement or cleaning (power
washing)
wastewater collection for offsite disposal
wastewater pretreatment (possibly consisting of
equalization, solids sedimentation, multistage filtration or other process
steps)
While these steps are listed in a
possible chronological order, the actual number and order of steps could be different
depending upon the facility and its Mercury Management Plan. Occasionally, earlier steps
may be repeated before a later step is undertaken.
Infrastructure control measures
have been developed and undertaken at several facilities in the MWRA sewer service area
because elemental mercury waste deposits and mercury accumulations in biomass growth from
past discharge practices were identified as significant contributors to chronic mercury
contamination of the wastewater discharges. The accumulation of mercury within waste
piping systems containing biomass growth contributes to the complexity of wastewater
mercury management at a facility. In addition, because various biological nutrients may be
contained in "Special Waste" (defined below), biomass growth can be promoted in
facilities that discharge such waste into the building waste piping infrastructure.
The three appendices that follow
are focused on mercury and biomass removal from piping systems that carry Special Waste.
However, the procedures discussed in these appendices can be followed by any facility
where discharge of mercury-containing materials to waste piping systems has been confirmed
or is suspected. The appendices are entitled Special Waste Piping Design (Appendix
B-1), Special Waste Trap Cleaning/Replacement (Appendix B-2), and Special
Waste Piping Power Washing (Appendix B-3).
Before any of the guidelines and
procedures presented in these three appendices are considered, however, a facility should
take all steps needed to prevent any elemental mercury or mercury-containing
compounds from being disposed to the Special Waste drains of the facility. Continued
disposal of any amount of mercury to the drains may mean that the waste trap and piping
cleaning procedures would be totally ineffective or effective only for a short period.
Then, the waste trap and piping cleaning procedures might have to be done again to reduce
effluent mercury concentrations.
In addition, because of a lack of
consistent analytical data developed before and after power washing of waste piping
systems at several facilities, the MWRA is currently developing a policy concerning power
washing of Special Waste systems. Specifically, the MWRA is concerned that:
- Power washing may be improperly considered by some
facilities as a substitute for comprehensive mercury management that would include source
reduction (including purchasing and inventory controls), source segregation (including
training and supervision of waste disposal practices), and/or pretreatment.
- Power washing may lead to greater mercury
violations for an indefinite period as small particles of loosened mercury-contaminated
biomass are discharged with normal wastewater flows for several days or weeks after the
power washing procedure.
Refer to Appendix B-3 for
details on the current state of MWRA power washing requirements.
To introduce and clarify the
following three appendices, Massachusetts Special Waste is defined below and the concepts
of biomass growth and mercury bioaccumulation and bioconcentration are discussed.
Special Waste
According to the Massachusetts State Plumbing Code,1
"Special Waste" includes, but is not limited to, chemicals, nuclear,
radioactive, acids, alkalis, perchloric solvents, organisms containing recombinant DNA
molecules, and other similar non-domestic wastes from various laboratories and industrial
activities. These types of wastes are potentially detrimental to a public sewerage system
and often do not comply with discharge limitations established by a local Publicly Owned
Treatment Works (POTW) such as the MWRA.
All Special Waste must be
conveyed within facilities in a separate, dedicated waste and vent piping system. The Code
covers piping design, types of waste neutralization systems, testing requirements, and
inspection requirements for Special Waste piping systems. Allowed materials and
installation methods are also specified. The Code does not specify the manner by which
Special Waste piping systems are to be used after installation or what specific chemicals
may be disposed into the system on a daily basis. On the other hand, the Code does
prohibit the introduction of solvent-bearing waste2
and requires the facility owner to submit a notarized letter stating what chemicals will
be discharged into the Special Waste system.3
The letter will be part of the basis of the design of the system by a Registered
Professional Engineer. In addition, the Code states that wastewater treatment systems
shall be part of the Engineers design when needed for compliance with regulatory
limits.4
All proposed Special Waste piping
and pretreatment system installations, modifications, revisions and additions must be
detailed in engineering drawings and specifications and certified by the Engineer. The
drawings and specifications must be submitted to the local Plumbing Inspector for review
and approval before construction. The approved documents are then submitted to the
responsible jurisdictional authority (e.g., the MWRA or the MA-DEP) with the proper
permitting documents and supporting engineering design data for final approval before the
Special Wastes can be discharged to the sewerage system.5
Biomass Formation
and Mercury Bioaccumulation and Bioconcentration
Bacterial biomass growth in Special Waste piping systems can be promoted by the presence
of organic matter such as blood products, urea, soaps, chemical reagents, and infectious
wastes discharged into the piping system. The combination of organic matter, possibly
elevated temperatures, and high humidity provides a good environment for biomass growth on
the interior surfaces of the waste piping. The organic matter often contains methyl and
dimethyl groups that can be combined by certain bacteria with inorganic mercury in the
wastewater to create very toxic organic forms of mercury (e.g., methyl mercury and
dimethyl mercury). In addition, the mercury accumulates in the bacterial biomass and
concentrates to significant levels. Because of the phenomenon of
"bioconcentration," bacterial biomass mercury concentrations 1,000 times greater
than that found in the wastewater have been reported.
Within a flowing pipe, the
biomass growth occurs principally below the liquid level with lesser amounts above. Within
a trap at a sink or elsewhere, the growth can be more pronounced because the contained
liquid creates a continuous "incubator" with effectively no oxidation or
dehydration of the bacteria. A hardened skeleton of carbon, oxidized soap products
containing elements such as calcium and potassium, and dried blood products can be formed
that strongly adheres to the piping surface.
Figures B-1 and B-2
illustrate the mercury bioaccumulation and
bioconcentration process in Special Waste traps and piping, respectively. A numeric key
for the figures appears in Figure B-3 along with a general description of the
bioaccumulation/bioconcentration process.
When wastewater flows through the
Special Waste piping system, "slugs" of mercury-laden biomass may be carried
into the wastewater stream when pieces of the accumulated growth are dislodged from the
piping wall. Therefore, large amounts of bacterial biomass growth within the waste piping
can lead to instances of high mercury concentrations in discharged wastewater. To move
toward compliance with mercury discharge limits, therefore, this phenomenon may have to be
addressed in facilities that have mercury-laden biomass growth. The following guidelines
and procedures may help some facilities address the issue properly.
It should be noted that bacterial
biomass formation can also occur within wastewater neutralization tanks. This formation
can increase the potential for further mercury bioaccumulation/bioconcentration and
wastewater contamination. According to the Plumbing Code,6
limestone chips are often used in sumps or tanks (i.e., chip tanks) for
neutralization of Special Wastes containing dilute acids and alkalis. Chip tanks should
not be used in facilities discharging significant quantities of organic matter, however,
since bacterial biomass growth will tend to coat the limestone chips, rendering them
useless for neutralization. It is recommended, therefore, that facilities check the
condition and efficacy of any chip tanks and replace them with active (adjustable)
neutralization systems as appropriate. For additional information, refer to Section 2.5
of this Guidebook.
See Figure B-3 for Numeric Key
Courtesy of Flow-Tech Associates, Inc.
Figure B -
1
Special Waste Trap Cross-Section
Mercury Bioaccumulation/Bioconcentration in Biomass
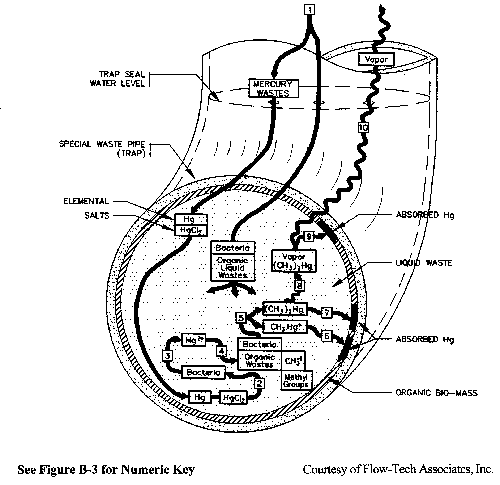
See Figure B-3 for Numeric Key
Courtesy of Flow-Tech Associates, Inc.
Figure B -
2
Special Waste Piping Cross-Section
Mercury Bioaccumulation/Bioconcentration in Biomass

Figure B - 3
Numeric Key for Figures B-1 and B-2
Mercury Bioaccumulation/Bioconcentration in Biomass
NUMERIC KEY FOR
FIGURES B-1 AND B-2
Liquid wastes enter the Special
Waste piping system carrying organic liquid wastes, bacteria, and mercury wastes such as
elemental mercury (Hg) and mercury salts (represented by HgCl2).
Elemental mercury and mercury
salts are slowly metabolized by certain bacteria. Chlorides are oxidized to chlorates and
mercuric ions (Hg+2) are released.
Elemental mercury is partly
converted to mercuric ions (Hg++2).
Mercuric ions (Hg+2)
combine with methyl ions (CH3-1) with bacteria acting as biological
catalytic agents.
Toxic methyl mercury ions (CH3Hg+)
and dimethyl mercury ( (CH 3) 2Hg ) are formed.
Methyl mercury ions (CH3Hg+)
are absorbed and bioaccumulated/ bioconcentrated in the organic biomass growing on the
Special Waste pipe wall.
Dimethyl mercury ( (CH3)2Hg
) molecules are absorbed and bioaccumulated/ bioconcentrated in the organic biomass
growing on the Special Waste pipe wall.
Some molecules of dimethyl
mercury ( (CH3)2Hg ) take a vapor form.
Some molecules of dimethyl
mercury ( (CH3)2Hg ) vapor are absorbed and bio-accumulated in the
organic biomass growing on the Special Waste pipe wall.
Some molecules of dimethyl
mercury ( (CH3)2Hg ) evaporate and are potentially released into the
workplace atmosphere from liquid surfaces in traps of the Special Waste piping system.
Courtesy of Flow-Tech
Associates, Inc.
APPENDIX
B - 1
SPECIAL WASTE PIPING DESIGN MODIFICATIONS
Introduction
This Appendix presents example design considerations for waste piping infrastructure
modifications that may be needed before initiation of any cleaning or replacement
activities in response to known mercury contamination. For background purposes, the
discussion begins with applicable state regulations.
According to the
Massachusetts State Plumbing Code,1
"Special Waste" includes, but is not limited to, chemicals, nuclear,
radioactive, acids, alkalis, perchloric solvents, organisms containing recombinant DNA
molecules, and other similar non-domestic wastes from various laboratories and industrial
activities. These types of wastes are potentially detrimental to a public sewerage system
and often do not comply with discharge limitations established by a local Publicly Owned
Treatment Works (POTW) such as the MWRA.
All Special Waste must be
conveyed within facilities in a separate, dedicated waste and vent piping system. The Code
covers piping design, types of waste neutralization systems, testing requirements, and
inspection requirements for Special Waste piping systems. Allowed materials and
installation methods are also specified. The Code does not specify the manner by which
Special Waste piping systems are to be used after installation or what specific chemicals
may be disposed into the system on a daily basis.
On the other hand, the Code does
prohibit the introduction of solvent-bearing waste2
and requires the facility owner to submit a notarized letter stating what chemicals will
be discharged into the Special Waste system.3
The letter will be part of the basis of the design of the system by a Registered
Professional Engineer. In addition, the Code states that wastewater treatment systems
shall be part of the Engineer's design when needed for compliance with regulatory limits.4
All proposed Special Waste piping
and pretreatment system installations, modifications, revisions and additions must be
detailed in engineering drawings and specifications and certified by the Engineer. The
drawings and specifications must be submitted to the local Plumbing Inspector for review
and approval before construction. The approved documents are then submitted to the
responsible jurisdictional authority (e.g., the MWRA or the MA-DEP) with the proper
permitting documents and supporting engineering design data for final approval before the
Special Wastes can be discharged to the sewer system.5
Facility
Infrastructure Inspection
The first step in dealing with known mercury contamination in the waste piping
infrastructure of a facility is to conduct an audit of the existing piping systems.
Drawings that reflect details of the actual waste piping, vent piping, and any associated
pretreatment system installations should be prepared. Special Waste diagrams are important
tools and can show regulating authorities that the facility has knowledge and control of
all Special Waste discharges. These diagrams should display all piping materials and
sizes, traps, isolation valves, glass inspection ports or sections, and sampling/drain
valves. The diagrams should also show any current areas lacking control or isolation of
Special Waste discharges.
Piping System Design and
Modification
After the piping system audit, the facility may determine that modifications are necessary
to allow for isolation of waste streams, cleaning, sampling, testing, and monitoring.
System designs or modifications should consider the following:
the type of wastes being
discharged and the piping material compatibility.6
Metal piping systems deserve special attention because of the potential for mercury to
form an amalgam with the metal. Cleaning of metal piping systems is not expected to reduce
effluent mercury concentrations. The cleaning effort may actually cause an increase in
effluent mercury concentrations. Thus, redesign and replacement of the systems using
nonmetal materials should be strongly considered instead of attempts at cleaning.
- the future uses of laboratory spaces (i.e., a
chemical research laboratory that is to be changed to a blood testing laboratory).
- the need to isolate branch piping from waste and
vent stacks to allow pipe cleaning (if needed and selected) without constricting waste
flows from other areas or causing overflows to uncontaminated piping systems.
- the investigation of unidentified Special Waste
sources and associated piping for bacterial biomass and mercury content before combining
with previously identified Special Waste piping. Pending the results of investigation of
these new sources, additional isolation valving and/or new dedicated risers discharging to
the neutralization system may need to be installed.
For trap cleaning/replacement and
power washing procedures as discussed in Appendices B-2 and B-3, respectively, any
disinfecting or cleaning agents proposed for use must be reviewed in relation to possible
interactions with the chemicals that may be contained in the waste piping system. The
potential for incompatible reactions should be considered to ensure that trap cleaning and
power washing procedures will not create any unsafe conditions. Reactions that may cause
fuming and gas evolution into the working environment, and into the piping system, must be
avoided.
Isolation Valves
The facility may determine that isolation valves need to be installed to allow for trap
cleaning/ replacement, removal of noncompliant wastes, sampling of suspect branch piping,
and control of potential cross-contamination. The location of isolation valves should
consider accessibility and maintenance especially when co-fitted with a sampling port for
testing.
The location of valves should
not cause an overflow of noncompliant wastes into another area where a spill may occur. As
an example, a floor drain would overflow if too much liquid used for pipe cleaning was
poured into a counter top sink at a higher elevation. Additionally, the need to provide
isolation valves in the venting system must not be overlooked for the same reasons.
Sampling Ports
Sampling ports should be installed in strategic locations for the periodic collection of
wastewater samples for monitoring purposes. Design of the sampling ports can follow that
shown in Figure 2, Recommended Sampling Port for Special Wastes, of the Pretreatment
Guidance Manual.7
A sampling port in an
isolated branch of piping may not only act as a monitoring point but also as a drain leg
for any disinfecting or cleaning agents used. The sampling port nozzle may be replaced
with a full-size drain leg for transfer of suspected noncompliant cleaning wastes to
containers for off-site disposal.
Special Waste Risers
Vertical Special Waste and vent piping risers may need to be isolated to allow for
sequential disinfection, cleaning, and testing of portions of entire systems in the same
manner as has been explained for horizontal runs of piping. During these periods, special
consideration must be given to the isolation of vent piping to reduce the possibility of
overflow of reagents back through the piping system.
Glass Inspection Ports
Inspection ports or sections of clear borosilicate glass piping should be installed within
the main horizontal runs of the Special Waste piping system fabricated of thermoplastic or
other opaque piping materials so that flow conditions can be viewed and the bacterial
biomass accumulation can be periodically observed. If any branch piping may contain
undiluted caustic or hydrofluoric acid, however, the branch piping sections should be
routed separately and connected downstream of a glass fitting and should have its
individual isolation valves and sampling port assemblies.
Discussion
The above are examples of the various design considerations needed for modifications of
Special Waste piping systems before cleaning or replacement activities are initiated.
However, before modifying any portion of its waste piping infrastructure, a facility
should determine if the system contains any metal piping or fitting materials8 that would require replacement and not
cleaning.
In addition, a thorough
inspection of any traps and horizontal piping runs (including analyses of biomass samples)
should be done to find if modification, cleaning, or replacement efforts should be done at
all. If trap and biomass contaminations are found, the decision would then be made to
pursue a specific combination of source reduction, source segregation, infrastructure
modification, infrastructure replacement, infrastructure cleaning, and pretreatment as a
solution to noncompliance with mercury sewer discharge limitations.
APPENDIX
B - 2
SPECIAL WASTE TRAP CLEANING/REPLACEMENT
In Special Waste systems, trap
accumulations of elemental mercury and of bacterial biomass growth contaminated with
mercury has been found a significant source of chronic elevated mercury concentrations in
wastewater discharges. The trap cleaning and replacement procedures outlined below have
been found of significant value in reducing the levels of mercury in affected wastewater
discharges.
Trap Location / Identification
Trap locations are determined by preparing a detailed inventory of all Special Waste
sources. Trap identification can be accomplished as part of the facility piping system
audit discussed in Appendix B-1. After all sources are identified, a facility Special
Waste piping general arrangement drawing should be generated with all traps identified by
unique numbers. A master inventory of all traps should be generated to record and track
all trap cleaning or replacement events. Each trap should be tagged or labeled with its
unique number, the cleaning or replacement date, and the name and signature of the person
doing the cleaning/replacement.
A Special Waste Trap
Inventory Form such as shown in Figure B2-1 can be used to document the information and
can include additional information such as the type and size of piping material.
Removal of Elemental Mercury
Elemental mercury is sometimes discharged into sinks and floor drains when
mercury-containing equipment breaks. Some elemental mercury sources include mercury
thermometers, thermostats, electric switches, and blood pressure manometers. When a sink
or floor drain trap is removed for the first time, it may contain elemental mercury,
identifiable as a pool of heavy silvery liquid separated from the trap wastewater.
Elemental mercury removed
from any traps should be collected and disposed as a mercury waste. See Appendix C for
disposal of mercury wastes.
Figure
B2-1
Example Special Waste Trap Inventory Form
SPECIAL WASTE TRAP INVENTORY
FORM
Institution Name:
______________________ Department: ______________________
Address: ______________________
Department Manager: ______________________
______________________
______________________ Date:
______________________
Building Name:
______________________
Trap ID No |
Dept./Room |
Waste Piping
Material |
Trap Type |
Type of
Waste and Hazard |
Cleaning/Replacement
Date |
Initials |
|
|
|
|
|
9 C
9 R |
|
|
|
|
|
|
9 C
9 R |
|
|
|
|
|
|
9 C
9 R |
|
|
|
|
|
|
9 C
9 R |
|
|
|
|
|
|
9 C
9 R |
|
|
|
|
|
|
9 C
9 R |
|
|
|
|
|
|
9 C
9 R |
|
|
|
|
|
|
9 C
9 R |
|
|
|
|
|
|
9 C
9 R |
|
|
|
|
|
|
9 C
9 R |
|
|
|
|
|
|
9 C
9 R |
|
Removal of
Biomass
Almost every trap will accumulate bacterial biomass, identified as a slimy brown film on
the internal surface of the plumbing material. The bulk of this growth will occur on the
bottom and wetted sections but some biomass will grow along the sides and top of the
non-wetted section of the plumbing materials. This capillary action of growth is the most
difficult to remove. Biomass growth on non-wetted surfaces can dry out. The dried out
biomass develops a strong bond to the plumbing surfaces. In addition, any elemental
mercury disposed into the drain can form an amalgam with metal plumbing. The amalgam is
very difficult to remove from the trap. Accordingly, some facilities have chosen to
replace contaminated traps rather than attempt to clean them.
Trap Removal and Handling
Precautions
Where wastewater is elevated in temperature or where chemical reactions produce heat
within a piping system, greater amounts of toxic fumes including dimethyl mercury may be
formed in the accumulated biomass. Both elemental mercury and dimethyl mercury may exist
in vapor form within the piping systems. Since negative pressures can sometimes exist in
laboratory rooms, hazardous elemental or dimethyl mercury vapors can emanate from plumbing
traps back into the rooms. Therefore, proper personnel protection should be practiced at
all times. In addition, the traps should be of the deep seal type and should continually
be filled to afford protection against possible vapor "drawback."
Trap Cleaning or Replacement
Procedures
1. Identify traps for
cleaning or replacement and discuss the trap removal procedure with the affected facility
occupants. Explain to them that the procedure will interrupt their operations and estimate
the duration of the interruption.
2. Before any traps are removed,
it is important to ask the occupants about the nature of their wastes, identifying all
possible health and safety hazards. Before handling traps that are in areas that contain
hazardous materials, all traps should be checked by the appropriate administrator for
approval (i.e., if a radioactive isotope is being used in a room, have the Radiation
Safety Department check out the trap to assure that it is safe for removal and handling).
3. After facility occupants have
been made aware of the trap cleaning/replacement program and after it is determined that
it is safe to handle traps, actual trap removal, replacement, and cleaning can be started.
4. It is important that personal
protective equipment be worn at all times by any personnel doing trap handling. It is
recommended that all these procedures be reviewed by an internal Health and Safety
Officer.
5. It is recommended that all
materials found inside the traps be initially handled as mercury waste and then disposed
of as mercury waste unless analyzed and found otherwise. See Appendix C for information on
the proper disposal of mercury waste.
6. If the removed trap is to be
cleaned, either a rag or flexible brush can be used. A cleaning agent and some type of
disinfectant may also be used to help ensure that complete removal of bacterial biomass
and disinfection is accomplished. For metal traps, replacement is usually preferred
because of the potential for mercury to form an amalgam with the metal.
7. After traps are removed,
cleaned or replaced, and reinstalled, a tag or label should be wired to the trap (or an
existing tag should be updated) with the unique number of the trap, the date, and the
responsible individuals' initials.
8. After trap removal, cleaning,
or replacement is completed and the area is returned to its original condition, all access
panels and other structural materials should be reinstalled. Before leaving the area,
inform the occupants that the procedure has been completed.
9. All trap cleanings or
replacements should be logged on a Trap Inventory Form (See Figure B2-1 for an example
inventory form).
10. If it is known that any
mercury-containing materials will remain in use, the associated wastes should be
segregated and collected for offsite disposal. Otherwise, it will be necessary to inspect
the affected cleaned traps for recurring contamination of the biomass growth. These
inspections could serve as a check on actual disposal practices and could initially be
done quarterly. Once a sufficient level of experience has been obtained, inspection
frequencies can either be increased or decreased depending on the levels of contamination
and the rates of returning biomass. The inspections should help determine the need for
repetition of the entire procedure.
11. It is highly recommended that
spare traps and associated hardware be available for each type and size of trap because
corroded or otherwise unusable traps are often discovered during a cleaning/replacement
program.
APPENDIX
B - 3
SPECIAL WASTE PIPING POWER WASHING
Background
In the past, Special Waste piping systems were sometimes used for the disposal of mercury
and mercury-containing materials. Because of the phenomena of bioaccumulation and
bioconcentration, the bacterial biomass within such Special Waste piping systems could
contain concentrations of mercury in the part per million range. In some cases, the
presence of such mercury-laden biomass was cited as the sole reason that mercury was
detected in discharged wastewater at concentrations exceeding the MWRA enforcement limit
of 1.0 µg/L (ppb).
A few facilities have used
power washing of their Special Waste piping systems as a mercury control technique because
of the scouring effect of power washing on accumulated mercury-laden biomass that
effectively removes the biomass. Some of these users believe that, after all needed
mercury source reduction has been carried out, power washing would be a lower cost final
step in effluent mercury control than removal and replacement of the contaminated Special
Waste piping system.
Special Waste piping power
washing uses specialized pumping equipment to produce a high pressure/low volume stream of
water. The water stream flows through a high pressure hose and a power nozzle to produce a
360o high velocity spray that can remove accumulated biomass and grease from
the inside surfaces of the waste piping while flushing the resulting debris down the line.
Status of MWRA Power Washing
Requirements
Currently, there are uncertainties in the ability of power washing to remove all biomass
residues thereby possibly exposing new surfaces from which mercury can reach the
wastewater. Also, there is some evidence that power washing may lead to new and possibly
higher mercury violations from the discharge of dislodged biomass particles for an
indefinite period after power washing is performed.
Because of these concerns,
the MWRA is currently formulating requirements for data collection during power washing.
As part of this process, a facility must notify the MWRA of its intention to perform power
washing and participate in a study of power washing effects according to specific
conditions and protocols. The results of the study will be used to finalize a MWRA
guidance on acceptable power washing procedures.
Waste Piping Power Washing
Precautions
The following are some precautions, recommended techniques, and possible compliance issues
that should be considered before beginning to use any waste piping power washing
procedures:
- Complete waste piping accessibility is essential
for successful power washing. Considerable modifications to an existing system (i.e.,
additions of piping isolation valves, cleanouts, access ports, and drains) may be needed
to achieve the needed accessibility. Refer to Appendix B-1, Special Waste Piping Design.
- Perhaps because of the potential for mercury to
form an amalgam with other metals, power washing has not been effective in Special Waste
piping systems constructed of metals (e.g., high silicon cast iron or stainless steel). If
a metallic waste piping system is mercury-contaminated, total replacement of the system
should be seriously considered with approved non-metallic materials.1 The MWRA will not approve a request to power
wash a metal-containing Special Waste piping system.
- All associated traps should be cleaned or replaced
before power washing. All substances contained within the waste piping system should be
assumed hazardous until analyses prove otherwise. Before waste piping power washing,
therefore, a facility Health and Safety Officer should review the proposed power washing
procedure and locations to ensure that proper personal protective equipment will be used.
- Waste piping fittings and components, especially
those of glass, can become cracked or broken during power washing. Inspect the entire
system before power washing and identify and tag any potential obstructions and fittings,
so that replacement fittings can be pre-ordered and be immediately available for
installation if the original fittings were to be broken.
- If the waste piping contains large amounts of
biomass, pieces may dislodge during power washing and may collect and clog downstream
waste piping sections. If such clogging occurs, wastewater backups in the waste piping
system may occur causing flooding at lower elevation locations.
- Dislodged biomass particles from waste piping
power washing can appear in the sewer discharge for some period after power washing. To
avoid compliance problems from the power washing procedure itself, the MWRA should be
contacted for approval prior to power washing. Refer to Section 2.5.4 of this Guidebook
and Appendix B.
- Any proposed disinfecting or cleaning agents
should be reviewed to prevent possible chemical interactions with waste constituents that
may exist in the piping system. The potential for incompatible reactions should be
considered to ensure that trap and pipe cleaning procedures will not create unsafe
conditions. Reactions that may cause fuming and result in gas evolution into the working
environment and into the piping system, must be avoided.
Waste Piping Power Washing
Techniques
The following techniques are easily monitored for effectiveness when performed on glass
waste piping systems. The techniques may require some modification when applied to
thermoplastic or other opaque waste piping materials.
- Waste piping power washing activities usually
require a minimum of two people: one serving as the power wash operator; and the other as
an observer of the nozzle and hose as it moves through the waste piping.
- The operator begins feeding the 80 to 100 feet of
hose with the power washing nozzle attached, while the observer, with a two-way radio in
full communication with the operator, watches the hose and nozzle for potential
obstructions and other problems. Typical obstructions include: tees, reducers, p-traps,
drum traps and valves.
- Some facilities have determined that successful
waste piping power washing occurs when cleaning operations begin at the collection or
treatment tanks in the lower floors. The operator then works in the waste piping system
toward the sources in a reverse flow direction. This technique is preferred because the
nozzle is designed with a reverse flow head configuration that literally "pulls"
the hose away from the power washer operator and toward the sources while flushing biomass
and debris down the line and to the collection point. In addition, most plumbing fittings
have smooth swings in the reverse direction and this seems to reduce obstruction
interference.
- Although reverse flow is preferred, the
complexities of the waste piping infrastructure may require some experimentation. For
immediate progress, select straight sections observed to contain biomass. In other
locations, piping may have to be removed or modified to reach all areas of concern. Power
washing on thermoplastic piping will require more experimentation and it may be necessary
to remove piping sections to verify cleaning effectiveness. The installation of sight
glasses may help to reduce the required amount of pipe removal.
- At times, feeding the hose and nozzle in the
preferred reverse direction may be difficult or impossible. An alternative method would
then be to start at the sources (sink traps or floor drains) and work in the direction of
flow. This technique, however, is less desirable because the nozzle head will not be
directly flushing debris as it moves along the piping. It may be necessary, then, to apply
additional water to aid the flushing process by opening faucets in an adjacent sink tied
into the same waste piping line.
- Regardless of the direction that the power wash
nozzle is fed into the system, a final wash and high volume rinse in the direction of flow
may help to flush residual biomass particles from the system.
Chemical Additions
Bleach
Some power washing units are designed for use with water only and do not allow for
addition of chemical solutions. However, it is suggested that a bleach solution be added
to the piping at the source, if possible, to accomplish disinfection of the piping system
immediately before the power washing and to possibly aid in the removal of biomass.
The bleach or other
disinfecting chemical should be analyzed before use to ensure that it is mercury-free or
of a "low" mercury content. Unfortunately, some chemicals and reagents,
including many disinfecting products that contain bleach, can contain measurable
concentrations of mercury.2
Other Cleaning
Solutions
The additions of surfactant, dispersant, caustic and/or wetting agents during power
washing were investigated during the Phase I Mercury Work Group effort. None of these
chemicals were recommended then because of performance and health and safety
considerations. In addition, such chemical additions may be costly for waste piping
systems at large facilities. It is unknown if any local facility has recently accomplished
power washing using chemical augmentation to achieve greater levels of cleaning.
Power Washing Wastewater
Disposal
All Special Waste piping power washing wastewater that contains removed biomass should be
assumed to contain levels of mercury above the MWRA enforcement limit of 1.0 µg/L (ppb)
and, therefore, should be collected for offsite disposal.3
The collection of the power wash wastewater may be difficult, but since power washing will
usually occur during non-operating hours, the Special Waste piping systems can virtually
be drained. Once all normal wastewater flows have been stopped, existing neutralization or
treatment tanks can be emptied and used as power washing wastewater collection vessels.
Additional temporary collection vessels may be needed. However accomplished, it is very
important that the power washing wastewater be collected and not discharged to the MWRA
sewer system.
All waste disposal activities
should be approved by an Environmental, Health and Safety Officer or the person(s)
responsible for waste disposal at the facility. Note that the MWRA prohibits the disposal
of chemicals into the sewerage system except aqueous solutions of nontoxic and
non-hazardous chemicals.4 In addition, the
Massachusetts Department of Environmental Protection (MA-DEP) prohibits the improper
disposal of hazardous wastes.5 The waste
disposal guidelines in Appendix C were developed to reflect both the MWRA and the MA-DEP
regulations and requirements.
RETURN TO HG
MANAGEMENT GUIDEBOOK
TABLE OF CONTENTS
|