
|
Fort McCoy
A Comprehensive Environmental
Management Program to Minimize and Prevent Waste. |
Standard Industrial Classification
(SIC) |
Military Base |
Type of Waste |
Air emissions, wastewater, hazardous waste,
solid waste |
Strategy |
Comprehensive environmental management
program |
Company Background |
Fort McCoy was established in 1909 and
presently has approximately 2,200 civilian employees and 300 active military personnel.
Fort McCoy provides training for active and reserve military units. Fort McCoy's
Directorate of Public Works (DPW) is the organization responsible for ensuring that all
installation activities related to operations, training and construction comply with all
applicable federal, state and local environmental and cultural resource laws and
regulations. The DPW Environmental and Natural Resources Division (ENRD) coordinates and
executes programs for Fort McCoy, and supports U.S. Army Reserve Centers located in
Wisconsin, Minnesota, Michigan, Illinois, northern Indiana and Ohio. |
Motivation |
The initial focus was regulatory compliance
which evolved into exploration of alternative processes to meet budgetary challenges. |
Pollution Prevention Process |
Fort McCoy developed a comprehensive
environmental management program to achieve significant reductions in hazardous waste, air
emissions, wastewater and solid waste by implementing recycling programs, material
substitutions, source reduction and process modifications. Hazardous
Waste
- Paint Removal System
Replaced a sand-blasting paint removal system with an aluminum oxide pellet-blasting
system in 1993. The metal pellets can be reused up to 15 times before being sent off-site
for treatment and disposal as solid waste. The sand from the old system could not be
reused and was considered hazardous waste because of the presence of heavy metals from the
paints. The old system generated about 12 tons a week of hazardous waste as opposed to
only one ton a week of hazardous waste with the new system.
Air Emissions
- Gas Furnace Conversion
Fort McCoy replaced between 3,000 and 4,000 coal-fired boilers with natural gas or liquid
propane fuel furnaces between the years 1989 and 1995. This eliminated the use of 6,500
tons of coal per year. Subsequent reductions in emissions are summarized below.
Emission |
1990* |
1994* |
1995 |
Average
Percent Reduction |
Sulfur dioxide |
97 |
5 |
1 |
97% |
Particulates |
61 |
5 |
3 |
93% |
Nitrogen oxides |
23 |
2 |
13 |
67% |
Carbon monoxide |
147 |
3 |
4 |
98% |
Inhalable particulate matter |
12 |
3 |
3 |
75% |
Reactive organic gas |
18 |
0.5 |
11 |
67% |
* values are expressed in tons/year |
- HVLP Paint Guns
Fort McCoy installed High Volume/Low Pressure (HVLP) paint guns that reduce overspray and
Volatile Organic Compound (VOC) emissions by approximately 50 percent, or 8,750 pounds per
year. This resulted in lower material costs, less solvent usage and fewer changes of paint
booth filters.
Wastewater
- New Vehicle Wash Facility
Fort McCoy uses more than five million gallons of water per year to wash vehicles.
Previously Fort McCoy discharged all of this water to its wastewater treatment plant, but
has recently completed a new wash facility that reuses about 98 percent of the wash
water. The wash water is collected, sent to settling basins, filtered and then reused.
This process reduces loadings to the wastewater treatment plant and conserves water.
Solid Waste
- Land Application of Sludge
Fort McCoy began land-applying its wastewater treatment sludge to areas of the base
undergoing revegetation work. Prior to this, the sludge had been disposed of at a solid
waste landfill. To date, 466 tons of sludge has been land-applied. This has reduced
landfill costs and extended the life of the landfill, while benefiting from a valuable
soil conditioner.
- Metal Recycling Program
Fort McCoy has established a metal recycling program for PCB-containing and
non-PCB electrical transformers. Fort McCoy sends the PCB-containing equipment
off-site where the fluid is drained and the casing is decontaminated. The oil is
incinerated and the cleaned metal is then recycled. The non-PCB equipment can be directly
recycled. The project has recycled approximately 100,000 pounds of valuable metals.
- Motor Oil Absorbent Management
Fort McCoy had previously disposed of its clay based absorbent after each use. This
material subsequently would be shipped off-site for landfill disposal. Since 1991, motor
oil absorbent is reused on-site until the absorbent is fully saturated. The absorbent is
then treated on-site in bio-piles. If significant reductions do not occur on-site, the
material is shipped off-site for further biodegradation prior to thin spreading. This
management strategy had reduced the total amount of absorbent used on-site therefore
reducing the volume of material for treatment.
- Recycling Motor Coolants
In 1996, Fort McCoy began recycling its motor coolants (anti-freeze). The
coolants are collected and outside recycling vendor processes the recovered anti-freeze
for reuse at the Fort.
|
Economics |
Disposal Cost (old method) |
$237,120/year |
Disposal Cost (new method) |
$19,750/year |
Disposal Cost Savings |
$217,370/year |
- High Volume/Low Pressure Paint Guns (HVLP)
Approximate savings |
$30,000/year |
- Land Application of Sludge
Type |
Old Process* |
New Process* |
Costs |
Landfill tipping fees |
$44.00 |
0 |
$44.00 |
Labor |
0 |
($7.50) |
($7.50) |
Equipment |
0 |
($7.00) |
($7.00) |
*values are expressed per ton |
Total |
$29.50 |
Cost Savings = 466 tons at
$29.50/ton or $13,750 (to date) |
Estimated Disposal Cost Savings |
$75,000, to date |
- Recycled Motor Oil Absorbent
Approximate Savings |
$17,850/year |
Type |
Old Process |
New Process |
Costs |
Product |
$5.50 |
0 |
$5.50 |
Disposal |
$6.50 |
0 |
$6.50 |
Recycle |
0 |
$2.00 |
($2.00) |
* values are expressed per gallon |
Total |
$10.00 |
Cost savings = 315 gallons at $10/gal or
$3,150 (to date) |
|
In Development |
- Biodegradation of Petroleum-contaminated Soil
In 1995, Fort McCoy began experimenting with the use of naturally-occurring bacteria
to biodegrade petroleum contamination in soil. The process involves mixing contaminated
soil, wood chips (which serve as a bulking agent) and a nutrient source. This material is
placed outdoors in covered rows and oxygen is supplied via perforated piping. The
experiment is not yet complete and will require further adjustments to the moisture and
oxygen content. If the project is able to remove sufficient petroleum contamination, Fort
McCoy estimates that treatment through this method will cost $20 to $25 per ton, versus
$50 per ton for asphalt incorporation.
- Ultraviolet Disinfection
Currently, Fort McCoy uses chlorine to disinfect its wastewater. By early 1997,
Fort McCoy will replace this system with one that uses ultraviolet light. The new
system will eliminate an estimated 1,200 pounds per year of chlorine discharges to the
environment. By changing this process, Fort McCoy eliminates Tier II (EPCRA) reporting
requirement and saves on the procurement of chlorine and sulfur dioxide.
|
Benefits |
This comprehensive environmental management
program has resulted in overall cost savings, reduced volume of wastes to landfills,
reduced worker exposure to hazardous chemicals, reduced fire hazards and lowered
pollutant-loadings to the environment. |
Additional Waste Reduction
Activities |
Fort McCoy hosted the DNR's one-day
Vehicle Maintenance Industry Pollution Prevention Workshop, providing facilities and
advertising for the event. Over 150 people attended from the general public, state
government and Army. Topics included a regulatory update and ideas for recycling and waste
minimization programs for the vehicle maintenance industry. In 1989, Fort McCoy
tested 94 of its approximately 1,800 buildings for radon. All of the tests found levels of
radon far below the EPA standard. Fort McCoy sponsored a hazardous waste clean sweep
within the base in the summer of 1995, gathering 7,921 pounds of hazardous materials
(paints, solvents, batteries, and acids). |
Company Address |
Commander Headquarters Fort McCoy
100 E. Headquarters Road
Fort McCoy, Wisconsin 54656-5263 |
Contact Person |
Steven Stokke, Environmental Protection
Specialist
608/388-4790 |
Pollution Prevention Resources |
Free, On-site Technical Assistance
University of Wisconsin Extension
Solid and Hazardous Waste Education Center
Milwaukee area: 414/475-2845
Remainder of state: 608/262-0385Industrial Waste
Reduction Information Clearinghouse
Wisconsin Department of Natural Resources
Bureau of Environmental Cooperative Assistance
608/267-9700 or e-mail: cea@dnr.state.wi.us |
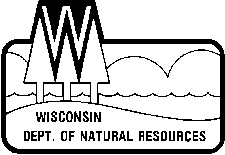 |
Bureau of Cooperative Environmental Assistance
Wisconsin Department of Natural Resources
P.O. Box 7921
Madison, WI 53707
608/267-9700
TS-061 96 |
|