Since
July 2000, Lawrence Livermore National
Laboratory has been using a passive, in situ treatment system
known as GeoSiphon (Tech
ID 2063) to remediate groundwater contaminated primarily with
volatile organic compounds. A variant of a permeable reactive barrier,
a GeoSiphon system takes advantage of natural gradient and pressure
differences to induce contaminated groundwater to flow at an accelerated
rate through a permeable reactive medium. At LLNL, the GeoSiphon has
been designed to cause groundwater to flow aboveground into a series
of drums filled with iron filings, where zero-valent iron reduces
trichloroethylene to ethane, ethene, and chloride ions. Nitrate is
reduced to ammonium and possibly nitrogen.
|
Schematic of the
Iron Filings/GeoSiphon Treatment System. |
Graphic provided by Lawrence Livermore
National Laboratory. |
The GeoSiphon concept isnt new. In 1997 and 1998, two DOE
organizations initiated demonstrations at the Savannah
River Site that have contributed to the knowledge base for implementing
this technology. The Office of
Environmental Restoration (now known as the Office of Project
Completion, EM-40) and the Office
of Science and Technology (EM-50) have sponsored demonstrations
of different GeoSiphon configurations at SRSs TNX facility and
in the D-Area, respectively, that have opened the way for a technology
that enjoys distinct advantages over both pump and treat and competing
permeable reactive technologies. GeoSiphon was developed by the Savannah
River Technology Center and is part of the Subsurface Contaminants
Focus Area inventory of technologies for treating groundwater or surface
water contaminated with heavy metals, volatile organic compounds,
or radionuclides.
A general
scheme for siphoning groundwater
A GeoSiphon system is configured to take advantage of significant
natural hydraulic head differences between two points. A siphon is
used to produce a flow between the two points without mechanical pumps.
The up-gradient initiation point is within a contaminated aquifer,
and the down-gradient discharge point can be to the subsurface, the
surface, or a body of water on the surface. The permeable treatment
medium can be placed at the initiation point or the discharge point,
be applied in situ or ex situ, and be either permanent or rechargeable.
Among the reactive media that can be used are granular cast iron,
activated carbon, ion exchange materials, limestone, zeolites, iron
foam, bimetallics, peat, phosphate rock, dolomite, concrete, fly ash,
blast furnace slag, sulfur, or pyrite.
A GeoSiphon system is sustainable and low maintenance, making it
a promising alternative to the higher capital outlay and more expensive
operating and maintenance costs involved in a pump-and-treat solution.
Due to slow contaminant dissolution and/or migration, groundwater
pump-and-treat systems often require extended treatment periods, ranging
from tens to hundreds of years to reduce contaminant levels to regulatory
standards. These extended periods of operation can require significant
energy, resulting in high operating and maintenance costs. A GeoSiphon
system also enjoys advantages over permeable reactive barriers, another
passive, in situ method of removing contaminants from groundwater.
While permeable reactive barriers rely on groundwaters natural flow
rate for transport of contaminants into reactive media, GeoSiphon
systems are designed to enhance natural flow rates and can, therefore,
potentially achieve faster cleanup results.
GeoSiphon
at LLNL
The GeoSiphon system at LLNLs Site 300 has been installed on
the floor of a steep-walled canyon. The contaminated groundwater,
which lies 40 to 60 feet below the canyon floor, contains 70 parts
per billion trichloroethylene, 20 ppb nitrate, and 6.5 ppb perchlorate.
The source area, which is 1,000 feet up canyon of the GeoSiphon treatment
system, contains concentrations of these contaminants two to three
orders of magnitude higher.
At LLNL, a siphon for transporting groundwater toward the treatment
cell is a backup option. The LLNL GeoSiphon system employs three artesian
wells for reaching water that rises to the surface by internal hydrostatic
pressure. The artesian extraction wells have natural flow rates of
5 to 8 gallons per minute and are located at an elevation approximately
30 feet higher topographically and approximately 400 feet up canyon
from the treatment system. In the event of artesian pressure drop,
the wells can be siphoned and the groundwater will flow to the treatment
system by force of gravity.
Four drums filled with zero-valent iron provide primary treatment
of the groundwater. The GeoSiphon system at LLNL is enhanced by the
addition of two granular activated carbon drums that provide secondary
treatment, as well as aerators and sand beds for removing iron oxides.
Accelerated bioremediation is also used as a final treatment to remove
nitrate, with acetate provided as the carbon source.
TNX GeoSiphon
Technical expertise from SRS has contributed to the transfer of this
technology to LLNL. EM-40 provided funding for the worlds first
GeoSiphon, which was installed at the TNX facility in July 1997 to
treat trichloroethylene and carbon tetrachloridecontaminated groundwater.
The TNX GeoSiphon treatment cell is an 8-foot-diameter well, containing
granular cast iron. A siphon passively induces the treated water to
flow from the GeoSiphon cell to the point of discharge, an outfall
ditch draining into the Savannah River. The TNX GeoSiphon is an example
of a presiphon treatment cell configurationgroundwater is first treated
then transported by siphon to the place of discharge.
As a zero-valent iron medium, granular cast iron is an effective
reducing agent in enhancing a reaction known as reductive dechlorination.
Although we do not completely understand the various steps by which
zero-valent iron degrades trichloroethylene (a chlorinated volatile
organic compound, or CVOC) into its final reaction productsethane,
ethane, and chloride ions, we do know that providing contaminated
groundwater with sufficient contact time with zero-valent iron reduces
CVOCs to intermediate and final degradation products.
During testing at the TNX GeoSiphon, approximately 49.7 tons of granular
cast iron was used in the treatment cell, and flow rates were manipulated
with pumping to determine the maximum acceptable treatment flow rate
that allowed reduction of 200 micrograms per liter (mg/l) trichloroethylene
to below drinking water standards (5 mg/l). The maximum acceptable
treatment flow rate was found to be between 7.8 and 8.3 gallons per
minute. During Phase II testing, the actual flow rate with an optimized
siphon configuration was found to average 2.62 gallons per minute,
resulting from a head differential of approximately 1.43 feet between
the cell and the outfall ditch, the point of discharge. A new siphon
line to increase the head differential and induce a treatment flow
rate that more closely matches the maximum acceptable treatment flow
rate will increase the efficiency of the system.
D-Area
GeoSiphon
During FY9899, EM-50 funded a full-scale pilot test of a GeoSiphon
system at Savannah Rivers D-Area Coal Pile Runoff Basin, a 12.5-acre
basin that received acidic runoff contaminated with metals and sulfate
from the 8.9-acre D-Area coal pile. Seepage from the basin resulted
in groundwater contaminated with ferrous iron, aluminum, nickel, chromium,
and other metals.
As used here, head is the pressure on a liquid
arising from a difference in elevations, expressed in feet (cubic
feet of water in a column). One foot is about 0.43 pounds per
square inch. |
The treatment system was designed to be two-stage. Groundwater flowed
below ground into a limestone-filled trench, the primary treatment
cell, where aluminum and chromium were precipitated. Receiving the
groundwater through a siphon line, the secondary treatment cell oxidized,
precipitated, and collected the remaining metal contaminants, mostly
iron and nickel. The natural head difference of less than 5 feet between
the up-gradient limestone trench and the discharge point into the
secondary treatment cell, induced groundwater to flow through the
D-Area GeoSiphon system. With a siphon connecting two treatment cells,
the D-Area GeoSiphon can be thought of as combining both presiphon
and postsiphon treatment cell configurations.
The limestone trench raised the groundwater pH, which caused the
precipitation of dissolved metals, primarily aluminum and chromium.
The partially treated groundwater was then transferred by natural
siphon to a downstream settling container. The supernatant from the
settling container moved to a secondary treatment system, where iron
and nickel were oxidized, precipitated, and settled. The treated water
was then discharged to a man-made stream that flowed to a permitted
surface water outfall.
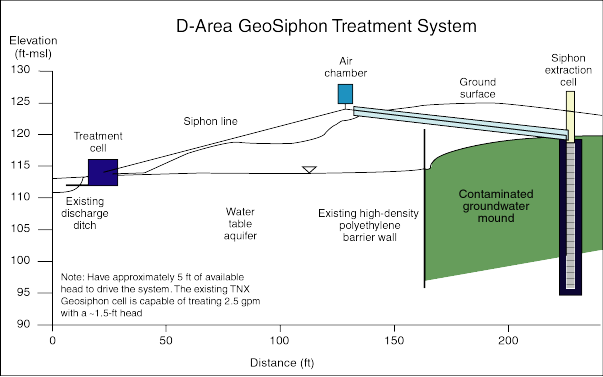 |
The D-Area GeoSiphon
is an example of a postsiphon treatment cell configuration. |
Graphic provided by
Savannah River Site |
During testing of the D-Area GeoSiphon, several siphon configurations
were evaluated as well as the capability of several oxidants and bases
to oxidize iron and raise pH in the secondary stage. The most effective
reactants for the secondary stage were found to be calcium peroxide
and hydrogen peroxide/sodium carbonate.
Ready,
set, siphon!
The GeoSiphon has broad applicability in a number of configurations.
Testing at Savannah River Sites TNX facility demonstrated its
treatment of VOCs using a zero-valent iron medium. The configuration
at the D-Area, with limestone and oxygen-generation compounds, shows
that the technology aids in metals remediation and may also remediate
the VOC-portion of contaminated groundwater simultaneously. Westinghouse
Savannah River Co. has a patent pending for the GeoSiphon technology.
Mark Phifer, an engineer at the Savannah River Technology Center,
has been instrumental in this technologys deployments at Savannah
River and Lawrence Livermore and is available to help other sites
that are considering a GeoSiphon. For Phifer, the beauty of a GeoSiphon
is its synergy with nature. Rather than looking at the natural
environment as something to overcome, the GeoSiphon concept looks
for and works with existing natural energy potentials to achieve groundwater
cleanup.
For more information on the GeoSiphon, contact Mark Phifer at
the Savannah River Technology Center at (803) 725-5222, or mark.phifer@srs.gov.
|