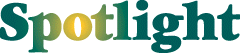 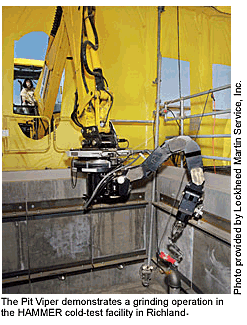
on
the Tanks Focus Area
The nations highest cleanup priority is remediation of nearly
300 radioactive waste tanks at five DOE sites. These tanks hold nearly
90 million gallons of differing waste containing 650 million curies.
Differing waste types and unique compositions require specialized
technologies for safe storage, removal, treatment, and disposal of
tank contents in an environmentally acceptable manner. The Tanks
Focus Area is the central organization within the Office of Science
and Technology managing development and deployment of technology to
close DOE radioactive storage tanks. TFA draws on a broad spectrum
of resources to develop safe, cost-effective solutions to site technology
needs.
Since its establishment in 1994, TFA has enabled the ongoing development
and implementation of approximately 100 technologies, accounting for
approximately 100 deployments. This contribution has resulted in significant
reductions in risk and schedule, with a net cost savings of approximately
$250 million to date. TFA anticipates that savings from future deployments
of existing TFA technical solutions will amount to billions of dollars.
Close interaction with users
TFAs success in implementing new technical solutions is due
in large part to close interaction with cleanup programs managers
and other science and technology programs to bring together valued
expertise, resulting in many deployments and technical assistance
efforts. TFA works to accelerate technology deploymentswhile
reducing environmental management costs and technological riskby
bringing together users and a wide range of technical experts
to define and execute the mission,
integrating work across the sites and other funding organizations,
and
building teams of users and providers to deliver and deploy technical
solutions
The TFA Technical Team is led by Pacific Northwest
National Laboratory (PNNL), which partners with DOE to manage the
program. As the lead laboratory, PNNL coordinates the work of six associated
DOE laboratories and contractors. The Technical Team is responsible
for developing, proposing, and implementing a comprehensive technical
program spanning basic research through commercialization. The team
provides system integration, including assessing technical problems
and site users needs to develop technical responses to meet those
needs.
The Technical Team has established Technology Integration Managers,
who are subject-matter experts in each of the six functional areas of
tank waste remediation: safety, characterization, retrieval, pretreatment,
immobilization, and closure. The TIMs ensure that
a sound technical approach is used to solve users problems,
integrated technical solutions are available to meet users
schedules,
technical solutions are useful to more than one site or one application,
wherever possible, and
users are integrally involved throughout the development of a technical
solution.
Program benefits from independent experts
TFAs Technical Advisory Group, an independent review and advisory
panel, provides a national resource base of experts that can be quickly
accessed to provide review, technical assistance, and support to the
program. Seventeen senior subject-matter experts in tank waste remediation
from industry, universities, and national laboratories serve on the
TAG, whose review and input supports the TIMs in developing and executing
a technically defensible program.
Independent reviews focus on technical feasibility/validity and relevancy
in meeting the needs of users and TFA. These reviews are typically
conducted on "new starts" or projects in the early stages
of the technology maturity cycle. Two types of independent technical
reviews are conductedreviews by the TFA TAG, as well as peer
reviews by the American Society of
Mechanical Engineers as defined under OST guidelines. Relevant
experts selected by ASME perform reviews of proposals, new starts,
and ongoing projects that meet certain requirements.
TFA technical assistance spans the country
The expertise of the TIMs, along with that of the TFA TAG, has resulted
in numerous requests for technical assistance, including the following:
Savannah River SiteTFA is providing direct management of the
Salt Processing Project research and development
effort, including revision of technology roadmaps, development of
technology selection criteria, and preparation
of a comprehensive R&D program plan, in addition to
direct project management of the technology development
activities.
Hanford SiteTFA
is conducting an Advanced High-Level Waste Melter and Waste Products Review
at the request of DOE-HQ to evaluate immobilization improvements or
alternatives that could reduce costs at Hanford.
Idaho National Engineering
and Environmental LaboratoryTFA conducted three independent
reviews to evaluate treatment options for
INEELs tank-related wastes, investigate the technical validity
of a proposed treatment option, and provide technical recommendations
for development of a roadmap for vitrification
of sodium-bearing waste.
Technology developments
Pit Viper reduces radiation exposure at Hanford
Under a project funded by TFA and the DOE Office of River Protection,
Robotics Crosscutting Program
staff at PNNL and Oak Ridge National
Laboratory (ORNL) are developing a robotic Pit Viper system (Tech
ID 2195) that will be used in tank valve pits at the Hanford Site
to remotely retrieve contaminated equipment and clean out contaminated
pits. The Pit Viper system consists of several components, including
a backhoe, control trailer, video equipment, and a dexterous manipulator
arm. This equipment recently underwent testing at
Hanfords Hazardous Material Management and Emergency Response
(HAMMER) cold-test facility.
The French manufacturer of the arm visited Hanford to provide basic
training on the arm and illustrate removal techniques as required
for maintenance, positioning the arm inside the pit mockup, and placing
sleeving on the backhoe boom and the arm. Training on the manipulator
arm by the manufacturer is a key activity in support of deploying
the system at Hanford. This system will reduce personnel exposure,
decrease costs for riser pit decontamination, and enhance riser pit
access to support deployment of tank waste retrieval and transfer
equipment.
Probes help prevent tank leakage at Hanford and Savannah River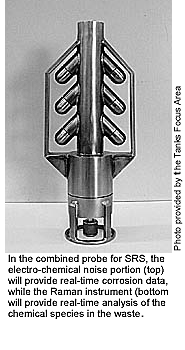
To combat corrosion in double-shell tank walls and improve the corrosion
control process, TFA has worked with partners at the Hanford Site
to develop and deploy an electrochemical noisemonitoring device
called the Corrosion Probe (Tech
ID 1985). This probe listens to the sounds of electrochemical
reactions during the corrosion process and interprets them to detect
the type and extent of corrosion taking place.
For the Savannah River Site (SRS), a corrosioninhibitor monitor
has been developed to continuously measure concentrations of nitrate,
nitrite, and hydroxide ions, which are the key to minimizing corrosion
in steel tanks. Data from this instrumentthe Raman Probe (Tech
ID 2015)minimizes sampling requirements and chemical additions
to the tanks. TFA is funding efforts to integrate the Raman Probe
with the Corrosion Probe to notify operators when corrosion is occurring,
enabling them to take quick and effective actions while minimizing
and refining corrosion inhibitor added to the waste.
Pipeline
plugging prevention
and unplugging
TFA is working with the Characterization,
Monitoring, and Sensor Technology Crosscutting Program and Florida
International University (FIU) to develop a system to reduce the
risk of pipeline plugging during tank waste retrieval activities.
The Dual Coriolis Monitor (Tech
ID 2970) detects weight percent changes in suspended solids by
continuously monitoring the density of tank waste being transferred
through pipelines. This real-time monitored data, coupled with a better
understanding of solids formation and plugging chemistry in pipelines,
will ensure safe and cost-effective retrieval operations. Experience
from an ORNL deployment of the Dual Coriolis Monitoring System in
FY 2000 was integrated into a demonstration test loop at FIU to produce
a prototype planned for deployment at SRS in FY 2002.
TFA is also working with Industry
Programs to sponsor a demonstration of pipeline unplugging methods
at FIU using specially constructed testbeds (Tech
ID 2367). Several effective means of removing simulated blockages
in pipelines were demonstrated. One used sonic resonance to apply
varying vibration frequencies, breaking the bond holding the blockage
to the pipe. Another method used water pressure and scouring inserts
called "pigs" to remove blockages.
|
The latest TFA Innovative Technology Summary Reports give performance
and cost information on the following ready-for-implementation
technologies:
Heel Sampling End Effector
(Tech
ID 2386)
Robotic Tank Inspection End Effector
(Tech
ID 278)
Stereo Viewing System
(Tech
ID 890)
Sludge Washing (Tech ID 233)
Vadose Zone Characterization
System
(Tech
ID 2118)
ITSRs on TFA technologies are available via the Web at http://apps.em.doe.gov/ost/
itsrtfa.html.
|
Processing of vitrification expended material accelerated
The West Valley Demonstration Projects removal and vitrification
of liquid high-level waste from underground tanks generates vitrification
expended material, radiological waste material in the form of
used equipment and instruments that have come into contact with high-level
waste slurry and molten HLW glass. In an Accelerated Site Technology
Deployment effort, TFA has funded the Vitrification Expended Material
Processing System (Tech ID 2383) to sort, segregate, size-reduce,
chemically and radiologically decontaminate, and package all materials
and equipment that have been declared waste.
Accelerated deployment of expended materials processing cuts costs
by reducing the volume of waste requiring management and storage following
vitrification. The system has potential for processing similar waste
already in storage and other high-activity wastes being generated
as part of WVDP. Subsequent deployments are possible at sites that
process HLW, including the Hanford Site, Oak Ridge Reservation, SRS,
and INEEL.
Regenerable HEPA Filter to save time, cost, and exposure at
DOE sites
TFA is partnering with the Savannah River Technology Center High Level
Waste Division and the National
Energy Technology Laboratory to investigate the use of regenerable
filter media on high-level radioactive liquid waste tank exhaust systems.
The media would have filtration performance characteristics equivalent
to conventional disposable high-efficiency particulate air filters.
Westinghouse
Savannah River Company tested two types of filter media: sintered
metal and monolith ceramic. These media were subjected to a hostile
environment to simulate tank ventilation systems conditions. Test
results showed that both filter media were insensitive to high humidity
or moisture conditions and were easily cleaned in situ. The filters
regenerated to approximately clean filter status even after numerous
plugging and in situ cleaning cycles. Both the sintered metal and
ceramic filters passed the challenge test with conventional HEPA filter
efficiency (99.97% or greater) each time.
The sintered metal and ceramic filters not only can be cleaned in
situ, but also hold great potential as a long-life alternative to
conventional HEPA filters. An in situ regenerable system may also
find application in recovering nuclear materials, such as plutonium,
collected on glovebox exhaust HEPA filters. This innovative approach
of an in situ regenerative filtration system may be a significant
improvement upon the shortfalls of conventional disposable HEPA filters
having the potential to significantly reduce cost and personnel risk.
For more information, see the TFA Web site at
http://www.pnl.gov/tfa.
|