"Precision Cleaning - The Magazine of Critical Cleaning
Technology"
Parts Cleaning Carbon Dioxide Snow Examination and Experimentation
by: Elizabeth A. Hill
Pages: 36 - 39; February, 1994
When liquid carbon dioxide (CO2) is allowed to expand to
atmospheric pressure through a nozzle, a portion of the CO2 freezes,
forming soft flakes. Spray cleaning surfaces with this CO2
"snow" has been shown to remove particles and other debris without
damage.
This technique was initially proposed for precision cleaning applications
more than five years ago.1 Since then it has been used on component
surfaces of instruments ranging from telescopes2 to vacuum
systems.3
Carbon dioxide snow can also be compressed into hard pellets that are
propelled toward a surface with high-pressure gas as a carrier. In this form,
the pellet process resembles sandblasting and can remove paint and rust. Care
must be taken with pellet blasting, however, to avoid physical damage to the
surface being sprayed.
This article focuses on the gentler, snow cleaning process.
Various Advantages, Various Approaches
One advantage of CO2 cleaning is that the snow sublimes, leaving
behind as waste only the removed debris. This can greatly reduce waste disposal
costs. Other advantages are that the equipment and process for cleaning with
CO2 snow are very simple and relatively inexpensive.
Carbon dioxide is nontoxic, nonflammable, and does not deplete the ozone
layer. It is a greenhouse-warming gas, but is collected as a by-product of
other processes, so there is no net increase of carbon dioxide emissions into
the atmosphere.
Snow made from water or argon also have been used for surface
cleaning.4,5 When using water snow, the parts being cleaned become
wet and must be dried in subsequent process steps.
The water-based snow cleaning process must be performed in an area where the
resulting liquid can be controlled and collected. The major advantages of this
method are that water is readily available in high purity and is not a
greenhouse warming material.
Argon had identical advantages. However, argon snow (-189.3° C freezing point) is much colder than
CO2 snow (-78.5° C freezing point),
so thermal shock and chilling of the parts is more of a problem.
With both water snow and argon snow, more equipment is needed to operate the
process than with CO2 snow. For argon snow, the argon gas must be
precooled and pressurized prior to expansion, or the snow will not form. The
process also is carried out in a vacuum chamber to prevent condensation on the
part. It is usually performed under partial vacuum to maintain the argon
particles in a solid state and allow then to reach the surface more
effectively. CO2 snow requires only a liquid carbon dioxide source
and nozzle.
Experimental Setup and Procedures
High-purity CO2 in a standard 50-pound, 800 psi tank was used for
these experiments. A nozzle or snow gun was attached to the tank with a
braided, stainless steel-jacketed hose. A purifier was connected in series
between the tank and gun. The gas used in most tests was Air Products and
Chemicals' (Allentown, Pa.) high-purity grade. The nozzle and purifier were
supplied by Va-Tran Systems, (Chula Vista, Calif.).
The surfaces cleaned in these experiments were unpatterned silicon wafers.
Particles on the wafer surfaces were counted and sized with an Aeronca WIS-150
laser wafer scanner before and after snow cleaning.
Particle removal experiments were performed on wafers pre-contaminated with
0.31, 0.50, and 0.94 micron polystyrene latex (PSL) microspheres and Arizona
fine test dust. The contaminants were deposited on the wafers by producing a
cloud of the particles above the wafers and letting it settle on them. Addition
of other contaminants was measured on clean wafers (no pre-contaminated with
particles), also with the WIS-150.
To begin a cleaning cycle, the nozzle valve was opened. Gas flowed from the
system until it cooled to the point where snow was produced. One snow was
spraying from the gun at a steady rate, it was directed at the parts being
cleaned.
The operator moved the gun across the surface in a manner similar to washing
a car with a hose. For all tests, the nozzle's tip was positioned at a standard
45° angle approximately 3 inches from the
surface. As long as the snow hit all surfaces to be cleaned, distance and angle
were not critical. A standard cleaning cycle lasted 10 seconds.
Removal of Particles
Figure 1 shows the percent of particles removed from the wafer. Error
bars for +/- one standard deviation (sigma) are included.
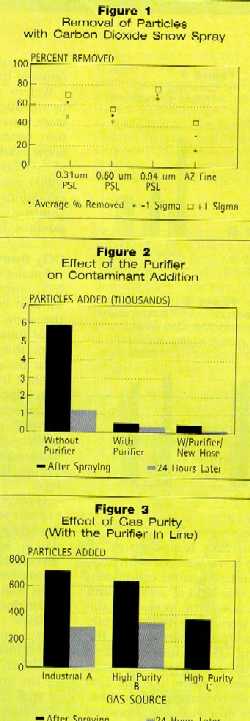
The CO2 snow removed 55 to 75 percent of the PSL microspheres;
about 32 percent of the Arizona fine test dust was removed. The latter
particles have a maximum size of 176 microns, with more than 50 percent of the
particles being smaller than 10 microns, and 18.2 percent smaller than 2.8
microns. The initial loading of Arizona fine test dust on the wafers was very
heavy.
The true particle removal percentages were probably slightly higher than
those shown here. Some addition of contaminants from the CO2 was
occurring concurrently with the cleaning, but every effort was made to minimize
this problem during these tests.
These values are indicative of the process capability, since the desired
result is the lowest overall particle count possible, whether from prior
contamination or that from the cleaning process. The next experiments in this
study focused on the material being added to the wafers by the CO2
and methods to reduce or eliminate it.
Addition of Contaminants
The snow cleaning process currently does add some contamination to the parts
being cleaned -- seen on the wafer surfaces as very small, thin droplets, most
of which are less than 0.5 microns in diameter.
The wafer scanner does detect them and counts them as particles. The
droplets are not easily seen with a light microscope because they are small and
widely dispersed on the surface. Nomarski polarization is helpful. A Scanning
Electron Microscope (SEM) does not detect the droplets, possibly because they
are not stable in vacuum or are destroyed by the electron beam.
Much of the material is volatile. Therefore, all data reported in this
section include particles added to the wafers as measured immediately after
spray cleaning, and as remeasured 24 hours later. The sources of this
contamination were traced to the gas supply and some of the components in the
cleaning apparatus. A purifier was used in these experiments to reduce the
contamination.
Figure 2 shows the addition of particles to the wafer with the
without the purifier in line. The purifier reduced the amount of contamination
from the gas sources by 75 to 90 percent. The major portion of the remaining
material was identified as phthalic and aliphatic esters, traced to a hose
upstream of the purifier. Upon replacement with a teflon-lined hose,
contamination reduction improved to 90 to 94 percent. There is still a small
amount of contamination added, but efforts are currently underway to eliminate
this as well.
Effects of Gas Purity, Enclosed Cleaning
Figure 3 shows the effect of gas purity. Three different gas sources
were tested: "A" was an industrial grade; "B" and
"C" were high-purity gas sources from different suppliers. All three
were used with the purifier in line.
The wafers from gas "C" were not scanned after 24 hours, so the
graph includes no data for that gas source. Small differences in the amounts of
contamination added to the wafers from the different gas sources were much
greater without the purifier in line. This shows that the purifier is effective
in reducing contaminants from the gas but that gas quality is still important.
Figure 4 shows the effect of cleaning inside an enclosed space.
Wafers were placed on a support inside a stainless steel vacuum chamber, and
the snow gun nozzle was fixtured through the chamber wall. All other conditions
were maintained. No vacuum was pulled in these tests. The wafers cleaned out in
the open were placed on a support several inches above the surface of a table
so that the snow slid off the wafer as it cleaned. Cleaning in the open results
in much less addition of contamination than in an enclosure.
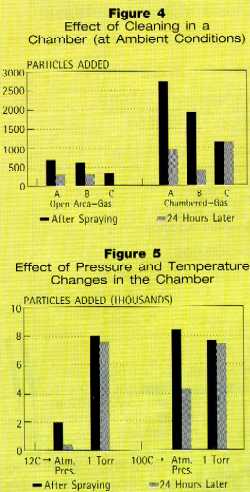
The most striking result was that the snow cleaning the wafers
simultaneously cleaned the walls of the vacuum chamber. The snow spray aimed at
the wafer would bounce off the wafer and swirl around in the chamber. Some
flakes than hit the chamber walls and rebounded back onto the wafer, depositing
contamination.
Effect of Pressure and Temperature
To study the snow cleaning mechanism, wafers were sprayed while at two
temperatures and two pressures.
The first cleaning tests were done in an open area. Wafers were mounted on
heating blocks and cleaned while maintained at 15° C and 100° C. There
were no significant differences in the amounts of contamination added to wafer
surfaces.
Next, clean wafers were placed in a vacuum chamber. The temperature of the
wafers was held at 12° C and 100° C for these tests. Figure 5 shows the
results of cleaning wafers in the vacuum chamber while at the two temperatures
and pressures.
When the wafers inside the chamber were heated to 100° C on a heating block, the added contamination was
much greater than at the lower temperature. This may be attribute primarily to
chamber wall cleaning as well as increased phase change at the wafer surface
due to the higher surface temperature.
Wafers also were sprayed with CO2 snow while under vacuum
conditions. The pressure was held at ambient and 1 torr. At atmospheric
pressure, the snow flakes were large and discrete, and could easily be seen
during spray cleaning. At vacuum of 1 torr, the snow particles were very small
and indiscrete, looking more like fog. Low pressure inhibits coagulation of
particles.
Many more droplets were deposited on the wafer surfaces in vacuum, and a
much larger percentage of those remained on the surfaces 24 hours later. This
may have been thermal mass and more surface area to volume, changes phase at
the surface of the part being cleaned, dropping the contaminants from the gas
source. The source of the increase in solid, non-volatile particles appeared to
be debris removed from the inside of the chamber.
Wafers cleaned with both elevated temperature and reduced pressure also were
heavily contaminated. It appears that conditions producing short-lived snow
flakes (vacuum or the combination of a heated substrate and enclosing walls)
should be avoided, as well as conditions where the snow flake is contaminated
prior to reaching the surface being cleaned.
CO2 Snow Cleaning Mechanisms
Among two possible mechanisms for CO2 snow cleaning is transfer
of kinetic energy by physical contact of the snow flakes with the particles. A
flake must hit a particle and knock it from the surface. The particle must then
be entrained in the gas jet and flushed from the surface being cleaned. It is
important for solid snow flakes to be present in the CO2 gas jet. A
gas blow-off alone will only remove large particles, leaving smaller particles
behind in the area of low gas velocity near the surface known as the boundary
layer.
However, this mechanism does not explain some of the experimental findings
described in the next paragraphs, which leads to the next proposed mechanism: a
combination of shear stress forces and thermophoresis.
In this explanation, the solid snow flake does not physically contact the
particle or the surface being cleaned. The approaching snow flake is separated
from the surface by a cushion of cold CO2 gas produced by
sublimation of the snow flake. There may even be a thin layer of liquid or
supercritical CO2 between the solid CO2 and the gas
during the brief time the flake is nearest to the surface.
Particles on the surface being cleaned are exposed to shear stresses from
two sources. The first is the gas flowing from the nozzle. However, the force
of this gas is not dominant or even required in this removal mechanism.
The second and more important source of shear stress energy is the rapid
expansion of carbon dioxide as the snow flake changes phase from solid to gas.
As the cold snow flake approaches the surface it is exposed to a large, much
warmer thermal mass (the surface). The solid snow rapidly changes phase on the
side nearest to the surface.
There is a very small distance between the flake and the surface for this
material to expand in as it changes to gas, so a high velocity burst is
created. This explosive phase change occurring in the small distance between
the snow flake and the surface provides the force necessary to dislodge the
particle.
One the particle is dislodged it is attracted and held to the snow flake by
thermophoretic forces. Thermophoresis refers to the force on a particle due to
a thermal gradient. The kinetic energy of air molecules on the cool side of a
particle is less than on the warm side. Therefore, warm air molecules
"push" the particle in the cool direction. The greater temperature
difference and the smaller the distance between warm and cold points, the
stronger the force.
With snow cleaning, there is approximately 100° C difference in temperature over the distance of a
few microns or less. Thermophoretic forces are usually incapable of overcoming
particle-to-surface adhesion, but are strong enough to account for entrapment
of particles in the snow flakes. These particles are held to the snow flake as
long as it remains in solid phase, and will be deposited when the change to gas
phase is complete.
This hypothesis is supported by several experimental observations. First,
when large snow flakes (roughly one-eighth-inch diameter and up) are sprayed up
into the air and allowed to settle back onto the surface being cleaned, the
particles are still removed. This eliminates the shear forces due to the gas
flow from the nozzle.
Second, particles removed from a surface by snow flakes are redeposited
wherever the snow finally changes back to the gas phase. A small pile of snow
flakes can be collected and picked up with a spatula. If this pile is placed on
a contaminated surface and then lifted off again, the particles are removed
from the surface. If the same snow pile is then placed on a clean surface and
allowed to sit until it sublimes, the particles are redeposited at that point.
Some nozzles produce a small jet of high-velocity, small snow flakes. Others
produce large qualities of large, low-velocity snow flakes. Experience has
shown that different cleaning results are obtained with the two types of snow
nozzles. This may be due to differences in the dominant cleaning mechanism.
Nozzles producing higher velocity jets with smaller snow flakes may result in
more kinetic cleaning, while the forces from larger snow flakes may be due to
thermophoretic cleaning.
Conclusions
Carbon dioxide snow cleaning is effective for particle removal, and should
be considered among alternative cleaning processes.
The best cleaning is obtained when using high-purity gases and mechanical
components. Cleaning should be performed at room temperature and ambient
pressure. Surfaces should be cleaned with smooth, quick strokes. The snow must
be allowed to leave the surface being cleaned before it changes to the gas
phase.
The CO2 cleans everything it contacts, including the inside of
the gas tank, the hoses, and nozzles in the cleaning apparatus. Therefore, all
components in the gas delivery system and spray nozzle must be clean. The inner
surfaces of the hoses and nozzles must be as smooth as possible and be made of
non-flaking and non-leaching materials. Use of dedicated gas tanks and system
components is highly recommended to maintain cleanliness.
The main challenge with this technique as it stands today is eliminating the
last microdroplets of contamination, identified as being primarily from the
CO2 gas itself. If this flaw can be eliminated, CO2
cleaning will be feasible for many processes requiring very high levels of
cleanliness.
In the meantime, CO2 cleaning is still viable for many processes,
such as removal of packaging debris, cleaning of equipment before entry into
cleanrooms, and removal of particles from surfaces where submicro organic
droplets will not harm product submission.
References
1. S.A. Hoenig, "Cleaning Surfaces with Dry Ice,"
Compressed Air Magazine, No. 8,9122-24, August 1986.
2. R.R. Zito, "Cleaning Large Optics with CO2 Snow",
SPIE, Vol. 1236 Advanced Technology Optical Telescopes IV 1990.
3. L. Layden and D. Wadlow, "High Velocity Carbon Dioxide Snow for
Cleaning Vacuum System Surfaces," J.Vac Sci. Technol., A 8 (5), 3881-3883,
Sept./Oct. 1990.
4. T. Ohmori, I. Kanno, T. Fukumoto, H. Komiya, M. Tada, T. Kawaguti,
"Ultra Clean Ice Particles," J. Electrochem. Soc. 137, 399C,
1989.
5. W. T. McDermott, R. C. Ockovic, J. J. Wu, R. J. Miller, "Surface
Cleaning by a Cryogenic Argon Aerosol," Proc. Of the IES. 882-885,
1991.
Acknowledgments
The author wishes to thank the sponsors and affiliates of the Surface
Cleaning Technology Consortium (SCTC) and the Research Triangle Institute who
jointly supported this work. Sponsors included IBM, Fujitsu, Kobe Steel Ltd.,
and Storage Technology Corp. Affiliates included Allied-Signal, Crest
Ultrasonics, The J.M. Ney Co., TSI Inc., UVOCS, Va-Tran Systems, and Verteq.
The CO2 snow equipment was provided by Va-Trans Systems. In
addition, the support of the surface cleaning laboratory staff is greatly
appreciated.
About the Author
Elizabeth A. Hill is the program manager for the Surface Cleaning
Technology Program in the Center for Aerosol Technology at Research Triangle
Institute (RTI), N.C. She received bachelor's (1978) and master's (1981)
degrees in analytical chemistry from Northern Illinois University and the
University of Colorado, respectively. Before joining RTI, she gained seven
years of industrial experience in precision surface cleaning and contamination
control as a development and manufacturing engineer in the computer disk drive
industry.
Best Conditions for Snow Cleaning
The following conditions enhance particle removal and minimize contaminant
addition.
- Use a high-purity gas source.
- Use a purifier in-line for additional purity and quality control.
- Clean at ambient temperature and pressure.
- Clean in an open area so that the snow strikes only the part being cleaned
and can be collected before it changes phase.
- Move the nozzle slowly and smoothly across the surface once, making sure
that the snow does not pile up on the part being cleaned. Cleaning is not
improved by holding the gun closed to the surface or holding it in one place
for a long time. Further exposure only chills the part being cleaned and
produces additional gas-sourced contamination.
- Ensure that there are no materials in the cleaning system that could leach
organics into the CO2.
|