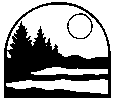 |
Office of Technical Assistance Executive
Office of Environmental Affairs Commonwealth of
Massachusetts |
Toxics Use Reduction Case Study
1,1,1 Trichloroethane Elimination At Hardigg
Industries
Summary
Customer pressure, employee concern and the new Federal labeling
requirements for Class I ozone depleting chemicals (ODC) combined to
motivate Hardigg Industries to eliminate 1,1,1 trichloroethane (TCA) from
its manufacturing operations. This was accomplished after six months of
testing and experimentation in two procedures using TCA-based agents. In
cleaning operations, Hardigg was able to replace TCA with water soluble
cleaners. A nonhazardous compound was substituted for a TCA-based mold
release. Hardigg's previous annual average emissions of 11,082 pounds of
TCA have now been eliminated.
Background
Hardigg, a 210-employee company in South Deerfield, Massachusetts,
manufactures plastic containers using rotational, injection and blow
molding techniques. TCA was used in several process areas. To facilitate
removal of the containers, a TCA-based release was wiped onto the molds
prior to addition of the plastic pellets. Elsewhere, a dip tank cleaning
operation used TCA to remove cutting oils and metal fines from machined
metal hinges and locks. In a third area, following assembly of the metal
parts and plastic containers, grease and oils were removed by wiping the
products with a TCA-based cleaner. In all operations, TCA was allowed to
evaporate from the parts, releasing the chemical to the atmosphere where
it has contributed to the destruction of the ozone layer.
Toxic Use Reduction
At Hardigg, each employee is an Associate, and is included in all
phases of the manufacturing process, including problem solving. The
Hardigg Associates spearheaded the substitution of nonhazardous
alternatives for TCA because they had environmental concerns and they
found the odor objectionable. Also Hardigg's customers did not want a
product delivered with a label stating that it had been manufactured with
a Class I ODC as required by the new Clean Air Act Amendments. Hardigg
worked with their vendors to select several alternatives to TCA and began
approximately four months of trials and destructive testing in order to
assure quality. The new cleaner had to be compatible with the plastic
substrate and could not contain dyes which might penetrate and color the
parts.
Hardigg's cleaning tests found a water-soluble cleaner that was
comparable to TCA. In the dip cleaning operations, a new water-based
cleaning machine was installed at a cost of $3,500. While the new cleaner
is an effective substitute for TCA, cleaning takes longer and additional
drying time is needed.
The first TCA substitute used for the final wipe of the containers also
required longer cleaning times and caused a problem with residues. Hardigg
located another substitute which combined with vigorous wiping, solved the
residue problem.
The new mold release agent -- a water-based emulsion -- was a direct
substitute for the TCA-based product. This nonhazardous replacement
functions as effectively as TCA in preventing the plastic containers from
adhering to the mold.
Results
Reductions Achieved: The "alternative" water-soluble cleaner and
nonhazardous mold release agent have completely eliminated TCA use at
Hardigg, which was 11,082 pounds the previous year. Use of these
alternatives has reduced Hardigg's environmental reporting and compliance
requirements and their associated costs.
Economics: Hardigg installed new machines for the dip cleaning
operation at a cost of $3,500. The new mold release agent has not added to
production costs beyond the labor and materials expended during the
testing period. Hardigg's labor costs have risen because the new cleaner
does not evaporate as quickly as TCA and workers spend more time removing
residual cleaner. However, by meeting the demand for non-ozone depleting
chemicals, Hardigg satisfied its customers and retained their business.
This case study is one in a series prepared by
the Office of Technical Assistance (OTA), a branch of the Massachusetts
Executive Office of Environmental Affairs. OTA's mission is to assist
industry in reducing the use of toxic chemicals and/or the generation of
toxic manufacturing byproducts. Mention of any particular equipment or
proprietary technology does not represent an endorsement of these products
by the Commonwealth of Massachusetts. This information is available in
alternate formats upon request. OTA's confidential, non-regulatory
services are available at no charge to Massachusetts businesses and
institutions that use toxics. For further information about this or other
case studies, or about OTA's technical assistance services, contact:
Office of Technical Assistance, 100 Cambridge Street, Room 2109, Boston,
Massachusetts 02202. Phone #(617)727-3260. Fax #(617)727-3827. Website:
http://www.magnet.state.ma.us/ota.
|