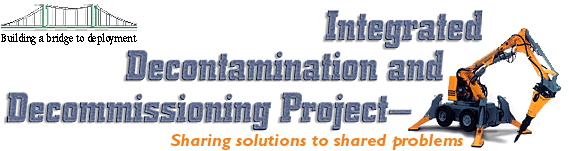 DOEs
Office of Science and Technology is funding the Accelerated Site Technology Deployment
(ASTD) program, formerly known as the Technology Deployment Initiative (see back issues of
Initiatives). Projects in the program promise to reduce the cost of environmental
management and accelerate cleanup throughout the complex.
Surplus DOE facilities with radioactive and hazardous contamination span the range
of construction techniques from concrete block to structural steel to massive
cast-in-place, steel-reinforced concrete. They often contain large amounts of steel piping
and equipment. These facilities need
to be decontaminated and decommissioned for other uses and to reduce the number of
facilities requiring maintenance and surveillance. New technologies exist that could
D&D these facilities more efficiently than the currently used baseline methods, but
the risks inherent in using untried methods tend to encourage traditional technologies. As
a result, although new technologies have been developed and proven in demonstration
projects or industry, their use to D&D facilities in the DOE complex may be limited.
A broad-ranging ASTD project targeting this problem is the Integrated Decontamination
and Decommissioning (ID&D) project, a combined effort of Idaho National Engineering
and Environmental Laboratory, Fernald Environmental Management Project, and Argonne
National LaboratoryEast. The project is increasing the use of innovative but proven
technologies on a large scale in the D&D of facilities in the DOE complex. The three
sites are integrating their efforts through joint planning and reporting, regular
communication, and sharing of technical information and lessons learned.
Each of the chosen innovative technologies has demonstrated
improvements over current baseline methods in cost, schedule, waste generation, radiation
exposure, or safety either in large-scale demonstration projects or through commercial
use, but they have not been used across the board to D&D facilities in the DOE
complex. Doing actual D&D projects with the selected innovative technologies will
build user familiarity and experience with them and add them to the array of tools
available. The increased use of these technologies will generate ongoing cost savings, not
just at these three sites, but at others across the country.
Attacking common problems
The participating facilities present problems typical of decommissioning nuclear
facilities throughout the DOE complex and private industry:
- unknown location of high-intensity radiation or hot spots
- unknown location of underground pipes servicing the facility
- loose, highly radioactive contamination on surfaces and equipment inside buildings
- massive high-density concrete structures
- large amounts of contaminated concrete and oversized metal structures and equipment
- high temperatures and radiation levels, limiting worker stay times
- large volume of waste materials
Facilities with some of these problems were selected at INEEL, FEMP, and ANL-E.
Backing proven winners
After analyzing common needs, the ID&D project team chose to deploy an array of
proven innovative technologies with high potential for benefits in cost, schedule, waste
generation, radiation exposure, or safety.
Initiatives readers will recognize some of these technologies from earlier
stories:
- GammaCam (see Initiatives, April 1997), developed by AIL Systems, Deer
Park, New York, consists of a portable sensor head that contains a gamma-ray imaging
system and a TV camera. The system provides two-dimensional images of a gamma radiation
field superimposed on the corresponding visual image, displayed on a standard portable PC
monitor outside the radiation area.
- Pipe Explorer (see Initiatives, February 1996 and February 1997), developed
by Science and Engineering Associates, Inc., Albuquerque, New Mexico, uses air pressure to
invert a tubular membrane through pipes and around elbows up to several hundred feet,
towing a video camera, characterization sensor, or pipe-locating equipment and providing a
clean conduit for the equipment.
- The Brokk Remote-Controlled Concrete Demolition System (see Initiatives,
Summer 1998, pictured at top of story), manufactured by Holmhed Systems AB, Sweden, deploys
various tool attachments on a remotely operated, articulated, hydraulic boom. The
hydraulic hammer attachment delivers 600 foot-pounds of impact with up to 1500 strokes per
minute.
- The oxygasoline torch (see Initiatives, February 1997), developed by Petrogen
International Ltd., Richmond, California, cuts metal objects significantly faster than
baseline devices and uses less expensive fuel. In addition to improving safety by reducing
exposure through accelerated schedules, the tool reduces blow-through of burning metal
slag.
The other innovative technologies being deployed in
the ID&D project are new to these pages:
- The track-mounted shear/crusher is a marriage of two commercially available and proven
technologies, a track-mounted crawler made by John Deere and a rotating demolition shear
manufactured by Pemberton, Inc., Longwood, Florida. The shear cuts concrete and steel
I-beams up to 18 inches wide. The demonstrated configuration was assembled by Tiger
Machinery Company, Cincinnati, Ohio.
- The self-contained pipe-cutting shear was developed by Lukas Hydraulic GmbH, Germany, as
a mobile rescue tool. Its regrindable drop-forged cutting blades can deliver more than
60,000 pounds of cutting force.
The shear requires no external hydraulic fluid lines, and
its compact size and relatively low weight (50 pounds) enable its use in confined working
spaces. Demonstrated at the Hanford C Reactor Large-Scale Demonstration and Deployment
Project (LSDDP) on steel pipe up to 2½ inches in diameter, the shear leaves clean,
crimped ends, reducing secondary waste and contamination.
- The Personal Ice Cooling System developed by Delta Temax, Inc., Pembroke, Ontario, is a
self-contained core body temperature control system that uses ordinary ice to cool
circulating water. The 13-pound cooling system, demonstrated by the FEMP LSDDP, is
designed to be worn under the first layer of anticontamination garments. Demonstration
results indicate a cost savings of 39 percent over baseline Level C personal protective
equipment ($47/hour per two-person crew) for work area temperatures 7085ºF, and a
66 percent cost savings ($159/crew-hour) for temperatures greater than 85ºF.
- The Decontamination, Decommissioning, and Remediation Optimal Planning System (DDROPS)
is a computer program developed and demonstrated at INEEL. Given information about
facilities or equipment targeted for dismantlement, DDROPS creates a model and recommends
a cutting plan optimized to ensure that the resulting pieces will fit available packaging
with the fewest cuts and least worker exposure. With a second pass, the program recommends
a packing plan that maximizes use of space without exceeding acceptance criteria for
radioactivity. An additional benefit is an inventory documenting each containers
contents and their source. The technology saves costs by minimizing waste volume and
accelerating schedule while protecting worker safety.
The ID&D project already deployed four of these technologies at FEMP in FY98, where
five buildings were decontaminated and decommissioned ahead of schedule, reducing the
mortgage and saving costs. One of these technologies was also deployed at INEEL. During
the next two fiscal years, all of the technologies will eventually be deployed at one or
more of the sites under the ASTD program and used many more times as part of normal
D&D operations.
Problems |
Baselines |
ID&D
technologies |
Deployment
sites |
Unknown location of hot spots |
Manual survey |
GammaCam |
INEEL |
Unknown location of underground pipes |
Exploratory digging |
Pipe Explorer |
INEEL |
Massive concrete structures |
Jackhammer, diamond-wire saw |
Track-mounted shear/crusher |
FEMP |
Contaminated concrete |
Handheld scabbler |
Brokk with scabbler, hammer, and
bucket |
INEEL |
Sizing metal equipment |
Acetylene torch, saws |
Oxygasoline torch, self-contained
pipe-cutting shears, track-mounted shear/crusher, and Brokk with hydraulic shear and
grapple |
INEEL, FEMP, ANL-E |
High temperatures |
Ice vests, reduced stay times |
Personal Ice Cooling System |
INEEL, FEMP, ANL-E |
Large volume of waste |
Unplanned filling of waste boxes by hand |
Decontamination, Decommissioning, and
Remediation Optimal Planning System (DDROPS) |
INEEL |
For further information, contact Dick Meservey, INEEL, (208)
526-1834, rhm@inel.gov or Anne Marie Smith, INEEL,
(208) 526-6877, aqs@inel.gov.Problems
Baselines ID&D technologies Deployment sites |